How Flush Door Shutters are made - Insight of Door Factory
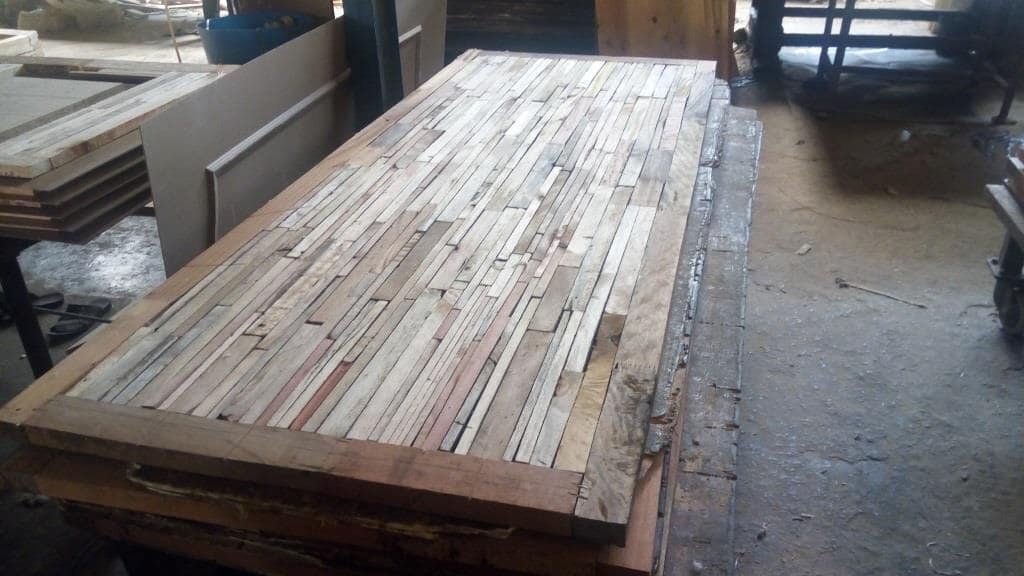
Before proceeding to how flush door shutters are made inside the factory, first take a look at the specifications given in IS 2202 Part 1 for making of it.
Stiles and rails should be of minimum 45 mm and shall not exceed by 75mm in width. Both should be of hard wood given in group 2A and group 2B.
The suitability of timber for stiles, rails and lipping normally based on screw holding properties of timber.
Blockboard – Wooden strip filled to make core of shutter shall be of single species and should not be more than 30mm in width. These strips may consist of pieces of small lengths placed end to end with the end joints staggered.
Moisture content in wood used for manufacturing door shutter shall not be more than 12%
In case of Particle board or medium density fiber (MDF) board core with blockboard, the width of blockboard constructed shall not be less than 150 mm from inner edge of the stile on either sides.
The Rails shall be made without any joint.
The Stile shall be made with maximum one finger or scarf type joint as per following details;
IS Code also state for Lock arrangement in shutters, it says;
Shutter shall be shop prepared for taking mortice locks or latches as may be agreed to. Shop preparing the door with mortice holes for lock fixing shall be done only when desire, suitable block of wood may be provided for fixing the hardware, in absence of specific requirement, the size of block shall be preferably corresponding to maximum size of lock covered in IS 2209.
All above are the basic requirements.
In India, Now days all solid core type flush door shutters are made up of scrap pine wood completely.
Pine is not a hard wood but still it is used for complete construction of shutter due to its cost effectiveness.
The pine scrap wood is dumped at factory via trucks, the pine wood received is generally 2 to 4 feet long.
