Concrete is a composite material composed of aggregate bonded together with a fluid cement which hardens over time. Most use of the term "concrete" refers to Portland cement concrete or to concretes made with other hydraulic cements. However, technically road pavement is also a type of concrete, "asphaltic concrete", where the cement material is bitumen.
Properties of Cement Concrete
The cement concrete possesses the following important properties:
Mixing
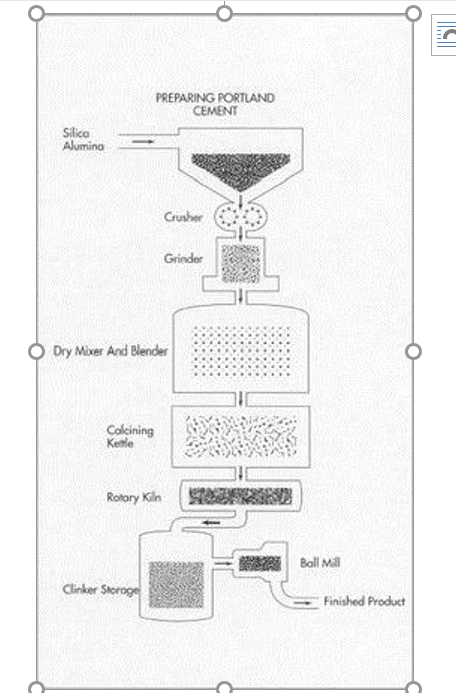
Placing and compacting
Once at the site, the concrete must be placed and compacted. These two operations are performed almost simultaneously. Placing must be done so that segregation of the various ingredients is avoided and full compaction—with all air bubbles eliminated—can be achieved. Whether chutes or buggies are used, position is important in achieving these goals. The rates of placing and of compaction should be equal; the latter is usually accomplished using internal or external vibrators. An internal vibrator uses a poker housing a motor-driven shaft. When the poker is inserted into the concrete, controlled vibration occurs to compact the concrete. External vibrators are used for precast or thin in situ sections having a shape or thickness unsuitable for internal vibrators. These type of vibrators are rigidly clamped to the formwork, which rests on an elastic support. Both the form and the concrete are vibrated. Vibrating tables are also used, where a table produces vertical vibration by using two shafts rotating in opposite directions.
Curing
Once it is placed and compacted, the concrete must cured before it is finished to make sure that it doesn't dry too quickly. Concrete's strength is influenced by its moisture level during the hardening process: as the cement solidifies, the concrete shrinks. If site constraints prevent the concrete from contracting, tensile stresses will develop, weakening the concrete. To minimize this problem, concrete must be kept damp during the several days it requires to set and harden.
Properties of Cement Concrete
The cement concrete possesses the following important properties:
- It possesses a high compressive strength.
- It is a corrosion resistance material and atmospheric agent has no appreciable effect on it.
- It hardens with age the process of hardening continues for a long time after the concrete has attained sufficient strength. It is this property of cement concrete which gives it a distinct place among building materials.
- It is more economical than steel.
- It binds rapidly with steel and as it is weak in tension, the steel reinforcement is placed in cement concrete at suitable places to take up the tensile stresses. This is termed as the reinforced cement concrete or simply as R.C.C.
- Under the following two conditions, it has a tendency to shrink:
- There is initial shrinkage of cement concrete which is mainly due to the loss of water through forms, absorption by surfaces of forms etc.
- The shrinkage of cement concrete occurs as it hardens. This tendency of cement concrete can be minimized by proper curing of concrete.
- It has a tendency to be porous. This is due to the presence of voids which are formed during and after its placing. The two precautions necessary to avoid this tendency are as follows:
- There should be proper grading and consolidating of the aggregates.
- The minimum water-cement ratio should be adopted.
- It forms a hard surface, capable of resisting abrasion.
