Method Statement for laying of BC DBM BM and SDBM for main carriageway and service roads
Method Statement For Laying of Binder Coarse (BC), Dense Bituminous Macadam (DBM), Bituminous Macadam (BM) for the main carriageway and Semi Dense Bituminous Macadam (SDBM) for the service roads
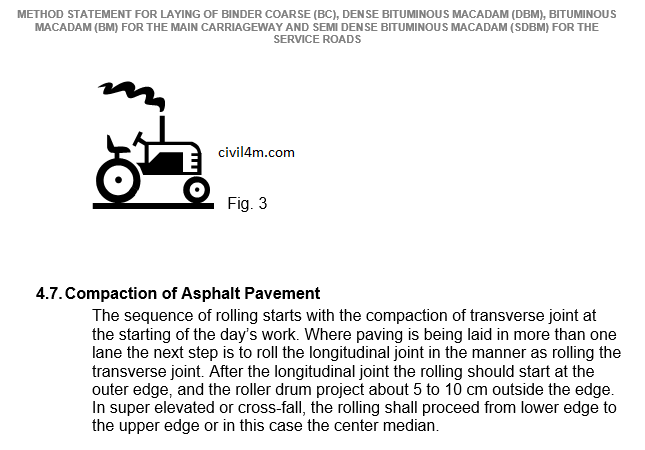
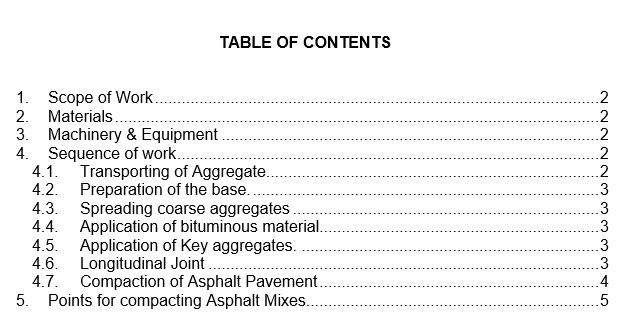
Scope of Work
The works generally consist of laying, spreading and compacting of Bituminous Bound Macadam (BBM) for the main carriageway on prepared road base (WMM) which primed previously with prime coat and in accordance to the requirement and specification given (Clause 507).
Materials
Approved source of crushed stone aggregates of 40MM, 20 MM, Key Aggregate of 12 MM and the binder material 60/70 grade Bitumen.
Machinery & Equipment
The equipment to be used for laying and spreading of BBM shall be Tippers, Motar Grader, vibration tandem roller, pneumatic tyre roller, Bitumen boozer and water truck as and when necessary.
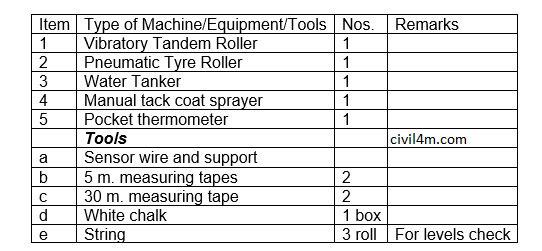
Sequence of work
The surface of the must clear of leaves, or inferior material etc. on WMM which are coated with tack coat , vehicle are not allow to travel on the surface other than trucks and boozer. Before carrying out actual paving operation ensure that the following to be checked on the site.
The transverse cold joint to be vertically cut, cleaned and tack coat to its face.
Transporting of Aggregate.
Number of truck and cycle time, adequacy, start time, Truck cleanliness
Preparation of the base.
The base on which the Bituminous bound macadam course is to be laid shall be prepared ,shaped, and compacted to specified lines, grades. Prime coat shall be over the base as per MORTH Cl.502-4.3
Spreading coarse aggregates
The coarse aggregate shall be dry and clean and free from dust and shall be spread uniformly and evenly at rate specified in QAP such as first spreading of 40 MM aggregate as rate 6kg to 9 kg per 100 Sqm then two pass of smooth steel wheel roller over the surface of 40 MM aggregates Next step 20 MM aggregate near about 15 % spreading over the surface for removing voids of 40 MM aggregate surface. After spreading of coarse aggregate rolling shall be carried out with an 8 -10 smooth steel wheel roller without cursing of aggregates until the compacted coarse aggregate has firm surface and texture that will allow free and uniform penetration of the bituminous material.
