Guidelines for concrete mix designing revised with revision in IS 10262 in 2019.
I am sharing the excel sheet for concrete mix proportioning which is purely base on IS 10262 and can be used for designing of the normal concrete mixes from M10 to M60 grade with option of blending cement by doing part replacement with single mineral admixture.
You can still design the mixes using this excel sheet up to M80 grade and replacement possible in excel sheet is with single mineral admixture. after proportioning you can replace the cement from 5 to 10% with silica fume to achieve the desired result in high performance concrete mixes.
This excel sheet does not include the mix designing of Self Compacting Concrete and Mass Concrete Mixes.
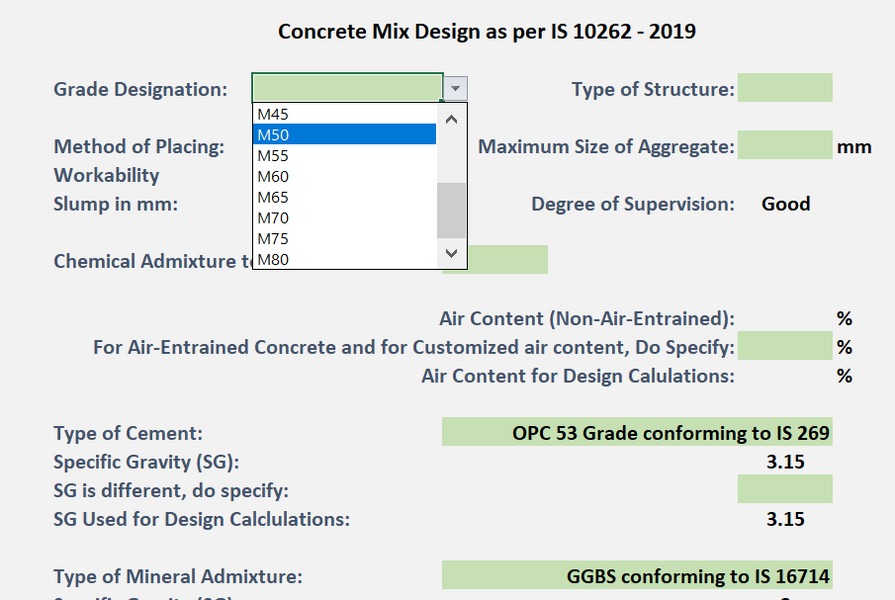
The excel sheet is very simple to use and anyone with basic knowledge of the materials can do mix designing using this sheet, the process of designing of the mixes to be followed;
Do write the details in the green cells only and do not make edit in other cell as the excel sheet is not protected with password and you can edit anywhere in the sheet, accidental edits in the cells may lead to errors in the mix design sheet due to overriding of formula by values edited by you.
To design a mixes, start entering the data in following sequence.
Select the grade of concrete mix which you want to design from the drop down list, you have a choice in drop down from M10 to M80.
Select the type of structure from the drop down list - structures are defined as PCC and RCC as the durability requirements are associated with this two types.
Method of Placing - Select from the drop down - Either dump or pump. dump represents the concrete operations where manual handling of concrete do happens for pouring such as direct pouring, using chutes for pouring etc and in pump type concrete, pumping operations are involved which may be stationary concrete pump or movable mobile pump like boom placer - this has impact on the required amount of water for mix proportioning.
Maximum Size of Aggregates - Currently MSA is up to 20 mm size and in drop down you have option to design with either 20mm or 10mm as maximum size of aggregates - higher sizes will be included in mass concrete excel sheet for concrete mix design.
Workability in terms of slump value - Select the desired workability from the drop down from 0 to 200 mm.
Chemical Admixture to be used - you have two options in drop down either yes or no. if you are going to used Chemical Admixture then you need to have the details of admixture with you which are required for doing calculation and finalizing the mix proportions.
Air Content - Air content is automatically selected from the code as per MSA for non-air-entrained concrete, you can specify the air content value if you are designing air-entrained concrete or wish to have different air content by writing it in green cell.
