Work Procedure for Backfilling
attachment snapshot
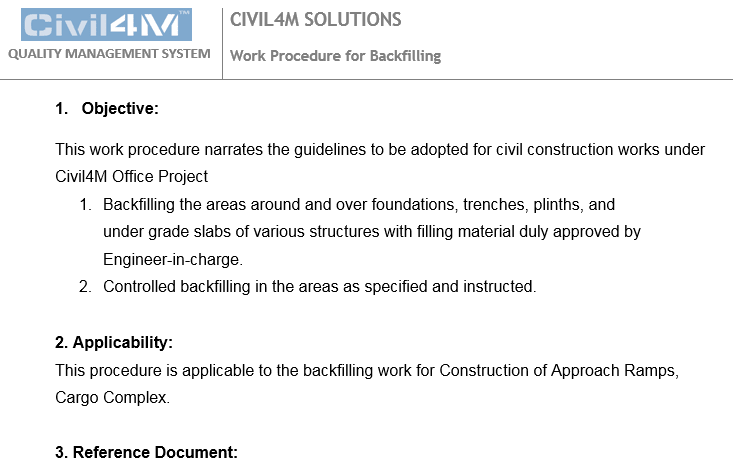
1. Objective:
This work procedure narrates the guidelines to be adopted for civil construction works under Civil4M Office Project
- Backfilling the areas around and over foundations, trenches, plinths, and under grade slabs of various structures with filling material duly approved by Engineer-in-charge.
- Controlled backfilling in the areas as specified and instructed.
2. Applicability:
This procedure is applicable to the backfilling work for Construction of Approach Ramps, Cargo Complex.
3. Reference Document:
Tender Specifications.
IS 2720 (Part V11).
Drawings
4. Responsibility:
The Project Manager shall be responsible for the overall implementation of this procedure.
5. Equipment:
a. Compaction Equipment’s
Smooth wheeled vibratory roller of 10T weight.
Smooth wheeled vibratory roller of 2T weight (to be used in the case it is found difficult to deploy 10T roller)
Pneumatic roller / Plate Compactor (to be used in space congestion where compaction by vibratory roller is not feasible.
b. Test Equipment’s
Proctor Density Test Apparatus.
Core-cutter in-situ density test apparatus
6. Backfilling procedure:
Fill Material
When directed by the engineer coarse river/crushed sand shall also be used as backfill material. Soils such as black cotton soil, clay and mixtures having excessive swelling characteristics shall not be used as filling material.
For Controlled Backfilling
Selected material from any one of the followings shall be used for controlled backfilling. Before selecting any material for backfilling, modified proctor density tests shall be conducted on the material to determine its maximum dry density. The maximum dry density shall not be less than 1.44 gm/sq.cm.
Murrum
Murrum of approved quality obtained from borrow pits duly approved by Engineer-in-charge shall be used. Murrum shall be composed of large, coarse, siliceous grains & gritty to the touch and free from dirt and foreign material.
Murrum shall not contain lumps larger than 40 mm in size. Natural clay content shall not exceed 10 % and fine sand content (i.e. passing 75micron sieve) shall not exceed 8 %.
Note:
Borrow-pits shall be got approved from Engineer-in-charge. Once approved by Engineer-in-charge, filling material shall be brought from that borrow pits.
Backfilling by Excavated Material
After completion of the foundation works, the spaces left in the pits and trenches shall be cleared of debris, brickbats, mortar droppings etc. prior to the start of backfilling.
Filling material shall be spread in layers of thickness approx. 200 mm and compacted by 4 passes of 10 T vibratory roller. Water shall be sprinkled intermittently.
Each layer shall be compacted before laying the succeeding layer. Surface voids in each layer shall be filled by crusher dust.
In case of plinth filling the backfilling as per the above procedure shall be continued up to the bottom of the plinth beam. The top surface at this stage shall be flooded with water for a minimum of 24 hrs. and defects in backfill shall be rectified and shall be trimmed to the desired level of slope, if any. Further filling within the plinth beams shall be controlled backfilling and soling as indicated in the relevant drawings.
Backfilling by Sand
Sand shall be used as filling material between foundations where space for proper compaction by mechanical means is not available and when directed by the Engineer-in-charge. Sand shall be spread in 200 mm thick layers, flooded with water and rammed. Top layer of sand shall be compacted by mechanical means.
