How Granite slabs are made – Inside of Granite Factory
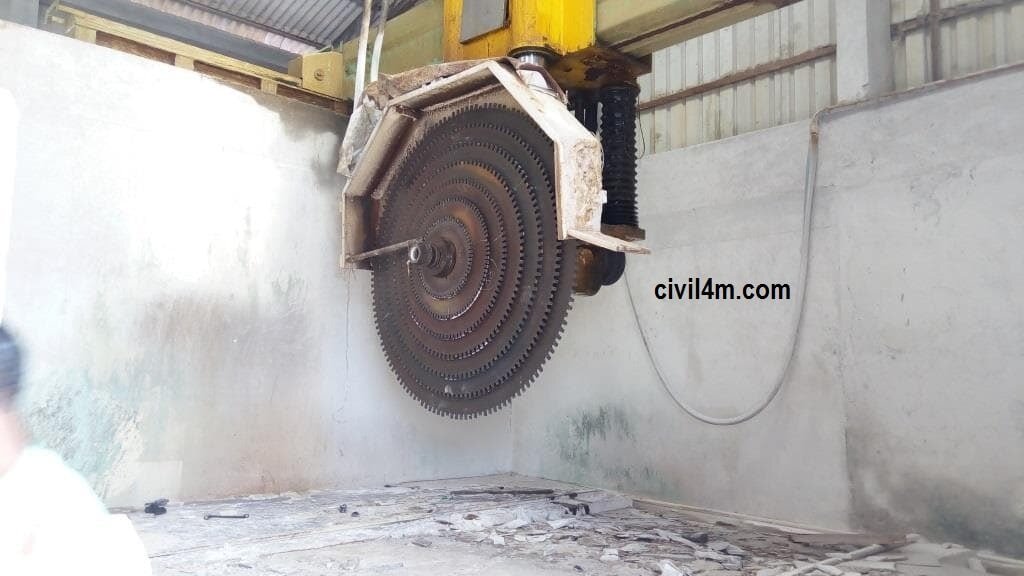
Granite is a hard stone and used at most of the places in construction of homes, commercial spaces, public and in all kinds of building.
It gives a better aesthetic look and Architect prefer to use it at maximum places.
The granite stones are taken out in big size blocks which can be transported and cut to required size from rock or earth by blasting, cutting and other means of suitable methods.
The raw stone blocks then transported to factory for further processing.
When a truck load reaches at factory, Quality inspector does its inspection, for quality, Color properties and presence of cracks in it. After this a financial calculation are done on the data and truck load is accepted or the bargaining happens base on the properties of stone.
Once the lot is accepted, it is unloaded with the help of gantry cranes.
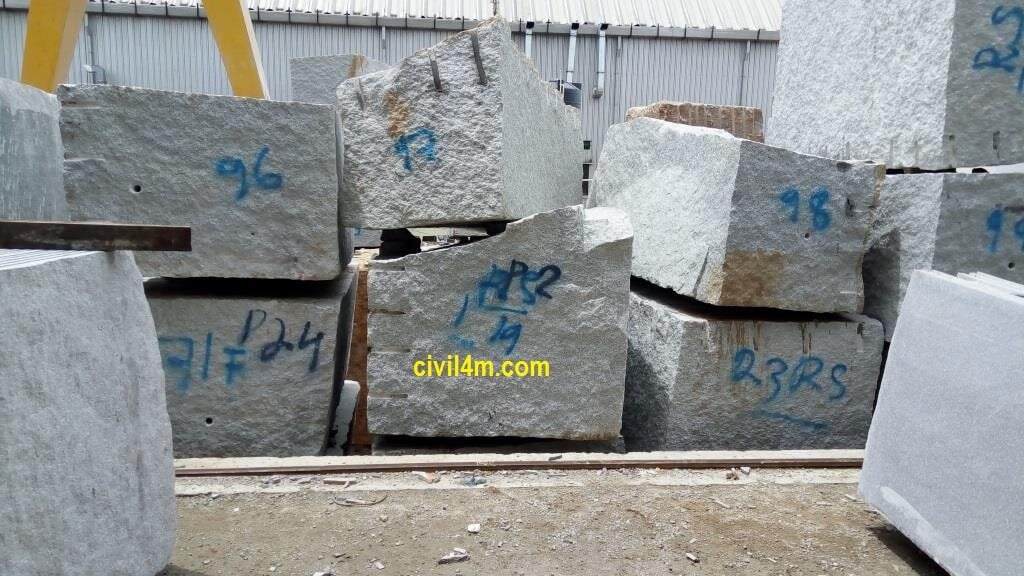
As the stones is natural material, there will be variation in properties of stones and mostly those people are interested in color and texture properties of it, according to properties stones are stacked for cutting. Same lot of stone can have different types of granite slab which can be sold at different prices.
The stones are then shifted one by one in cutting area, where stones are finally shaped into a slabs with thickness between 16 to 25 mm.
In most of the factories cutting of stone done with assembly of 4 blades, which cut stone blocks into 4 slices of specified thickness at different levels to avoid breakages and damages to it. During cutting water jet is also used at cutting location to prevent damages to stone and blades.
The cutting of stone can be done either in full body or by keeping some portion of stone block left uncut.
Cutting in full body gives you more quantity of slabs but may lead to damaging blades which increase the cost of maintenance.
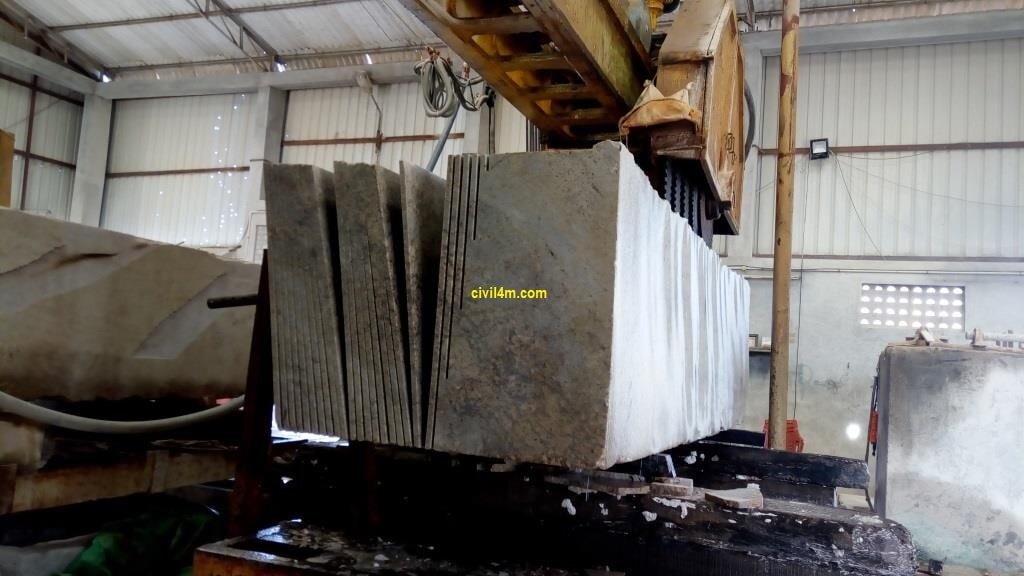
If you keep some space from bottom, and left some stone, this keeps slices of slab in position and reduce the risk of blades getting damaged.