Type of Cement - Select from the drop down the type of cement to be used, the strength calculations are base on the standard graph published in IS 10262 -2019 from W/c Ratio and strength of the cement. The specific gravity value is taken automatically but if the cement which you are using has different specific gravity, you can specify the same and that will be taken for doing calculations.
Recreated graph (there might be small error due to human factor of interpretation of reading from the graph but will not have the impact on overall mix because the error would be very small) for strength of the 53, 43 and, 33 grade cement, calculation of the strength at each fraction of the W/c ratio is done mathematically using polynomial equation of degree 6 (this also creates some factor of safety to remove or minimize the human reading error).
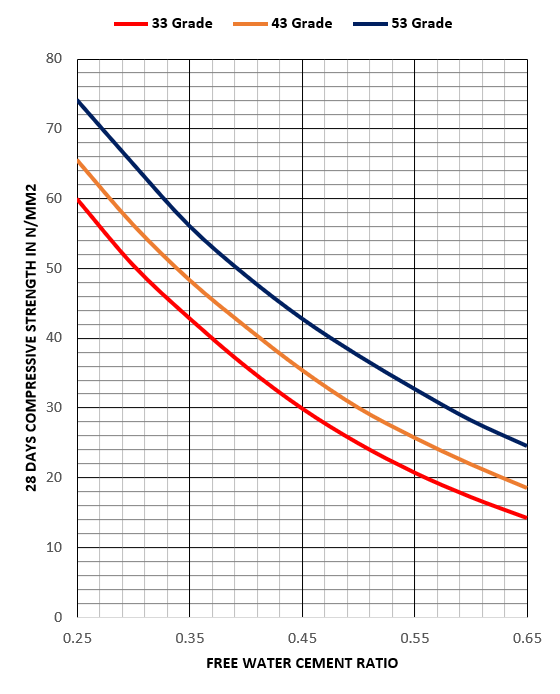
Type of Mineral Admixtures - You get a choice of mineral admixture in drop down list and similarly like cement you can specify specific gravity if it is different from automatically taken value.
Exposure Condition - You need to select the exposure condition in which this concrete will be there for its whole life. to get detailed idea about exposure conditions for concrete, do refer IS 456 tables mentioning in details when to call which condition with detailed explanation about the exposure environment.
According to selected exposure condition excel sheet verifies the data and raises alarm if durability aspects are not met by the mix, do corrections accordingly in alerted parameters.
Type of aggregate - select the type base on shape from the drop down list - shape of the aggregate has impact on the total water requirement so select correctly.
You need to write basic properties of the aggregates such as Specific Gravity and Water Absorption is respective green cells.
Zone of the fine aggregates - Select the zone of fine aggregate from the drop down list.
Combine gradation of the aggregates as per IS 383 requirement
For combine gradation normally falls in 60% : 40% ratio for 20mm to 10mm which is taken as default value.
Do write the % passing of each aggregate in the respective green cells for 20mm and 10mm in case of MSA is 20mm and only 10mm in case of MSA is 10mm. the below picture with red rectangle shows the area where it need to be entered.
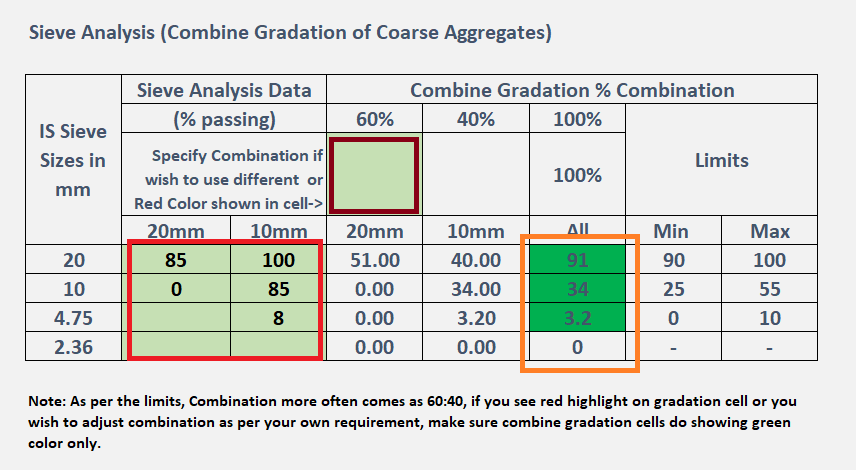
The final values in the orange box shown above in the image shall have all cells with green highlights, if any cell turns with red highlight, it means you need to change the combination to meet the requirement.