Procedure for Controlled Backfilling
When instructed by the Engineer-in –Charge, controlled backfilling shall be done. Material shall be spread in un compacted layers of thickness approx. 200 mm and rolled by adequate number of passes of a 10T vibratory roller so as to achieve 90% of the maximum Proctor density of the fill material.
7. Safety plan:
Ensure that Jungle clearance is properly done and Remove nails, sharp edged items and other Hazardous materials / items [e.g.: snake dwelling mud holes] from the BORROWING SOURCE before commencing BORROWING activities.
Cover / barricade the unclosed utility manholes / pits if any.
Avoid using rebar cut pieces for signboards / barricading. If used - PVC rebar caps shall be fixed on top of it.
Signalman shall be kept near the FILLING area so as to alert the surrounding workers about movement of vehicles and deeply excavated pits.
Pits and diesel storage areas shall be barricaded.
Keep collection trays below excavation equipment’s like compressors etc., so as to avoid spreading of fuels etc.,
Use PPE’s [Gumboot, Hand glows, Helmet etc.].
Ensure back light and reverse horn for all the vehicles, which will be used for this filling work.
Fool proof system for reversal of vehicle to be ensured.
All the equipment’s including plate compactor shall have the guard protection for belt moving portion.
8. Inspection Records:
Field Quality Check of Backfilling
Each compacted layer shall be cleared by Engineer-in-charge for surface voids etc randomly. A record in the form of either registers or sketches for the clearance shall be maintained.
Field Quality Check of Controlled Backfilling
Each compacted layer under controlled backfilling shall be tested for degree of compaction. One test per 100 sq. m of compacted area shall be done for determining field dry density of the compacted layer. Alternate layers shall be tested as per Modified Proctor Density Test and Sand Replacement Method respectively. Records of field density test shall be maintained in the format approved by Engineer-in-charge.
FIELD DRY DENSITY TEST
MODIFIED PROCTOR DENSITY TEST
CHECK LIST
This SOP (Standard Operating Procedure) / Work Procedure is attached herewith.
attachment snapshot
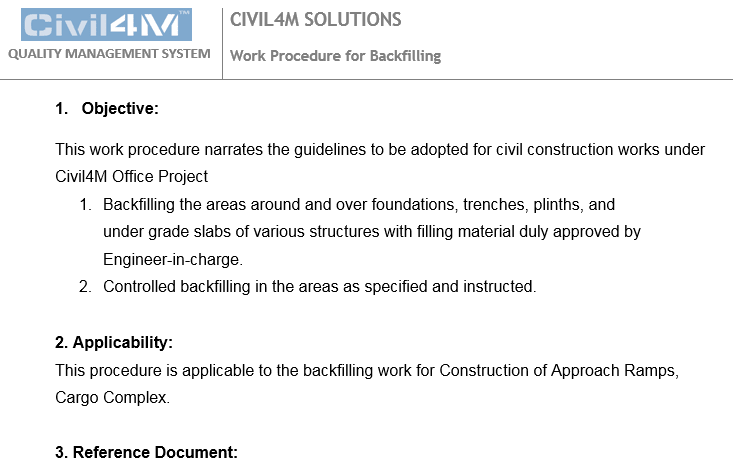
1. Objective:
This work procedure narrates the guidelines to be adopted for civil construction works under Civil4M Office Project
- Backfilling the areas around and over foundations, trenches, plinths, and under grade slabs of various structures with filling material duly approved by Engineer-in-charge.
- Controlled backfilling in the areas as specified and instructed.
2. Applicability:
This procedure is applicable to the backfilling work for Construction of Approach Ramps, Cargo Complex.
3. Reference Document:
Tender Specifications.
IS 2720 (Part V11).
Drawings
4. Responsibility:
The Project Manager shall be responsible for the overall implementation of this procedure.
5. Equipment:
a. Compaction Equipment’s
Smooth wheeled vibratory roller of 10T weight.
Smooth wheeled vibratory roller of 2T weight (to be used in the case it is found difficult to deploy 10T roller)
Pneumatic roller / Plate Compactor (to be used in space congestion where compaction by vibratory roller is not feasible.
b. Test Equipment’s
Proctor Density Test Apparatus.