Then surface of layer shall be carefully checked with camber plate or Level Machine to ensure correct line & level and cross fall.
Application of bituminous material
After the coarse aggregate has been rolled and checked, the bituminous binder shall be applied ,at rate given in QAP 200 kg per 100 Sqm and temperature as directed by Engineer in Charge.
At the time of applying the binder ,the aggregates shall be surface dry for full depth of layer.
Application of Key aggregates.
Immediately after the first application of bitumen ,the key aggregates(12 MM) ,which shall be clean ,dry ,and free from dust shall be spread uniformly over surface by manual method at rate specified in QAP 1.2 Cum to 1.8 Cum per 100 Sqm.
Longitudinal Joint
On longitudinal joint, there are two option to deal with it.
One is that on the earlier laid mat the longitudinal joint shall be heat to at least the rolling temperature by way of a gas burner torch as the over lapping of paving in progress.
Two, the joint is to be cut to its full depth to produce a straight edge. When these two option is carry out while laying the asphlatic material, the edge of the previously laid mat to be sprayed with light tack coat to enable the second mat to be bonded to the first. The screed should be positioned to give an overlap of 25 to 50mm for the second mat as shown in fig. 2. The overlapping material should be “feathered out” over the joint before rolling so that a perfect bonding and durable joint is obtained.
Compaction of Asphalt Pavement
The sequence of rolling starts with the compaction of transverse joint at the starting of the day’s work. Where paving is being laid in more than one lane the next step is to roll the longitudinal joint in the manner as rolling the transverse joint. After the longitudinal joint the rolling should start at the outer edge, and the roller drum project about 5 to 10 cm outside the edge. In super elevated or cross-fall, the rolling shall proceed from lower edge to the upper edge or in this case the center median.
Initial rolling temperature of the mix shall be in the range of 115 to 135 degree Celesius. A trial lay shall be conducted for the paving and determination of the rolling pattern of the mat.
The rolling pattern as mentioned below 2,2,8,2 shall means that the initial rolling will be 2 passes follow by 2 passes of vibrating, 6 passes by the pneumatic tyre roller and finally by the tandem roller to erase the tyre marks.
Initial rolling 2 static passes shall be rolled by means of vibratory compactor (twin smooth drum tandem roller) follow by applying 2 passes of vibration compaction. When vibratory roller is used for compaction of bituminous material, vibration should be cut off before changing direction of travel, to avoid marks on the surface and prevent shear or slip on the mat. The maximum speed for smooth wheeld roller is recommended as 5 km/hr and the speed of pneumatic tyre roller shall be 10km/hr. the roller drums/tyres shall be kept moist to prevent pick up of the hot asphalt mix.
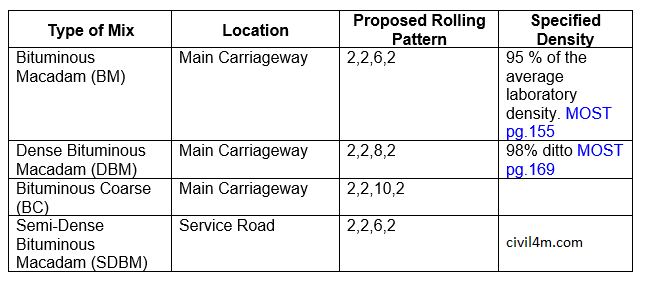
Points for compacting Asphalt Mixes
The following points should be noted during compaction of the Asphalt mixes;
After the longitudinal joint has been compacted rolling should start longitudinally at the edge and proceed towards the center of the carpet.
On super elevated curves rolling should start on the lower side and progress to the high side.
Each pass of the roller should overlap the preceding one by at least half the width of the rear wheel.
The roller should proceed on to fresh material with the fixed wheel leading in order to minimize movement and pushing of the mix.
The number of passed required will depend largely on thickness of the carpet and the weight if the roller, and temperature of the mix at the time of laying.