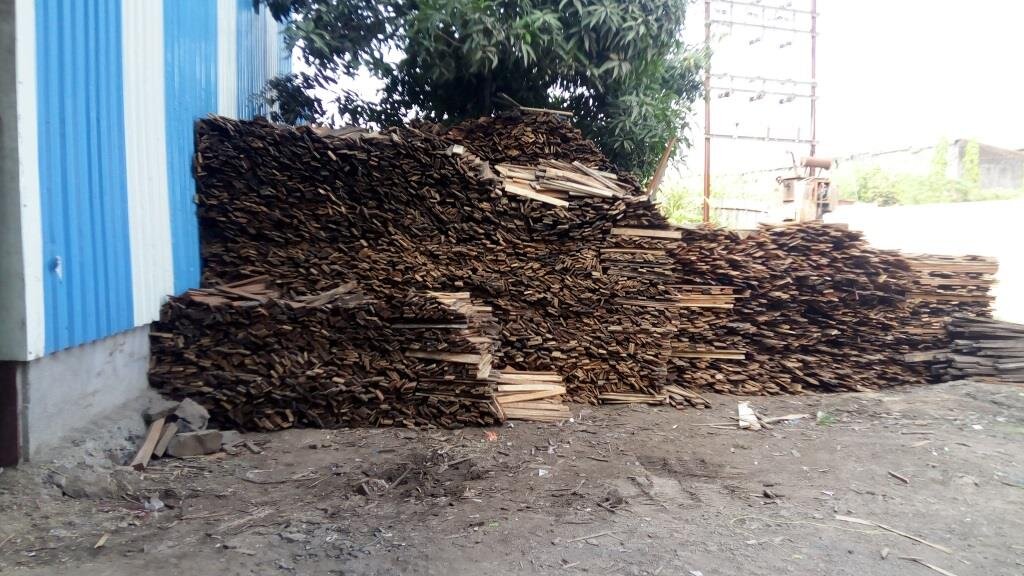
After receiving the wood, it is processed under the seasoning chamber to reduce its moisture content and make it below 12%. Generally, wood is made to complete dry condition in the seasoning chamber.
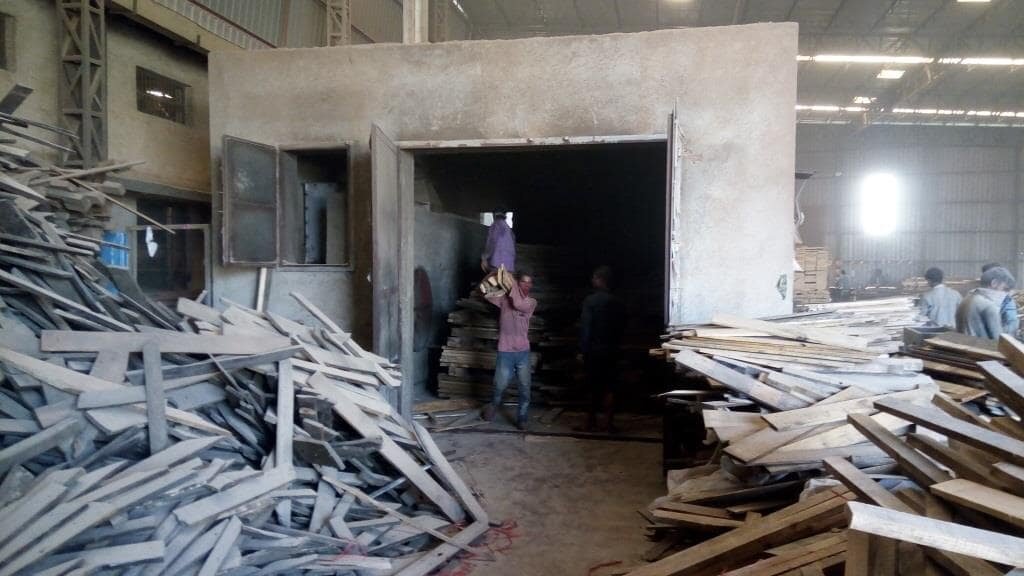
After removing the moisture to desired level, the pieces of pine wood then stacked outside to make it in sizes required. Wood tend to deformed in shape when the moisture level in wood changes and also it does get cracked after drying.