To change the combination, specify the % value of 20mm in Brown box shown in above image. if all cells are green in orange box there is no need to change this combination but if you wish to use different combination, you can always change it to suit your requirement.
Chemical Admixture Details - If you have selected yes for using it, do specify the details by writing it in green cells.
Mix Design Calculations - here the entered data processing starts and the values are generated, you have a choice to specify the different standard deviation value other than assumed one from the code, but to make a mix proof, the code also added a new criteria to make minimum target strength for designing of mixes.
The target value is chosen automatically and it will be higher in case of entered standard deviation values is higher than the assumed value.
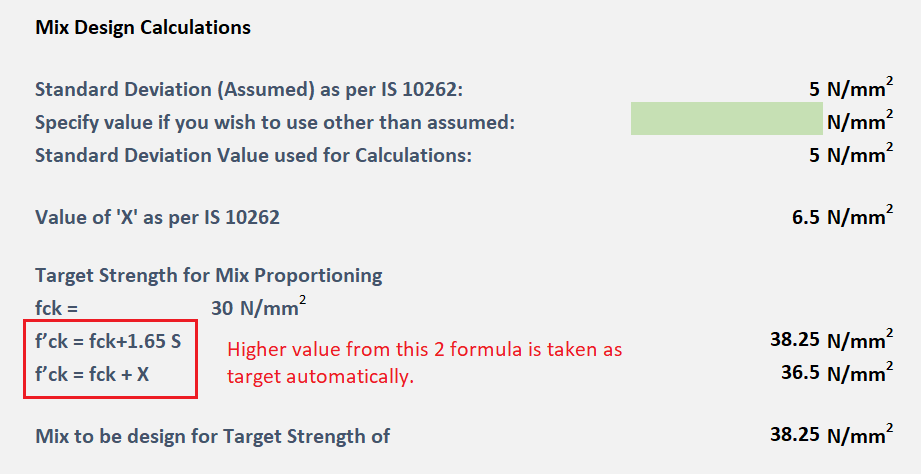
After targeting for the strength, water cement ratio is calculated from the graph and verified against the durability requirements.
In case if it fails to meet the durability requirement or you wish to use other wc ratio than the calculated one which meets durability requirement, you can specify same in the green cell.
Base on that required water is calculated and required cementitious material in mix is also calculated.
In case of pure mixes cementitious content will be treated as cement only.
in case when mineral admixture is used, you get a choice for specifying replacement value for it along with display of recommended values for replacement.
You can specify the value as shown in below image, which generates a final mix proportion for doing trials.