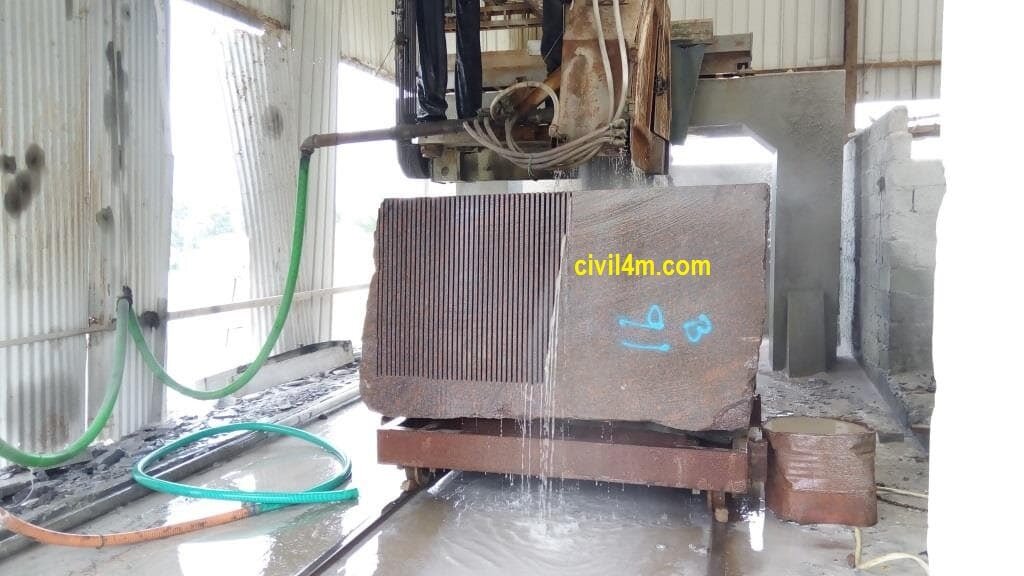
After completion of cutting stone block, it shifted to other location to break slabs from base body, in case block is not fully cut till bottom.
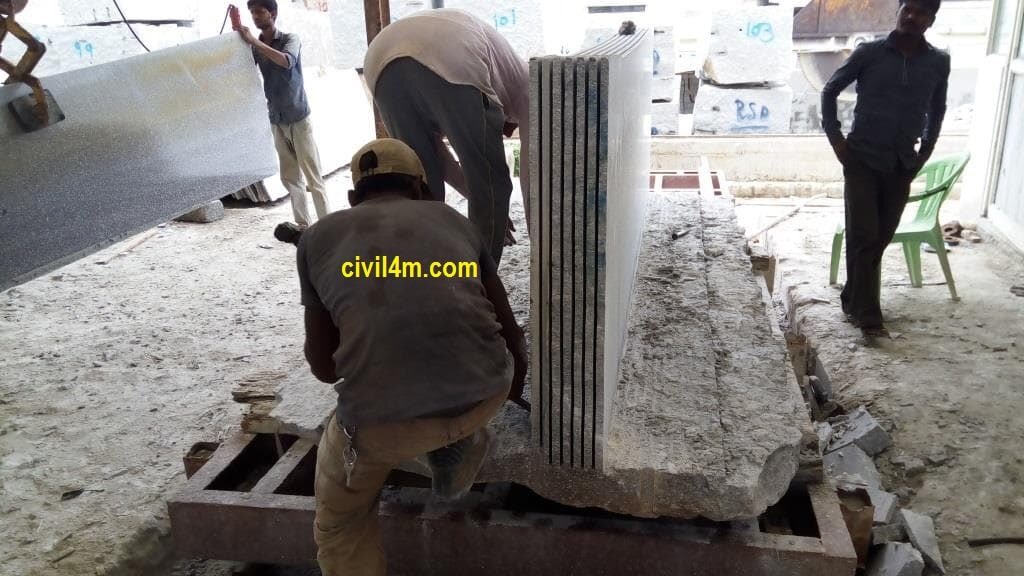
After removing each slab from body, then it is shifted to stack yard near polishing machine via gantry cranes.
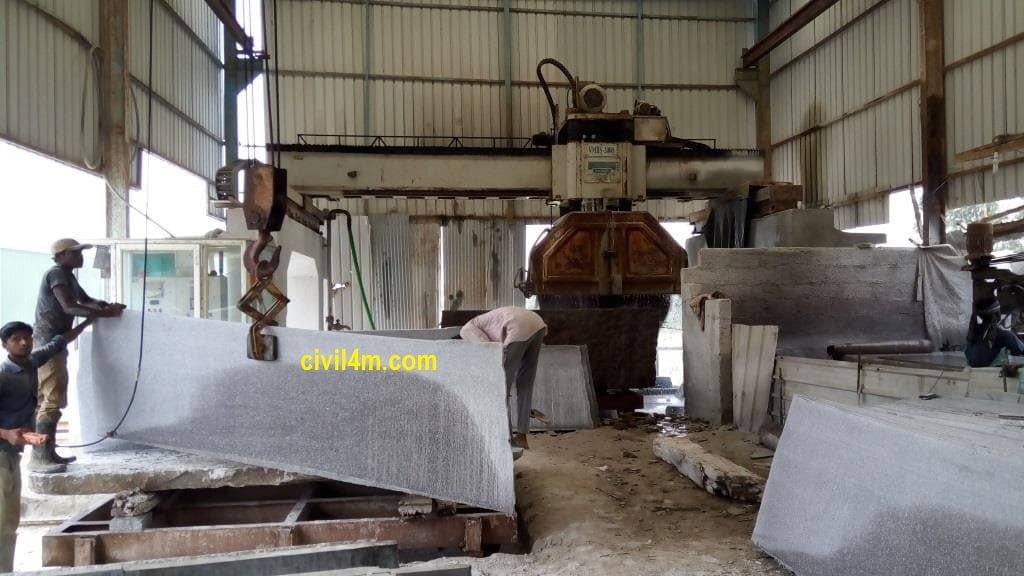
The stone slabs are then polished with polishing machines and different kinds of polishing blades.
