Anti-Static Epoxy Flooring – Method and Application
Anti-static epoxy flooring is preferred over other flooring methods when it is required to provide a floor having joint-free finishes along with high chemical resistance and decorative properties. Anti-static epoxy flooring is mostly used in electronic and telecommunication industries, automotive industries, pharmaceutical factories, aerospace industries, operation theatres, computer rooms etc.
In order to prepare a high performing coat, good substrate preparation is pivotal. The surface of the concrete over which the coat has to be laid must be hard, sound and free of dust and other barrier materials such as paint, lime, coatings, plaster, curing agents, laitance and other adhesive residues.
Anti-Static Epoxy Flooring Method
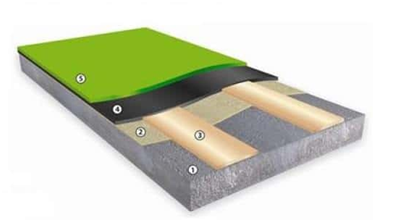
Layer-Arrangement of Anti-Static Epoxy Flooring
1) Surface preparation
All Substrates should be dry (max. 5% moisture content), clean, sound and free of laitance. Surface grinders and shot blasting are used to prepare the surface; the surface should be properly cleaned and should be free from dust prior to application of primer.
2) Priming
It is imperative that the Primer-contents are thoroughly premixed prior to mixing together. The contents are mixed slowly using a slow speed drill and paddle for at least 4 minutes. Primer is then applied on the dry concrete surface @ 0.2 to 0.25Kg/per square meter by Brush/Roller.
3) Laying of copper Tape
A copper strip of required width and thickness is laid. The butter paper is firstly removed and the adhesive side of the copper strip is kept exposed. Stick the self-adhesive copper strip on to the clean primed substrate at a distance of 1 to 4 meter to each other, lengthwise and breadth wise.
At the periphery, near to the walls, stick the self-adhesive copper strip at a distance of 6 inches from the walls. At any one end in the room, copper strip should be extended out for connection of earthing.
4) Base Coat
It is a three component self leveling system which is natural black in color. Base coat should be applied after drying of the Primer (usually after 6 – 8 hrs. from application of primer).
5) Topcoat
Top Coat is a three component self leveling system. There is a wide range of colors available for that and Technical department should be contacted for choosing the best suited color for a particular surrounding. Top coat is applied just after the drying of base coat. A gap of at least 12 hrs should be maintained for application of topcoat.
Roughening the surface of dried base coat by using emery paper is recommended for better bonding of the topcoat with the base coat. Before application of top coat the surface should be cleaned and ensure that the surface is free from dust particles.
Mixing and application methodology for top coat and base coat remains common as equal to a normal self-leveling system.
Anti-static epoxy flooring is preferred over other flooring methods when it is required to provide a floor having joint-free finishes along with high chemical resistance and decorative properties. Anti-static epoxy flooring is mostly used in electronic and telecommunication industries, automotive industries, pharmaceutical factories, aerospace industries, operation theatres, computer rooms etc.
In order to prepare a high performing coat, good substrate preparation is pivotal. The surface of the concrete over which the coat has to be laid must be hard, sound and free of dust and other barrier materials such as paint, lime, coatings, plaster, curing agents, laitance and other adhesive residues.
Anti-Static Epoxy Flooring Method
- Preliminary preparation for Anti-Static Epoxy Flooring
Methods of Applications of Anti-Static Epoxy Flooring
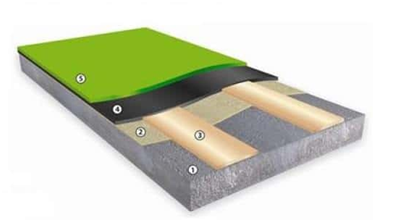
Layer-Arrangement of Anti-Static Epoxy Flooring
1) Surface preparation
All Substrates should be dry (max. 5% moisture content), clean, sound and free of laitance. Surface grinders and shot blasting are used to prepare the surface; the surface should be properly cleaned and should be free from dust prior to application of primer.
2) Priming
It is imperative that the Primer-contents are thoroughly premixed prior to mixing together. The contents are mixed slowly using a slow speed drill and paddle for at least 4 minutes. Primer is then applied on the dry concrete surface @ 0.2 to 0.25Kg/per square meter by Brush/Roller.
3) Laying of copper Tape
A copper strip of required width and thickness is laid. The butter paper is firstly removed and the adhesive side of the copper strip is kept exposed. Stick the self-adhesive copper strip on to the clean primed substrate at a distance of 1 to 4 meter to each other, lengthwise and breadth wise.
At the periphery, near to the walls, stick the self-adhesive copper strip at a distance of 6 inches from the walls. At any one end in the room, copper strip should be extended out for connection of earthing.
4) Base Coat
It is a three component self leveling system which is natural black in color. Base coat should be applied after drying of the Primer (usually after 6 – 8 hrs. from application of primer).
5) Topcoat
Top Coat is a three component self leveling system. There is a wide range of colors available for that and Technical department should be contacted for choosing the best suited color for a particular surrounding. Top coat is applied just after the drying of base coat. A gap of at least 12 hrs should be maintained for application of topcoat.
Roughening the surface of dried base coat by using emery paper is recommended for better bonding of the topcoat with the base coat. Before application of top coat the surface should be cleaned and ensure that the surface is free from dust particles.
Mixing and application methodology for top coat and base coat remains common as equal to a normal self-leveling system.