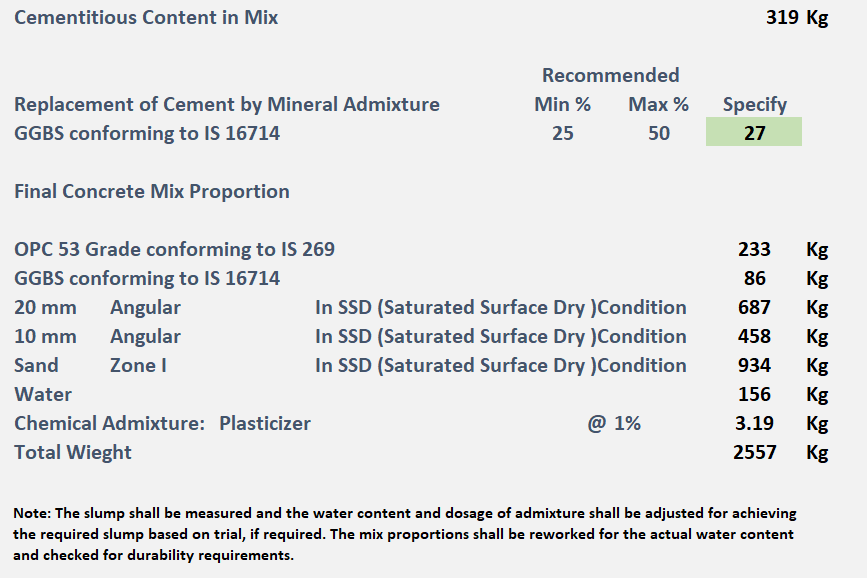
Now you have completed the process of doing mix designing of the concrete.
It is important to take a note of, the designed concrete mixes are theoretical approach, you need to verify the performance of the same by doing trials of designed mixes in lab before deployment of same in actual production.
IS recommends to do trials for same mixes by reducing and increasing the water content by 10% and plotting the relation between strength and wc ratio for designed concrete.
Upon doing trials, base on your observations, you can rework the mix to say either reducing water content, cement content, aggregate proportion etc. and reverification of same to ensure it meets durability requirement.
Rework in mix can be done using same excel sheet by modifying desired properties to ensure meeting of durability criteria. reworked mix shall again subjected to trials before deployment in actual production.
You can find the final mixes as per criteria for doing trial on tab namely Trial Mixes.
We also added a tab namely Information which also serve as guide in designing of mixes.
Hope this excel sheet helps you in quick designing of mixes correctly as per the guidelines and saving your productive time.
In case of any difficulties or errors observed in sheet, do reply here, i will try to fix them at earliest and make sure release of updated sheet.
You can download this concrete mix design sheet from below attachment section.
Concrete mix design sheet is updated (there was a problem of not showing aggregate quantities in final mix proportion when we select use of the admixture).
I am sharing the excel sheet for concrete mix proportioning which is purely base on IS 10262 and can be used for designing of the normal concrete mixes from M10 to M60 grade with option of blending cement by doing part replacement with single mineral admixture.
You can still design the mixes using this excel sheet up to M80 grade and replacement possible in excel sheet is with single mineral admixture. after proportioning you can replace the cement from 5 to 10% with silica fume to achieve the desired result in high performance concrete mixes.
This excel sheet does not include the mix designing of Self Compacting Concrete and Mass Concrete Mixes.
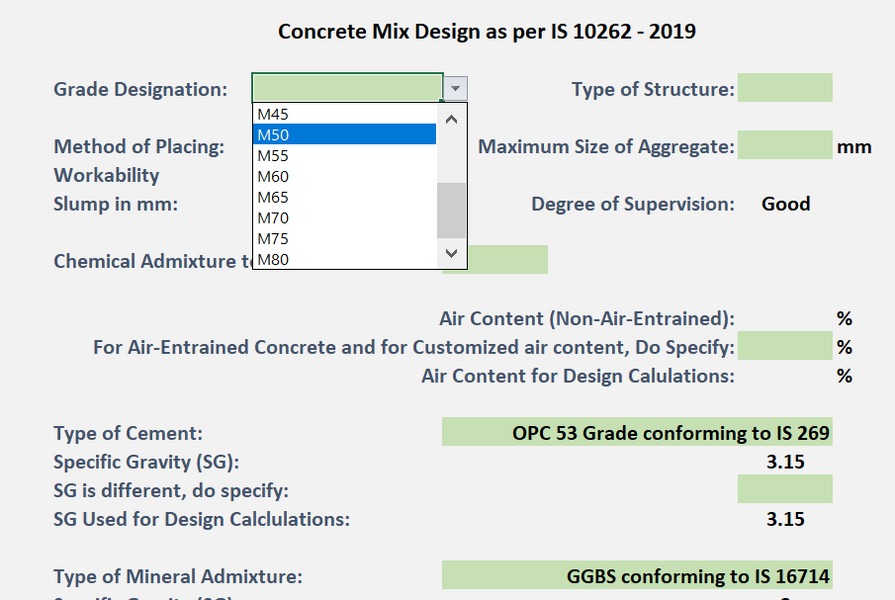
The excel sheet is very simple to use and anyone with basic knowledge of the materials can do mix designing using this sheet, the process of designing of the mixes to be followed;
Do write the details in the green cells only and do not make edit in other cell as the excel sheet is not protected with password and you can edit anywhere in the sheet, accidental edits in the cells may lead to errors in the mix design sheet due to overriding of formula by values edited by you.