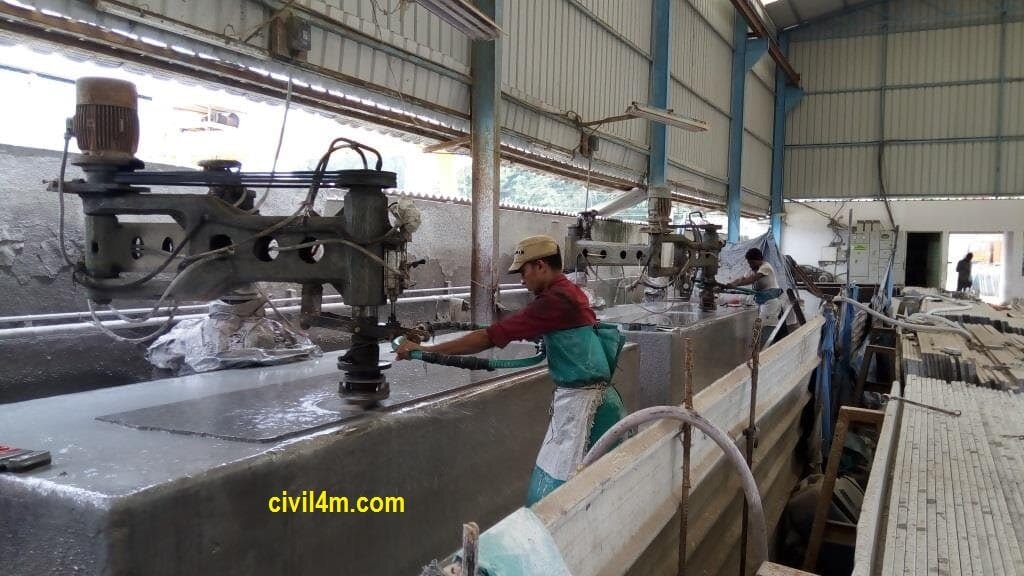
Water jet along with movement of polishing blades used to avoid, dusting and damages.

Below is the photo of different kinds of polishing stones, was seen at the Factory.
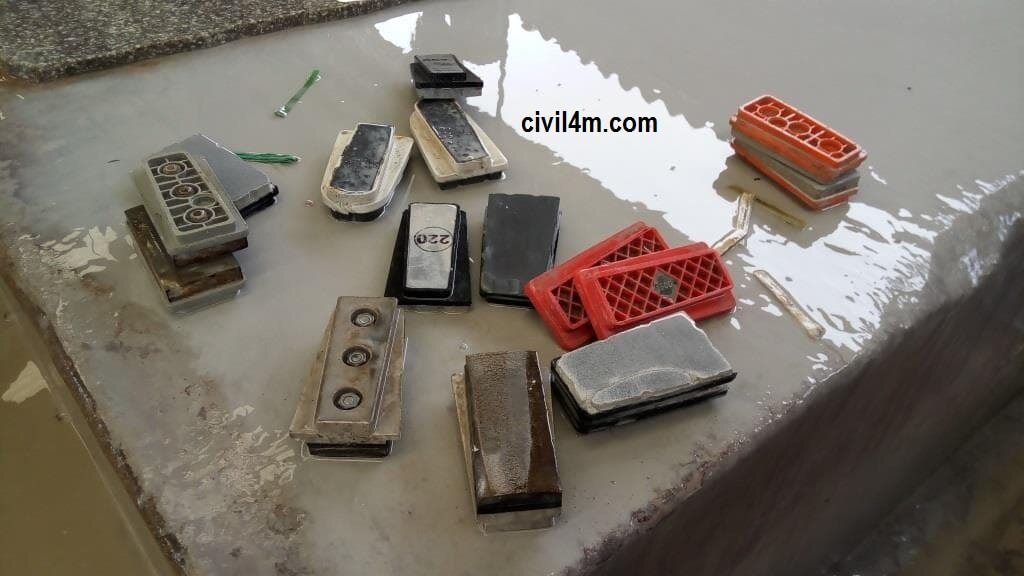
Polishing on granite stone slab is also done with fully automatic machine, where no human interaction happens other than placing and lifting slab from polishing machine area.
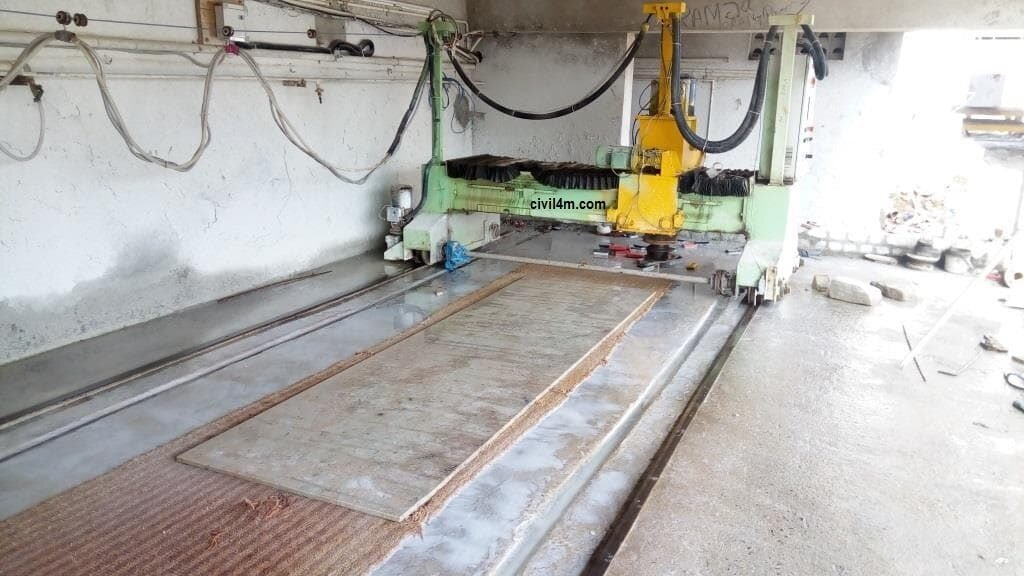
The remain body of stone block is not a waste, not a single piece of stone get wasted in any factory, those remains and waste pieces are crushed and used in manufacturing of artificial granite's, marbles, ceramic tiles etc.