Areas of pavement inaccessible to roller shoild be compacted by a tampers.
You can download method statement from below attachment.
Method Statement For Laying of Binder Coarse (BC), Dense Bituminous Macadam (DBM), Bituminous Macadam (BM) for the main carriageway and Semi Dense Bituminous Macadam (SDBM) for the service roads
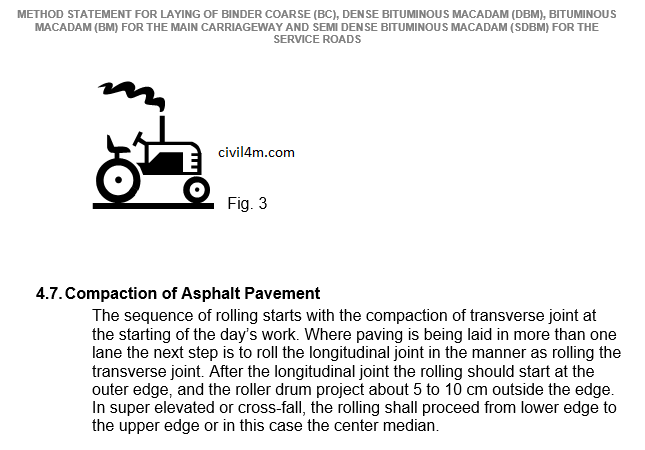
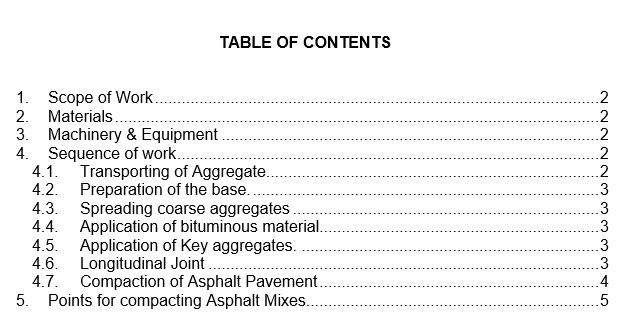
Scope of Work
The works generally consist of laying, spreading and compacting of Bituminous Bound Macadam (BBM) for the main carriageway on prepared road base (WMM) which primed previously with prime coat and in accordance to the requirement and specification given (Clause 507).
Materials
Approved source of crushed stone aggregates of 40MM, 20 MM, Key Aggregate of 12 MM and the binder material 60/70 grade Bitumen.
Machinery & Equipment
The equipment to be used for laying and spreading of BBM shall be Tippers, Motar Grader, vibration tandem roller, pneumatic tyre roller, Bitumen boozer and water truck as and when necessary.
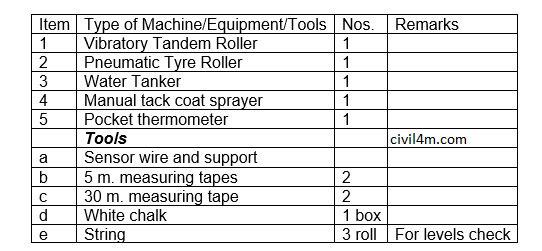
Sequence of work
The transverse cold joint to be vertically cut, cleaned and tack coat to its face.
Transporting of Aggregate.
Number of truck and cycle time, adequacy, start time, Truck cleanliness
Preparation of the base.
The base on which the Bituminous bound macadam course is to be laid shall be prepared ,shaped, and compacted to specified lines, grades. Prime coat shall be over the base as per MORTH Cl.502-4.3
Spreading coarse aggregates
The coarse aggregate shall be dry and clean and free from dust and shall be spread uniformly and evenly at rate specified in QAP such as first spreading of 40 MM aggregate as rate 6kg to 9 kg per 100 Sqm then two pass of smooth steel wheel roller over the surface of 40 MM aggregates Next step 20 MM aggregate near about 15 % spreading over the surface for removing voids of 40 MM aggregate surface. After spreading of coarse aggregate rolling shall be carried out with an 8 -10 smooth steel wheel roller without cursing of aggregates until the compacted coarse aggregate has firm surface and texture that will allow free and uniform penetration of the bituminous material.