To design a mixes, start entering the data in following sequence.
Select the grade of concrete mix which you want to design from the drop down list, you have a choice in drop down from M10 to M80.
Select the type of structure from the drop down list - structures are defined as PCC and RCC as the durability requirements are associated with this two types.
Method of Placing - Select from the drop down - Either dump or pump. dump represents the concrete operations where manual handling of concrete do happens for pouring such as direct pouring, using chutes for pouring etc and in pump type concrete, pumping operations are involved which may be stationary concrete pump or movable mobile pump like boom placer - this has impact on the required amount of water for mix proportioning.
Maximum Size of Aggregates - Currently MSA is up to 20 mm size and in drop down you have option to design with either 20mm or 10mm as maximum size of aggregates - higher sizes will be included in mass concrete excel sheet for concrete mix design.
Workability in terms of slump value - Select the desired workability from the drop down from 0 to 200 mm.
Chemical Admixture to be used - you have two options in drop down either yes or no. if you are going to used Chemical Admixture then you need to have the details of admixture with you which are required for doing calculation and finalizing the mix proportions.
Air Content - Air content is automatically selected from the code as per MSA for non-air-entrained concrete, you can specify the air content value if you are designing air-entrained concrete or wish to have different air content by writing it in green cell.
Type of Cement - Select from the drop down the type of cement to be used, the strength calculations are base on the standard graph published in IS 10262 -2019 from W/c Ratio and strength of the cement. The specific gravity value is taken automatically but if the cement which you are using has different specific gravity, you can specify the same and that will be taken for doing calculations.
Recreated graph (there might be small error due to human factor of interpretation of reading from the graph but will not have the impact on overall mix because the error would be very small) for strength of the 53, 43 and, 33 grade cement, calculation of the strength at each fraction of the W/c ratio is done mathematically using polynomial equation of degree 6 (this also creates some factor of safety to remove or minimize the human reading error).
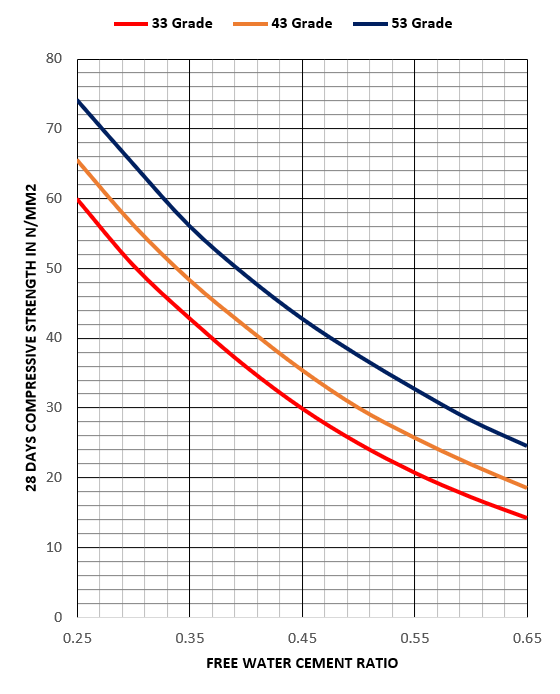
Type of Mineral Admixtures - You get a choice of mineral admixture in drop down list and similarly like cement you can specify specific gravity if it is different from automatically taken value.
