Work Procedure for Plumb or Bulge Rectification
attachment snapshot
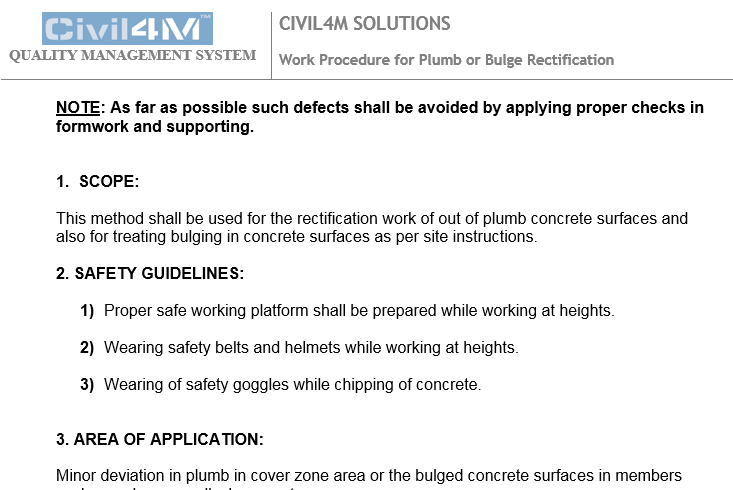
NOTE: As far as possible such defects shall be avoided by applying proper checks in formwork and supporting.
1. SCOPE:
This method shall be used for the rectification work of out of plumb concrete surfaces and also for treating bulging in concrete surfaces as per site instructions.
2. SAFETY GUIDELINES:
Proper safe working platform shall be prepared while working at heights.
Wearing safety belts and helmets while working at heights.
Wearing of safety goggles while chipping of concrete.
3. AREA OF APPLICATION:
Minor deviation in plumb in cover zone area or the bulged concrete surfaces in members such as columns, walls, beams etc.
4. MATERIALS USED:
Ingredients of cement based mortar mix are Cement, Sand and Water.
Ordinary Portland Cement or Portland Pozzolana cement conforming to IS: 12269 / 1489 shall be used.
Sand fraction passing 1.18 mm IS sieve and retained over 150 micron IS sieve and kept in dry condition shall be used for the mix.
Water to be used shall be of Potable Quality standard.
5. MIX PROPORTION AND OTHER ASPECTS:
Cement based mortar shall be proportioned as follows. One part by weight of Cement shall be dry mixed with two and half parts by weight of sand.
Cement: Sand = 1: 2.5 (By parts)
Sufficient amount of water shall be added to the dry mix and subsequently vigorously blended to produce a cement mortar of such a consistency that shall stick together when moulded into a ball by slight hand pressure.
The paste, thus formed, shall not extrude any water but shall leave the hands just damp.
6. SURFACE PREPARATION:
6.1. Deviated portion of the concrete surface shall be chipped off and cleaned thoroughly by wire brush to get rough sound concrete surface for bonding of plastering materials.
7. PROCEDURE OF RECTIFICATION:
Application:
Chipped surface of member shall be slightly wetted with no free water on the surface.
Cement and sand in specified proportion shall be dry mixed. Enough water shall then be added to the dry mix and blended vigorously. Dry pack mix shall be placed and packed in layers having a compacted thickness of about 10 mm. Most of the tamping shall be directed to ensure maximum compaction and bond.
Finishing:
Finished portion shall be brought to required line and verticality with straight edge and plumb bob. Edges and corners if any shall be maintained in right angle. Excess cement shall not be used to facilitate finishing.
Curing:
Immediately after patching, the finished area shall be covered with a non-staining, water saturated material. The covering sheet shall be kept wet and protected against sun and wind for a period of 12 Hrs. Thereafter the patched area shall be kept continuously moist for at least three day’s subject to achievement of specified strength.
8. REPAIR WORK:
Repairs shall be started as early as practicable after removal of forms and in a manner to meet the requirements of the finish specified for the particular location.