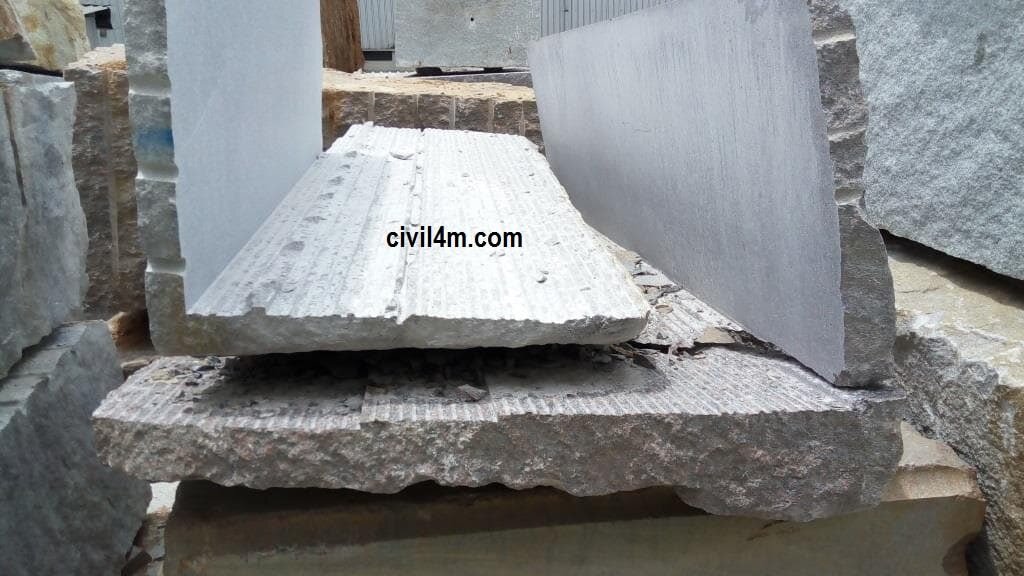
During cutting if there is slight movement in block, the polishing blade marks get embossed on slab due to scratching of surface. This is a unavoidable defect which can’t be seen from a distance, but if you take closer look of slab, you will find some scratches on granite slab.
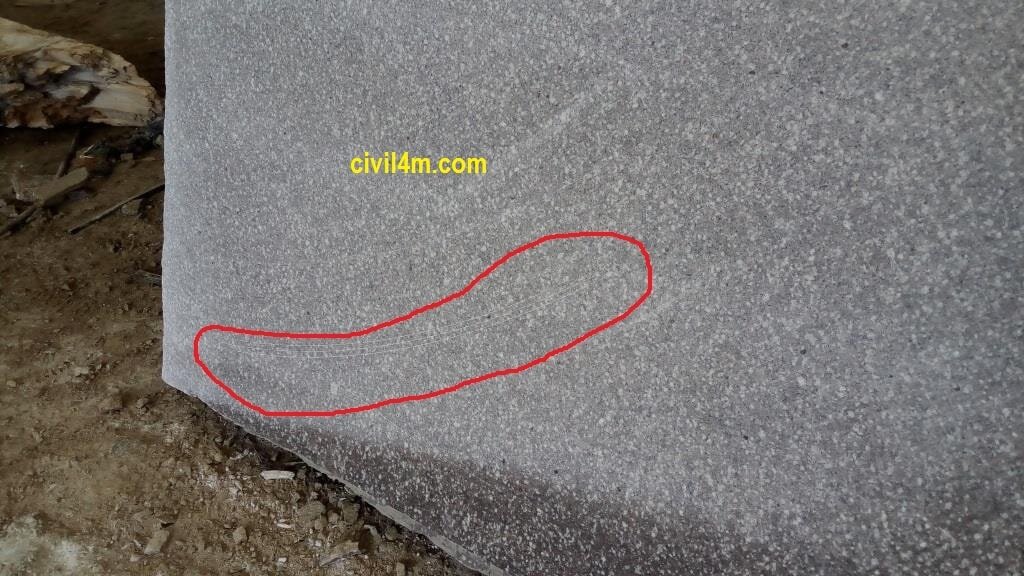
After polishing of granite slab, shiner is applied on the polished surface of granite to make its texture and color brighter. Those effect can go long term if slabs are used under sheds but may become dull if slabs are under direct sunlight. There also other parameters which can make granite slab surface finish dull over time.