Exposure Condition - You need to select the exposure condition in which this concrete will be there for its whole life. to get detailed idea about exposure conditions for concrete, do refer IS 456 tables mentioning in details when to call which condition with detailed explanation about the exposure environment.
According to selected exposure condition excel sheet verifies the data and raises alarm if durability aspects are not met by the mix, do corrections accordingly in alerted parameters.
Type of aggregate - select the type base on shape from the drop down list - shape of the aggregate has impact on the total water requirement so select correctly.
You need to write basic properties of the aggregates such as Specific Gravity and Water Absorption is respective green cells.
Zone of the fine aggregates - Select the zone of fine aggregate from the drop down list.
Combine gradation of the aggregates as per IS 383 requirement
For combine gradation normally falls in 60% : 40% ratio for 20mm to 10mm which is taken as default value.
Do write the % passing of each aggregate in the respective green cells for 20mm and 10mm in case of MSA is 20mm and only 10mm in case of MSA is 10mm. the below picture with red rectangle shows the area where it need to be entered.
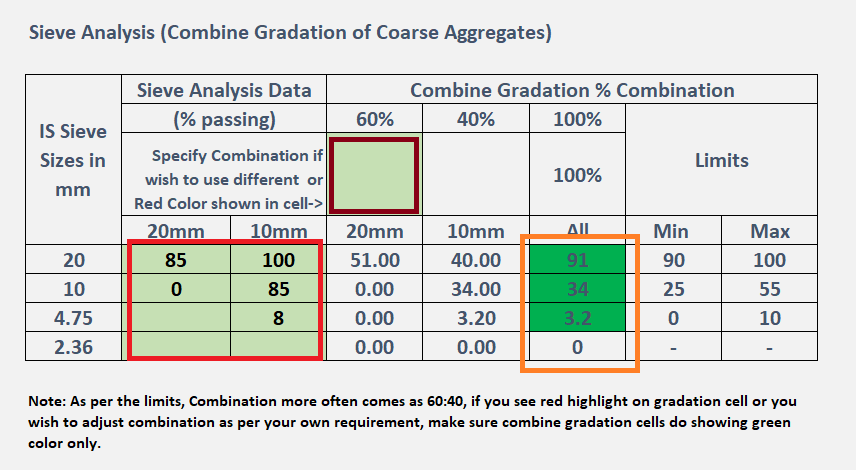
The final values in the orange box shown above in the image shall have all cells with green highlights, if any cell turns with red highlight, it means you need to change the combination to meet the requirement.
To change the combination, specify the % value of 20mm in Brown box shown in above image. if all cells are green in orange box there is no need to change this combination but if you wish to use different combination, you can always change it to suit your requirement.
Chemical Admixture Details - If you have selected yes for using it, do specify the details by writing it in green cells.
Mix Design Calculations - here the entered data processing starts and the values are generated, you have a choice to specify the different standard deviation value other than assumed one from the code, but to make a mix proof, the code also added a new criteria to make minimum target strength for designing of mixes.
The target value is chosen automatically and it will be higher in case of entered standard deviation values is higher than the assumed value.
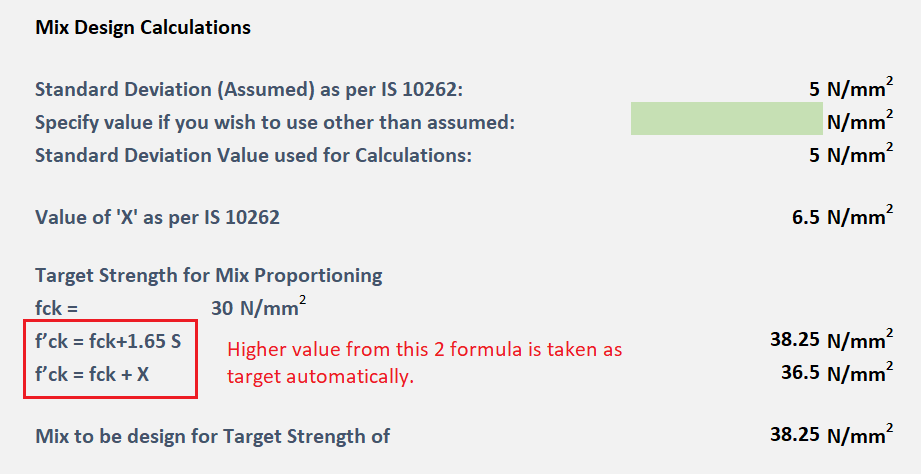
After targeting for the strength, water cement ratio is calculated from the graph and verified against the durability requirements.