Core-cutter in-situ density test apparatus
6. Backfilling procedure:
Fill Material
When directed by the engineer coarse river/crushed sand shall also be used as backfill material. Soils such as black cotton soil, clay and mixtures having excessive swelling characteristics shall not be used as filling material.
For Controlled Backfilling
Selected material from any one of the followings shall be used for controlled backfilling. Before selecting any material for backfilling, modified proctor density tests shall be conducted on the material to determine its maximum dry density. The maximum dry density shall not be less than 1.44 gm/sq.cm.
Murrum
Murrum of approved quality obtained from borrow pits duly approved by Engineer-in-charge shall be used. Murrum shall be composed of large, coarse, siliceous grains & gritty to the touch and free from dirt and foreign material.
Murrum shall not contain lumps larger than 40 mm in size. Natural clay content shall not exceed 10 % and fine sand content (i.e. passing 75micron sieve) shall not exceed 8 %.
Note:
Borrow-pits shall be got approved from Engineer-in-charge. Once approved by Engineer-in-charge, filling material shall be brought from that borrow pits.
Backfilling by Excavated Material
After completion of the foundation works, the spaces left in the pits and trenches shall be cleared of debris, brickbats, mortar droppings etc. prior to the start of backfilling.
Filling material shall be spread in layers of thickness approx. 200 mm and compacted by 4 passes of 10 T vibratory roller. Water shall be sprinkled intermittently.
Each layer shall be compacted before laying the succeeding layer. Surface voids in each layer shall be filled by crusher dust.
In case of plinth filling the backfilling as per the above procedure shall be continued up to the bottom of the plinth beam. The top surface at this stage shall be flooded with water for a minimum of 24 hrs. and defects in backfill shall be rectified and shall be trimmed to the desired level of slope, if any. Further filling within the plinth beams shall be controlled backfilling and soling as indicated in the relevant drawings.
Backfilling by Sand
Sand shall be used as filling material between foundations where space for proper compaction by mechanical means is not available and when directed by the Engineer-in-charge. Sand shall be spread in 200 mm thick layers, flooded with water and rammed. Top layer of sand shall be compacted by mechanical means.
Procedure for Controlled Backfilling
When instructed by the Engineer-in –Charge, controlled backfilling shall be done. Material shall be spread in un compacted layers of thickness approx. 200 mm and rolled by adequate number of passes of a 10T vibratory roller so as to achieve 90% of the maximum Proctor density of the fill material.
7. Safety plan:
Ensure that Jungle clearance is properly done and Remove nails, sharp edged items and other Hazardous materials / items [e.g.: snake dwelling mud holes] from the BORROWING SOURCE before commencing BORROWING activities.
Cover / barricade the unclosed utility manholes / pits if any.
Avoid using rebar cut pieces for signboards / barricading. If used - PVC rebar caps shall be fixed on top of it.
Signalman shall be kept near the FILLING area so as to alert the surrounding workers about movement of vehicles and deeply excavated pits.
Pits and diesel storage areas shall be barricaded.
Keep collection trays below excavation equipment’s like compressors etc., so as to avoid spreading of fuels etc.,
Use PPE’s [Gumboot, Hand glows, Helmet etc.].
Ensure back light and reverse horn for all the vehicles, which will be used for this filling work.
Fool proof system for reversal of vehicle to be ensured.
All the equipment’s including plate compactor shall have the guard protection for belt moving portion.
8. Inspection Records:
Field Quality Check of Backfilling
Each compacted layer shall be cleared by Engineer-in-charge for surface voids etc randomly. A record in the form of either registers or sketches for the clearance shall be maintained.
Field Quality Check of Controlled Backfilling
Each compacted layer under controlled backfilling shall be tested for degree of compaction. One test per 100 sq. m of compacted area shall be done for determining field dry density of the compacted layer. Alternate layers shall be tested as per Modified Proctor Density Test and Sand Replacement Method respectively. Records of field density test shall be maintained in the format approved by Engineer-in-charge.
FIELD DRY DENSITY TEST
MODIFIED PROCTOR DENSITY TEST
CHECK LIST
This SOP (Standard Operating Procedure) / Work Procedure is attached herewith.