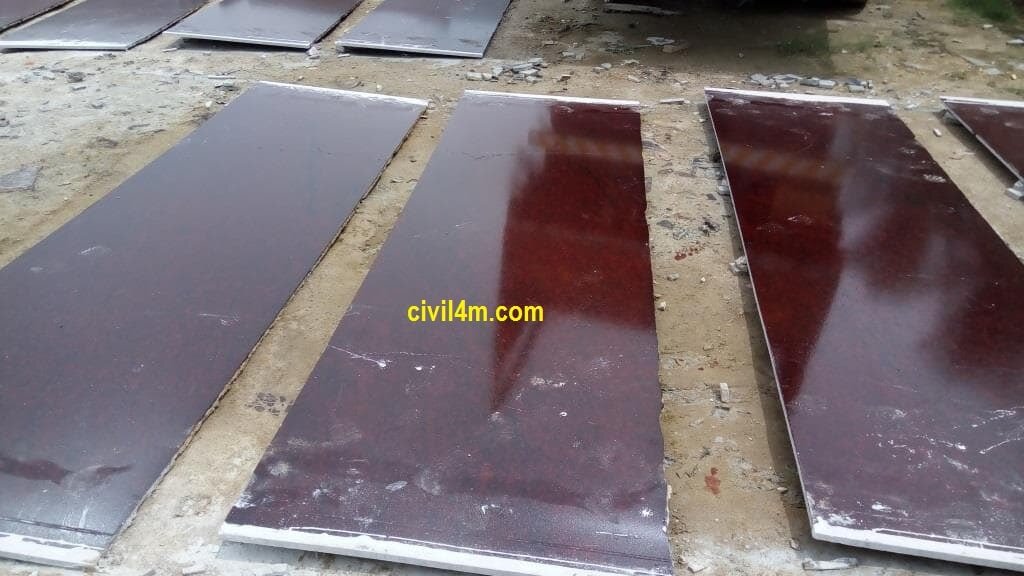
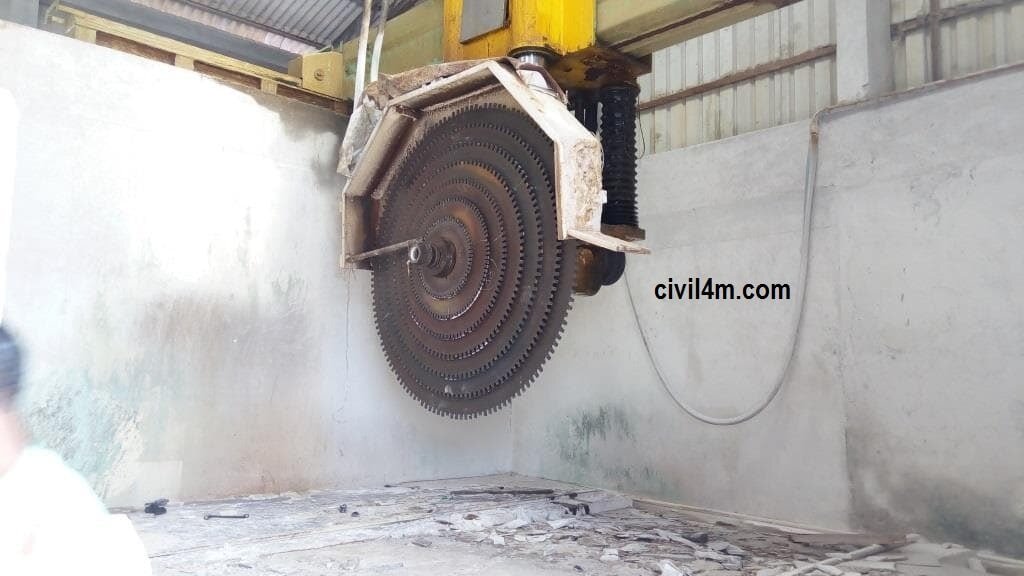
Granite is a hard stone and used at most of the places in construction of homes, commercial spaces, public and in all kinds of building.
It gives a better aesthetic look and Architect prefer to use it at maximum places.
The granite stones are taken out in big size blocks which can be transported and cut to required size from rock or earth by blasting, cutting and other means of suitable methods.
The raw stone blocks then transported to factory for further processing.
When a truck load reaches at factory, Quality inspector does its inspection, for quality, Color properties and presence of cracks in it. After this a financial calculation are done on the data and truck load is accepted or the bargaining happens base on the properties of stone.
Once the lot is accepted, it is unloaded with the help of gantry cranes.
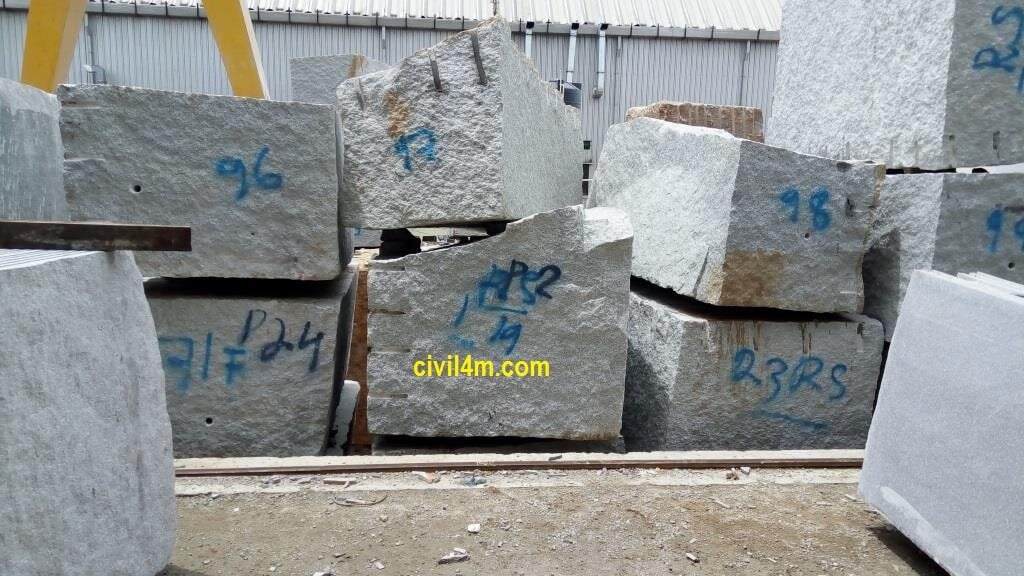
As the stones is natural material, there will be variation in properties of stones and mostly those people are interested in color and texture properties of it, according to properties stones are stacked for cutting. Same lot of stone can have different types of granite slab which can be sold at different prices.
The stones are then shifted one by one in cutting area, where stones are finally shaped into a slabs with thickness between 16 to 25 mm.
In most of the factories cutting of stone done with assembly of 4 blades, which cut stone blocks into 4 slices of specified thickness at different levels to avoid breakages and damages to it. During cutting water jet is also used at cutting location to prevent damages to stone and blades.
The cutting of stone can be done either in full body or by keeping some portion of stone block left uncut.
Cutting in full body gives you more quantity of slabs but may lead to damaging blades which increase the cost of maintenance.
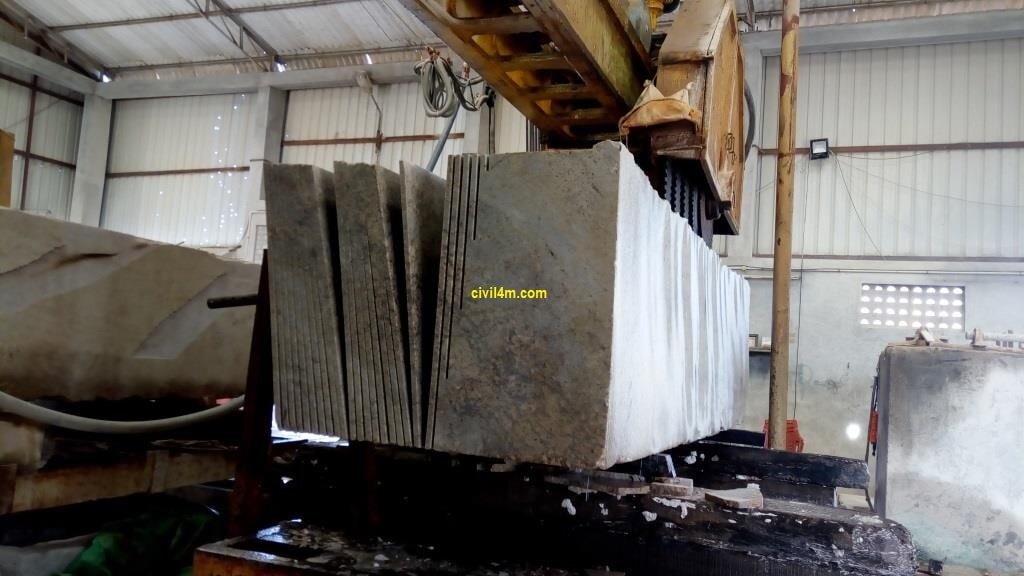
If you keep some space from bottom, and left some stone, this keeps slices of slab in position and reduce the risk of blades getting damaged.