Then surface of layer shall be carefully checked with camber plate or Level Machine to ensure correct line & level and cross fall.
Application of bituminous material
After the coarse aggregate has been rolled and checked, the bituminous binder shall be applied ,at rate given in QAP 200 kg per 100 Sqm and temperature as directed by Engineer in Charge.
At the time of applying the binder ,the aggregates shall be surface dry for full depth of layer.
Application of Key aggregates.
Immediately after the first application of bitumen ,the key aggregates(12 MM) ,which shall be clean ,dry ,and free from dust shall be spread uniformly over surface by manual method at rate specified in QAP 1.2 Cum to 1.8 Cum per 100 Sqm.
Longitudinal Joint
On longitudinal joint, there are two option to deal with it.
One is that on the earlier laid mat the longitudinal joint shall be heat to at least the rolling temperature by way of a gas burner torch as the over lapping of paving in progress.
Two, the joint is to be cut to its full depth to produce a straight edge. When these two option is carry out while laying the asphlatic material, the edge of the previously laid mat to be sprayed with light tack coat to enable the second mat to be bonded to the first. The screed should be positioned to give an overlap of 25 to 50mm for the second mat as shown in fig. 2. The overlapping material should be “feathered out” over the joint before rolling so that a perfect bonding and durable joint is obtained.
Compaction of Asphalt Pavement
The sequence of rolling starts with the compaction of transverse joint at the starting of the day’s work. Where paving is being laid in more than one lane the next step is to roll the longitudinal joint in the manner as rolling the transverse joint. After the longitudinal joint the rolling should start at the outer edge, and the roller drum project about 5 to 10 cm outside the edge. In super elevated or cross-fall, the rolling shall proceed from lower edge to the upper edge or in this case the center median.
Initial rolling temperature of the mix shall be in the range of 115 to 135 degree Celesius. A trial lay shall be conducted for the paving and determination of the rolling pattern of the mat.
The rolling pattern as mentioned below 2,2,8,2 shall means that the initial rolling will be 2 passes follow by 2 passes of vibrating, 6 passes by the pneumatic tyre roller and finally by the tandem roller to erase the tyre marks.
Initial rolling 2 static passes shall be rolled by means of vibratory compactor (twin smooth drum tandem roller) follow by applying 2 passes of vibration compaction. When vibratory roller is used for compaction of bituminous material, vibration should be cut off before changing direction of travel, to avoid marks on the surface and prevent shear or slip on the mat. The maximum speed for smooth wheeld roller is recommended as 5 km/hr and the speed of pneumatic tyre roller shall be 10km/hr. the roller drums/tyres shall be kept moist to prevent pick up of the hot asphalt mix.
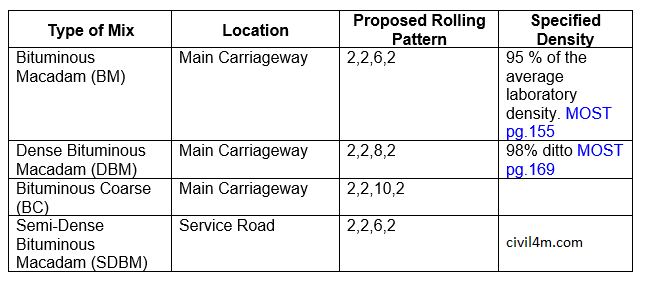
Points for compacting Asphalt Mixes
The following points should be noted during compaction of the Asphalt mixes;
After the longitudinal joint has been compacted rolling should start longitudinally at the edge and proceed towards the center of the carpet.
On super elevated curves rolling should start on the lower side and progress to the high side.
Each pass of the roller should overlap the preceding one by at least half the width of the rear wheel.
The roller should proceed on to fresh material with the fixed wheel leading in order to minimize movement and pushing of the mix.
The number of passed required will depend largely on thickness of the carpet and the weight if the roller, and temperature of the mix at the time of laying.
Areas of pavement inaccessible to roller shoild be compacted by a tampers.
You can download method statement from below attachment.