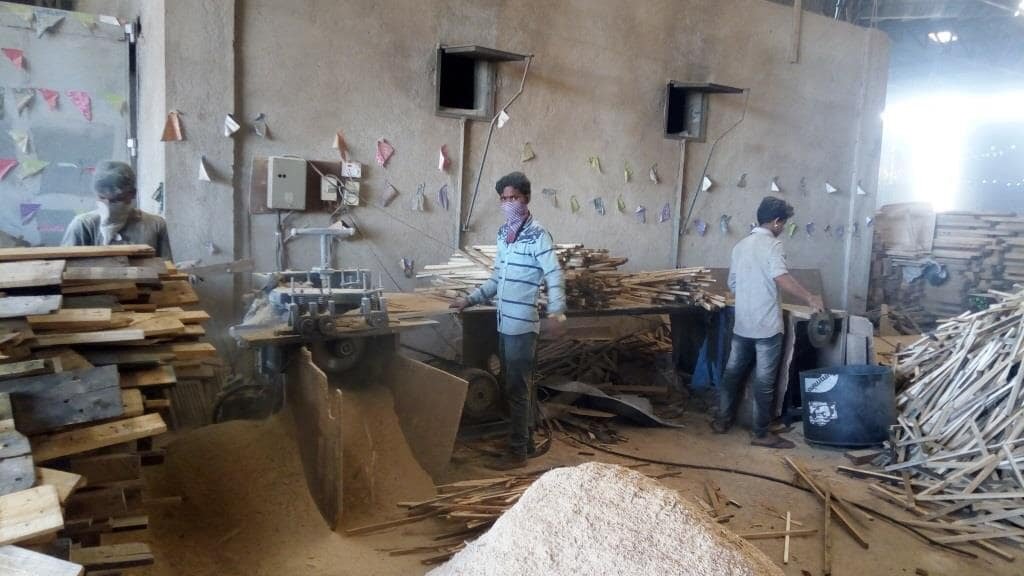
After sizing it to required level, it is stacked near machine and this is used for making blockboard and framing of door shutter.
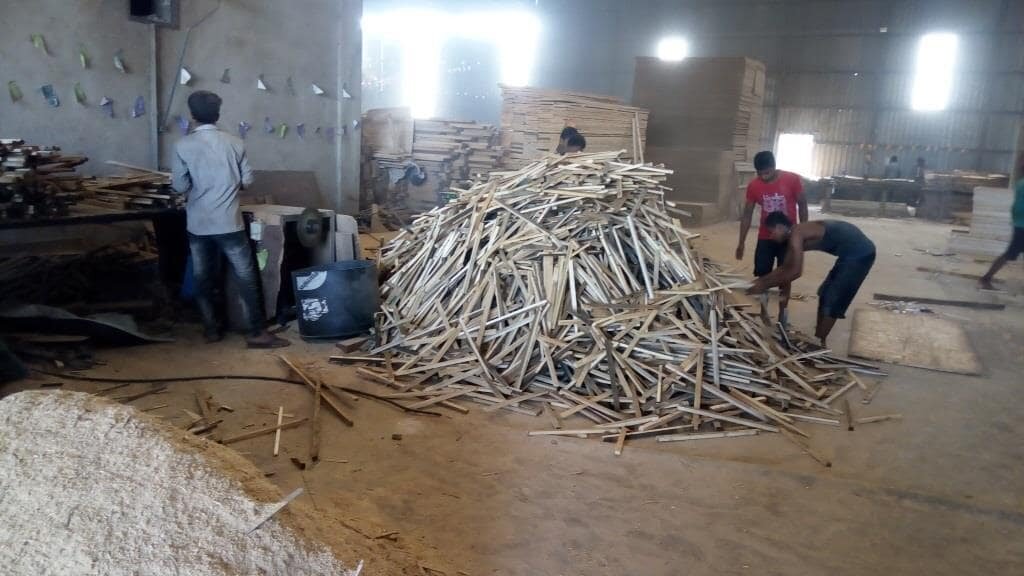
As the wood is scrape, it will be in size from 2 to 4 feet and height of the shutter is normally around 7 to 8 feet. Those pieces of wood then joined together by making finger joints.
Before making the stile and rails, the wood goes through the planner and finger joint making machine.