In case if it fails to meet the durability requirement or you wish to use other wc ratio than the calculated one which meets durability requirement, you can specify same in the green cell.
Base on that required water is calculated and required cementitious material in mix is also calculated.
In case of pure mixes cementitious content will be treated as cement only.
in case when mineral admixture is used, you get a choice for specifying replacement value for it along with display of recommended values for replacement.
You can specify the value as shown in below image, which generates a final mix proportion for doing trials.
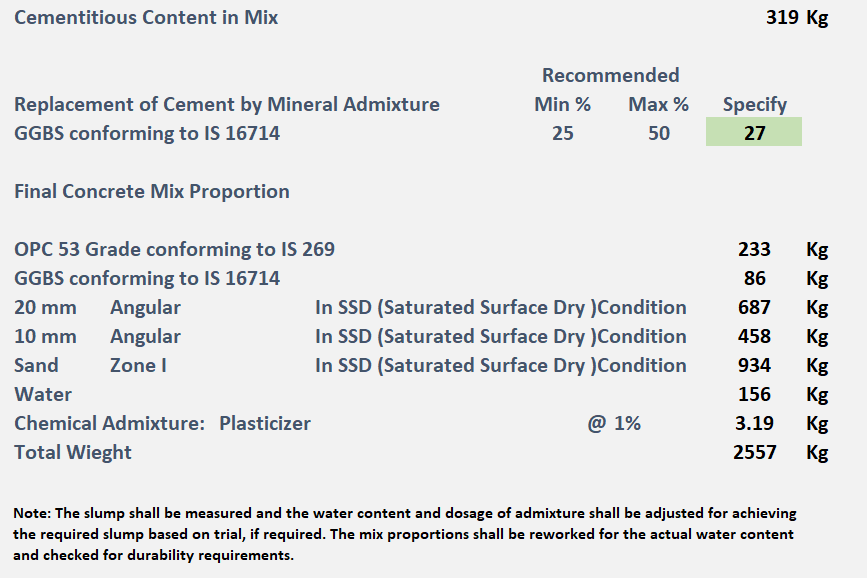
Now you have completed the process of doing mix designing of the concrete.
It is important to take a note of, the designed concrete mixes are theoretical approach, you need to verify the performance of the same by doing trials of designed mixes in lab before deployment of same in actual production.
IS recommends to do trials for same mixes by reducing and increasing the water content by 10% and plotting the relation between strength and wc ratio for designed concrete.
Upon doing trials, base on your observations, you can rework the mix to say either reducing water content, cement content, aggregate proportion etc. and reverification of same to ensure it meets durability requirement.
Rework in mix can be done using same excel sheet by modifying desired properties to ensure meeting of durability criteria. reworked mix shall again subjected to trials before deployment in actual production.
You can find the final mixes as per criteria for doing trial on tab namely Trial Mixes.
We also added a tab namely Information which also serve as guide in designing of mixes.
Hope this excel sheet helps you in quick designing of mixes correctly as per the guidelines and saving your productive time.
In case of any difficulties or errors observed in sheet, do reply here, i will try to fix them at earliest and make sure release of updated sheet.
You can download this concrete mix design sheet from below attachment section.
Concrete mix design sheet is updated (there was a problem of not showing aggregate quantities in final mix proportion when we select use of the admixture).
Attachments
Last edited: