Work Procedure for Dry Packing
attachment snapshot
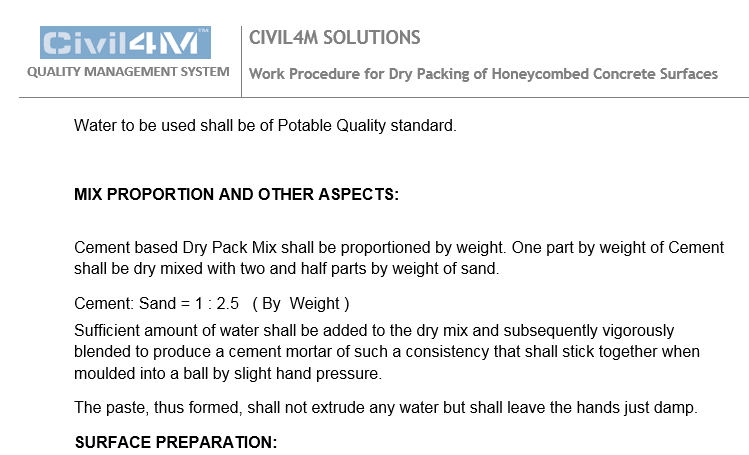
1. Objective:
Dry Packing shall be carried out for the rectification work of unsatisfactory and/or honeycombed concrete surfaces and also for treating shallow pockets on the concrete surfaces as and when instructed by the Engineer-in-charge.
2. Applicability:
Honeycombed / unsatisfactory areas on the exposed concrete surfaces of all concrete structures.
3. Reference Document:
BOQ.
Standard Specifications.
Drawings
4. Responsibility:
The Project Manager shall be responsible for the overall implementation of this procedure.
5. Safety Precautions:
Only authorized persons should handle the activities.
Use of PPE’s like goggles, hand gloves, helmet and gumboots.
6. Material’s, Equipment’s and Tools used:
Ingredients of cement based Dry pack mix are Cement, Sand and Water.
Site tested Ordinary Portland Cement conforming to IS: 1489 / 12269 shall be used. Cement shall be PPC / OPC 53 Grade.
Sand fraction passing 1.18 mm IS sieve and retained over 150 micron IS sieve and kept in dry condition shall be used for the mix.
Water to be used shall be of Potable Quality standard.
MIX PROPORTION AND OTHER ASPECTS:
Cement based Dry Pack Mix shall be proportioned by weight. One part by weight of Cement shall be dry mixed with two and half parts by weight of sand.
Cement: Sand = 1 : 2.5 ( By Weight )
Sufficient amount of water shall be added to the dry mix and subsequently vigorously blended to produce a cement mortar of such a consistency that shall stick together when moulded into a ball by slight hand pressure.
The paste, thus formed, shall not extrude any water but shall leave the hands just damp.
SURFACE PREPARATION:
Unsound portion of the concrete surface shall be chipped off and cleaned thoroughly to remove all loose aggregate, mortar and foreign materials by application of pressurized water jet. Pockets for dry pack shall have a minimum depth of 25 mm.
The pockets shall be sharp and square at the surface edges but corners within the pocket shall be rounded. Pockets shall be shown to Client for its approval to start repair work.
7. Procedure:
Surface of the pockets shall be wetted for before start of the dry packing. The pockets shall be slightly wet with no free water on the surface.
The surface shall then be dusted lightly with cement by means of dry brush. Under no conditions shall the pocket be painted with neat cement grout.
Cement and sand in specified proportion shall be dry mixed. Enough water shall then be added to the dry mix and blended vigorously. Dry pack mix shall be placed and packed in layers having a compacted thickness of about 20 mm. Each layer shall be solidly compacted over its entire surface by use of hard wood stick and hammer. The stick is normally about 300 mm to 450 mm long and not over 30 mm in diameter.
Most of the tamping shall be directed at a slight angle towards the side of the pocket to ensure maximum compaction and bond. Water shall not be used to facilitate finishing.
Immediately after patching, the patched area shall be covered with a non-staining, water saturated material. The covering sheet shall be kept wet and protected against sun and wind for a period of 12 Hrs. Thereafter the patched area shall be kept continuously moist for at least three day’s subject to achievement of specified strength.
REPAIR WORK:
Repairs shall be started as early as practicable after removal of forms and in a manner to meet the requirements of the finish specified for the particular location.