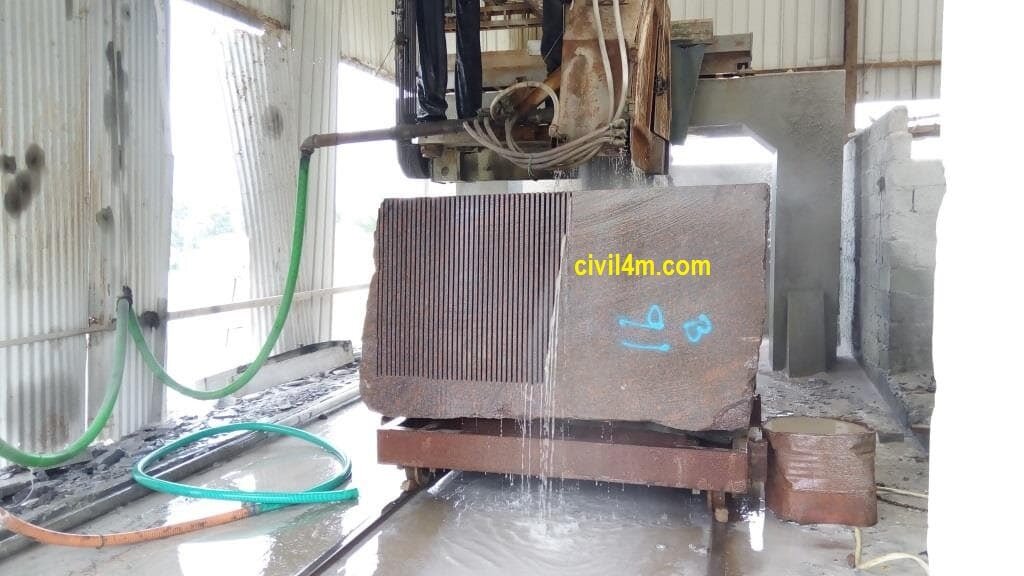
After completion of cutting stone block, it shifted to other location to break slabs from base body, in case block is not fully cut till bottom.
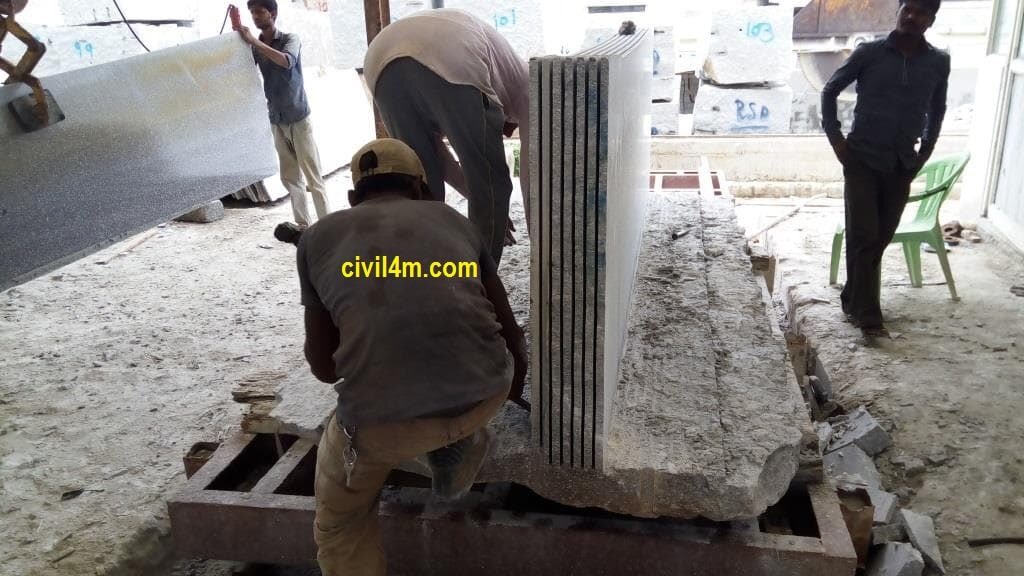
After removing each slab from body, then it is shifted to stack yard near polishing machine via gantry cranes.
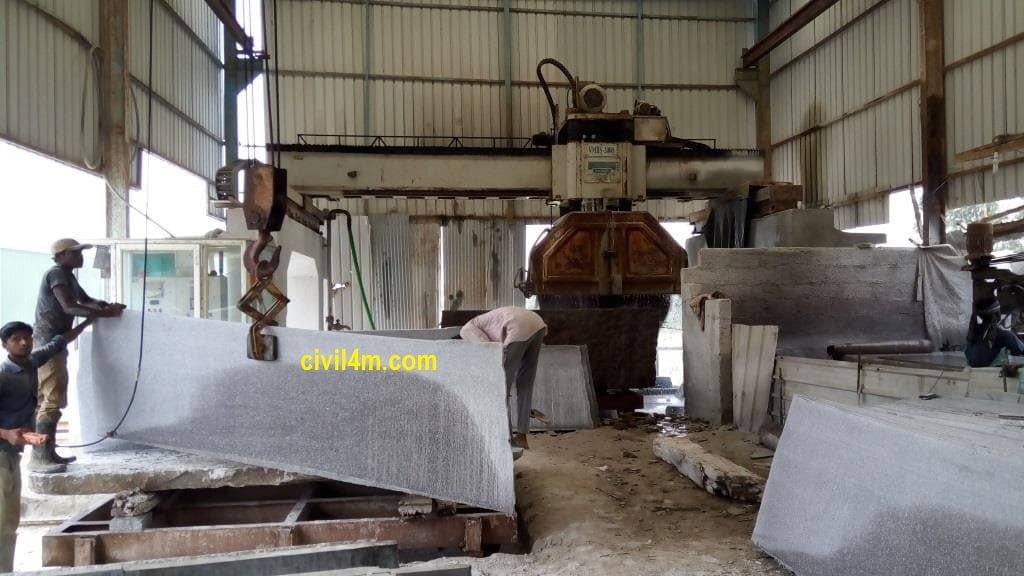
The stone slabs are then polished with polishing machines and different kinds of polishing blades.