This SOP (Standard Operating Procedure) / Work Procedure is attached herewith.
attachment snapshot
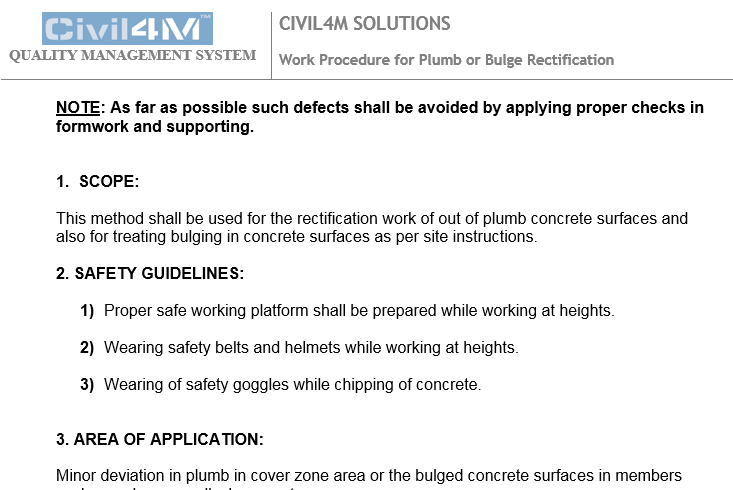
NOTE: As far as possible such defects shall be avoided by applying proper checks in formwork and supporting.
1. SCOPE:
This method shall be used for the rectification work of out of plumb concrete surfaces and also for treating bulging in concrete surfaces as per site instructions.
2. SAFETY GUIDELINES:
Proper safe working platform shall be prepared while working at heights.
Wearing safety belts and helmets while working at heights.
Wearing of safety goggles while chipping of concrete.
3. AREA OF APPLICATION:
Minor deviation in plumb in cover zone area or the bulged concrete surfaces in members such as columns, walls, beams etc.
4. MATERIALS USED:
Ingredients of cement based mortar mix are Cement, Sand and Water.
Ordinary Portland Cement or Portland Pozzolana cement conforming to IS: 12269 / 1489 shall be used.
Sand fraction passing 1.18 mm IS sieve and retained over 150 micron IS sieve and kept in dry condition shall be used for the mix.
Water to be used shall be of Potable Quality standard.
5. MIX PROPORTION AND OTHER ASPECTS:
Cement based mortar shall be proportioned as follows. One part by weight of Cement shall be dry mixed with two and half parts by weight of sand.
Cement: Sand = 1: 2.5 (By parts)
Sufficient amount of water shall be added to the dry mix and subsequently vigorously blended to produce a cement mortar of such a consistency that shall stick together when moulded into a ball by slight hand pressure.
The paste, thus formed, shall not extrude any water but shall leave the hands just damp.
6. SURFACE PREPARATION:
6.1. Deviated portion of the concrete surface shall be chipped off and cleaned thoroughly by wire brush to get rough sound concrete surface for bonding of plastering materials.
7. PROCEDURE OF RECTIFICATION:
Application:
Chipped surface of member shall be slightly wetted with no free water on the surface.
Cement and sand in specified proportion shall be dry mixed. Enough water shall then be added to the dry mix and blended vigorously. Dry pack mix shall be placed and packed in layers having a compacted thickness of about 10 mm. Most of the tamping shall be directed to ensure maximum compaction and bond.
Finishing:
Finished portion shall be brought to required line and verticality with straight edge and plumb bob. Edges and corners if any shall be maintained in right angle. Excess cement shall not be used to facilitate finishing.
Curing:
Immediately after patching, the finished area shall be covered with a non-staining, water saturated material. The covering sheet shall be kept wet and protected against sun and wind for a period of 12 Hrs. Thereafter the patched area shall be kept continuously moist for at least three day’s subject to achievement of specified strength.
8. REPAIR WORK:
Repairs shall be started as early as practicable after removal of forms and in a manner to meet the requirements of the finish specified for the particular location.
This SOP (Standard Operating Procedure) / Work Procedure is attached herewith.