This SOP (Standard Operating Procedure) / Work Procedure is attached herewith.
attachment snapshot
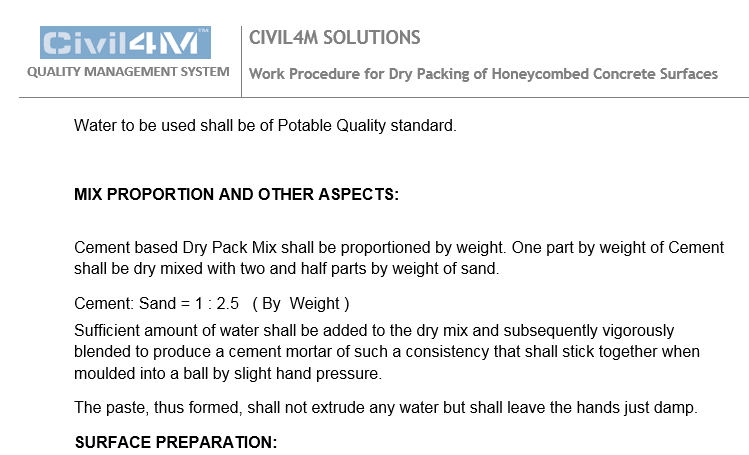
1. Objective:
Dry Packing shall be carried out for the rectification work of unsatisfactory and/or honeycombed concrete surfaces and also for treating shallow pockets on the concrete surfaces as and when instructed by the Engineer-in-charge.
2. Applicability:
Honeycombed / unsatisfactory areas on the exposed concrete surfaces of all concrete structures.
3. Reference Document:
BOQ.
Standard Specifications.
Drawings
4. Responsibility:
The Project Manager shall be responsible for the overall implementation of this procedure.
5. Safety Precautions:
Only authorized persons should handle the activities.
Use of PPE’s like goggles, hand gloves, helmet and gumboots.
6. Material’s, Equipment’s and Tools used:
Ingredients of cement based Dry pack mix are Cement, Sand and Water.
Site tested Ordinary Portland Cement conforming to IS: 1489 / 12269 shall be used. Cement shall be PPC / OPC 53 Grade.
Sand fraction passing 1.18 mm IS sieve and retained over 150 micron IS sieve and kept in dry condition shall be used for the mix.
Water to be used shall be of Potable Quality standard.
MIX PROPORTION AND OTHER ASPECTS:
Cement based Dry Pack Mix shall be proportioned by weight. One part by weight of Cement shall be dry mixed with two and half parts by weight of sand.
Cement: Sand = 1 : 2.5 ( By Weight )
Sufficient amount of water shall be added to the dry mix and subsequently vigorously blended to produce a cement mortar of such a consistency that shall stick together when moulded into a ball by slight hand pressure.
The paste, thus formed, shall not extrude any water but shall leave the hands just damp.
SURFACE PREPARATION:
Unsound portion of the concrete surface shall be chipped off and cleaned thoroughly to remove all loose aggregate, mortar and foreign materials by application of pressurized water jet. Pockets for dry pack shall have a minimum depth of 25 mm.
The pockets shall be sharp and square at the surface edges but corners within the pocket shall be rounded. Pockets shall be shown to Client for its approval to start repair work.
7. Procedure:
Surface of the pockets shall be wetted for before start of the dry packing. The pockets shall be slightly wet with no free water on the surface.
The surface shall then be dusted lightly with cement by means of dry brush. Under no conditions shall the pocket be painted with neat cement grout.
Cement and sand in specified proportion shall be dry mixed. Enough water shall then be added to the dry mix and blended vigorously. Dry pack mix shall be placed and packed in layers having a compacted thickness of about 20 mm. Each layer shall be solidly compacted over its entire surface by use of hard wood stick and hammer. The stick is normally about 300 mm to 450 mm long and not over 30 mm in diameter.
Most of the tamping shall be directed at a slight angle towards the side of the pocket to ensure maximum compaction and bond. Water shall not be used to facilitate finishing.
Immediately after patching, the patched area shall be covered with a non-staining, water saturated material. The covering sheet shall be kept wet and protected against sun and wind for a period of 12 Hrs. Thereafter the patched area shall be kept continuously moist for at least three day’s subject to achievement of specified strength.
REPAIR WORK:
Repairs shall be started as early as practicable after removal of forms and in a manner to meet the requirements of the finish specified for the particular location.
This SOP (Standard Operating Procedure) / Work Procedure is attached herewith.