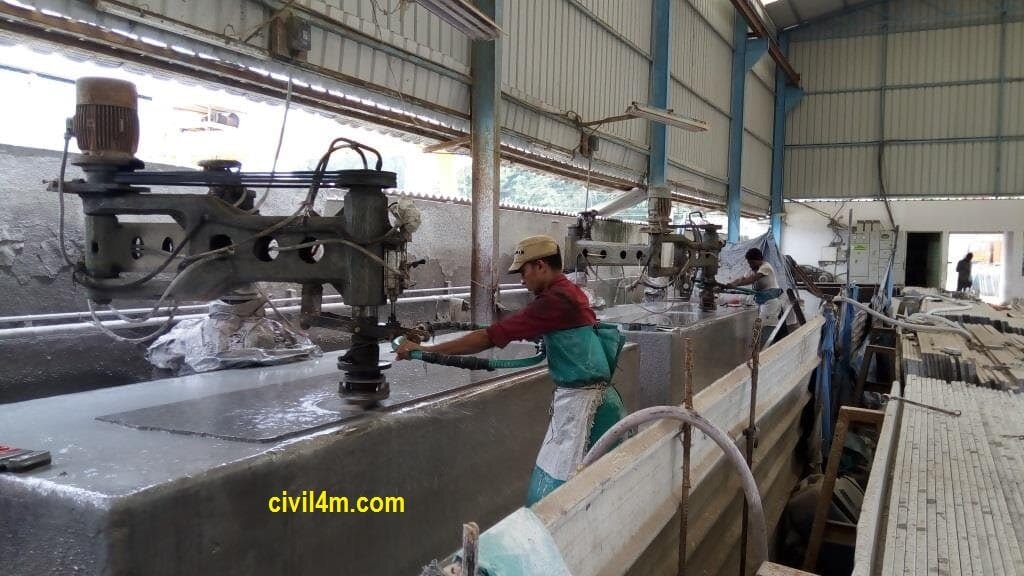
Water jet along with movement of polishing blades used to avoid, dusting and damages.

Below is the photo of different kinds of polishing stones, was seen at the Factory.
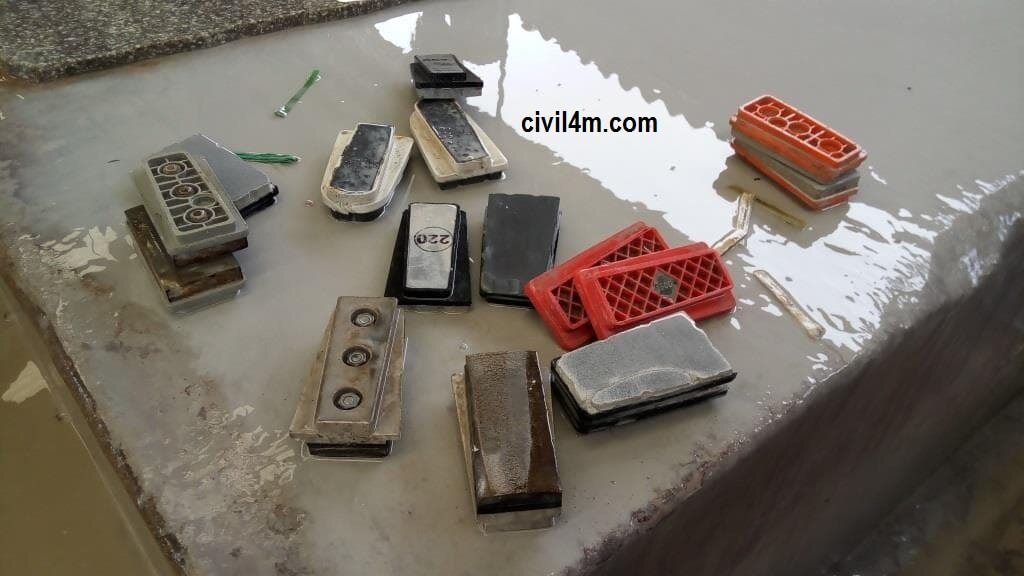
Polishing on granite stone slab is also done with fully automatic machine, where no human interaction happens other than placing and lifting slab from polishing machine area.
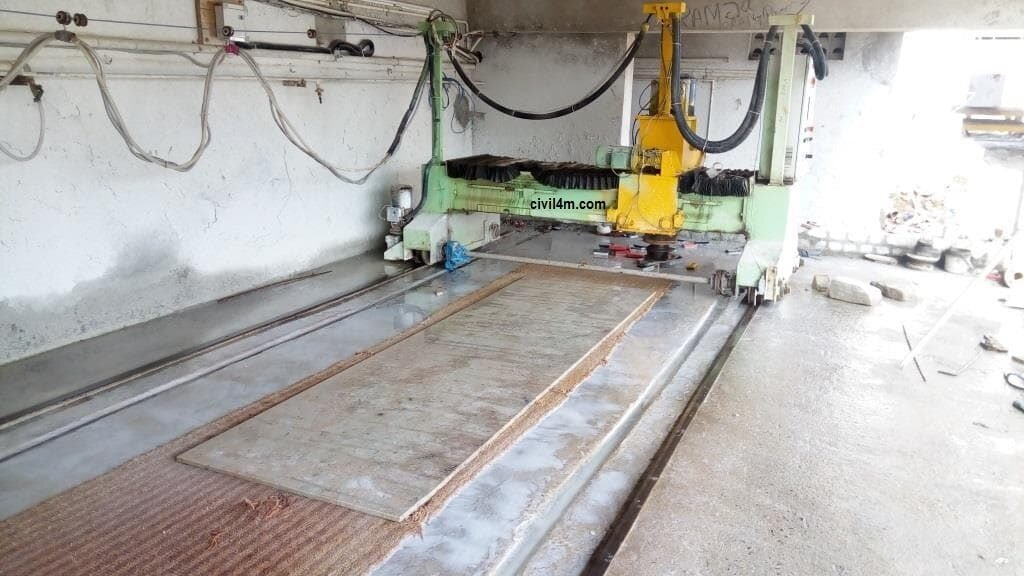
The remain body of stone block is not a waste, not a single piece of stone get wasted in any factory, those remains and waste pieces are crushed and used in manufacturing of artificial granite's, marbles, ceramic tiles etc.
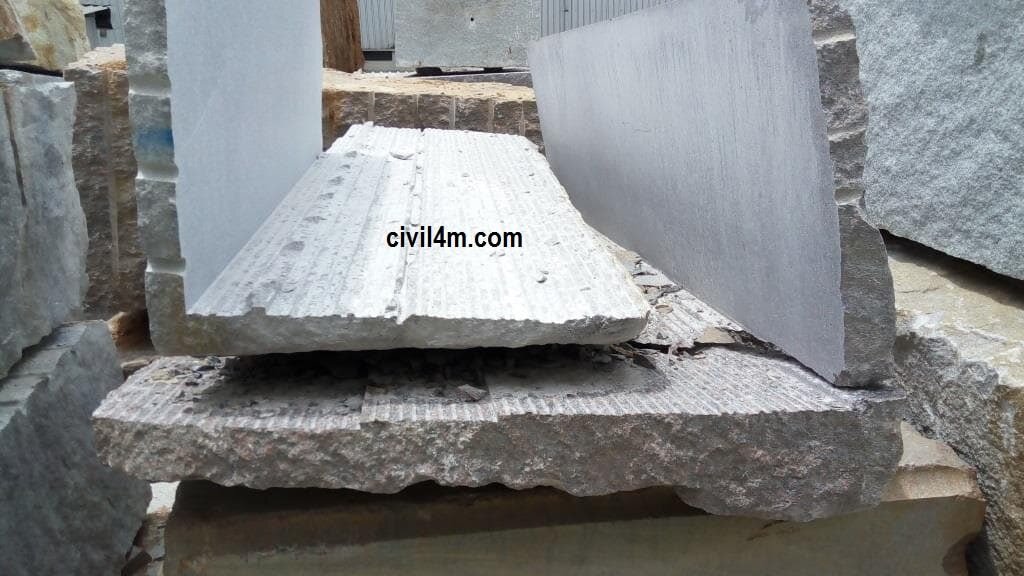
During cutting if there is slight movement in block, the polishing blade marks get embossed on slab due to scratching of surface. This is a unavoidable defect which can’t be seen from a distance, but if you take closer look of slab, you will find some scratches on granite slab.
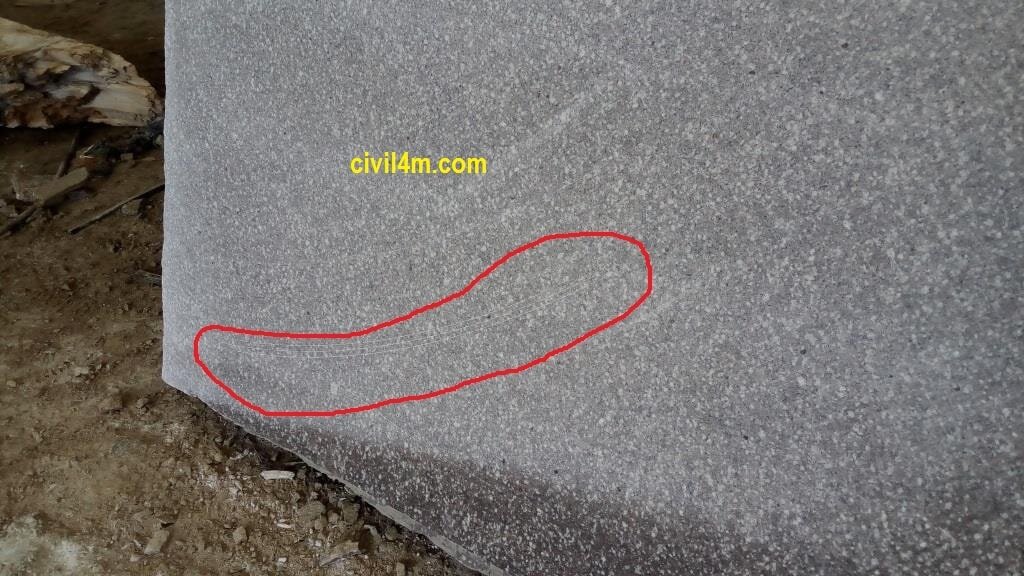
After polishing of granite slab, shiner is applied on the polished surface of granite to make its texture and color brighter. Those effect can go long term if slabs are used under sheds but may become dull if slabs are under direct sunlight. There also other parameters which can make granite slab surface finish dull over time.
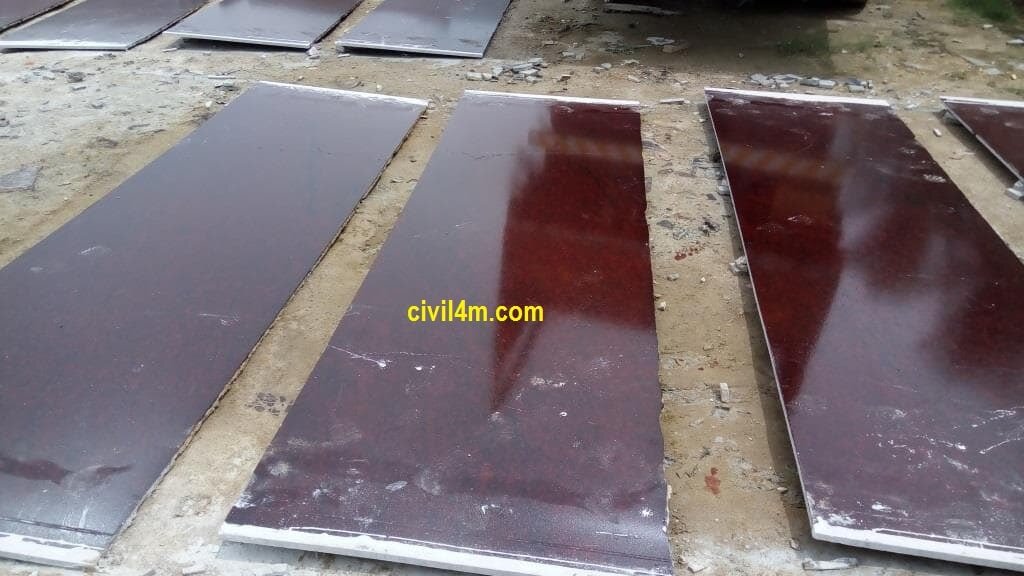