- It should be remembered that apart from other materials, the concrete comes to the site in the form of raw materials only. Its final strength and quality depend entirely on local conditions and persons handling it. However the materials which concrete is composed may be subjected to rigid specifications
Mixing
- The cement is then mixed with the other ingredients: aggregates (sand, gravel, or crushed stone), admixtures, fibers, and water. Aggregates are pre-blended or added at the ready-mix concrete plant under normal operating conditions. The mixing operation uses rotation or stirring to coat the surface of the aggregate with cement paste and to blend the other ingredients uniformly. A variety of batch or continuous mixers are used.
- Fibers, if desired, can be added by a variety of methods including direct spraying, premixing, impregnating, or hand laying-up. Silica fume is often used as a dispersing or densifying agent.
- Once the concrete mixture is ready, it is transported to the work site. There are many methods of transporting concrete, including wheelbarrows, buckets, belt conveyors,
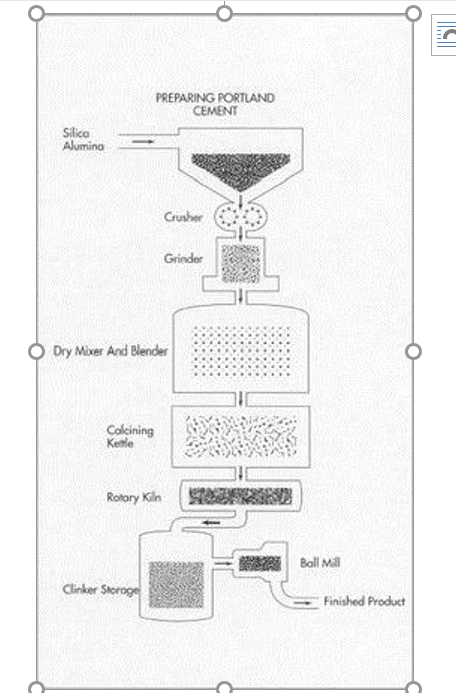
- The first step in making concrete is to prepare the cement. One type of cement, Portland cement, is considered superior to natural cement because it is stronger, more durable, and of a more consistent quality. To make it, the raw materials are crushed and ground into a fine powder and mixed together. Next, the material undergoes two heating steps—calcining and burning. In calcining, the materials are heated to a high temperature but do not fuse together. In burning, however, the materials partially fuse together, forming a substance known as "clinker." The clinker is then ground in a ball mill, a rotating steel drum filled with steel balls that pulverize the material.
- After the Portland cement is prepared, it is mixed with aggregates such as sand or gravel, admixtures, fibers, and water. Next, it is transferred to the work site and placed. During placing, segregation of the various ingredients must be avoided so that full compaction, elimination of air bubbles can be achieved.
special trucks, and pumping. Pumping transports large quantities of concrete over large distances through pipelines using a system consisting of a hopper, a pump, and the pipes. Pumps come in several types—the horizontal piston pump with semi-rotary valves and small portable pumps called squeeze pumps. A vacuum provides a continuous flow of concrete, with two rotating rollers squeezing a flexible pipe to move the concrete into the delivery pipe.
Placing and compacting
Once at the site, the concrete must be placed and compacted. These two operations are performed almost simultaneously. Placing must be done so that segregation of the various ingredients is avoided and full compaction—with all air bubbles eliminated—can be achieved. Whether chutes or buggies are used, position is important in achieving these goals. The rates of placing and of compaction should be equal; the latter is usually accomplished using internal or external vibrators. An internal vibrator uses a poker housing a motor-driven shaft. When the poker is inserted into the concrete, controlled vibration occurs to compact the concrete. External vibrators are used for precast or thin in situ sections having a shape or thickness unsuitable for internal vibrators. These type of vibrators are rigidly clamped to the formwork, which rests on an elastic support. Both the form and the concrete are vibrated. Vibrating tables are also used, where a table produces vertical vibration by using two shafts rotating in opposite directions.
Curing
Once it is placed and compacted, the concrete must cured before it is finished to make sure that it doesn't dry too quickly. Concrete's strength is influenced by its moisture level during the hardening process: as the cement solidifies, the concrete shrinks. If site constraints prevent the concrete from contracting, tensile stresses will develop, weakening the concrete. To minimize this problem, concrete must be kept damp during the several days it requires to set and harden.