Below is the photo of planner which makes the wood in uniform thickness.
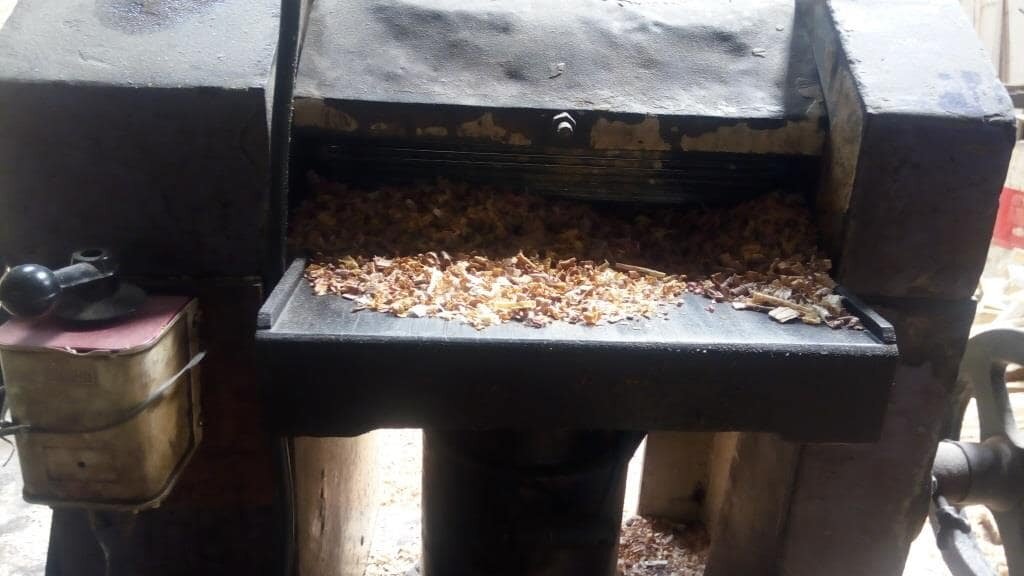
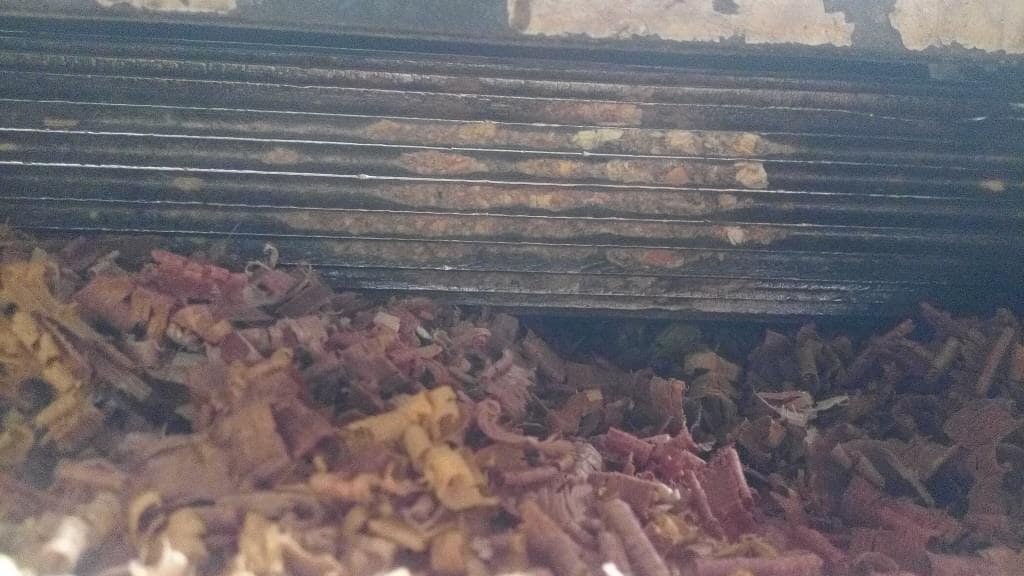
After this, finger joints are made on each piece of wood
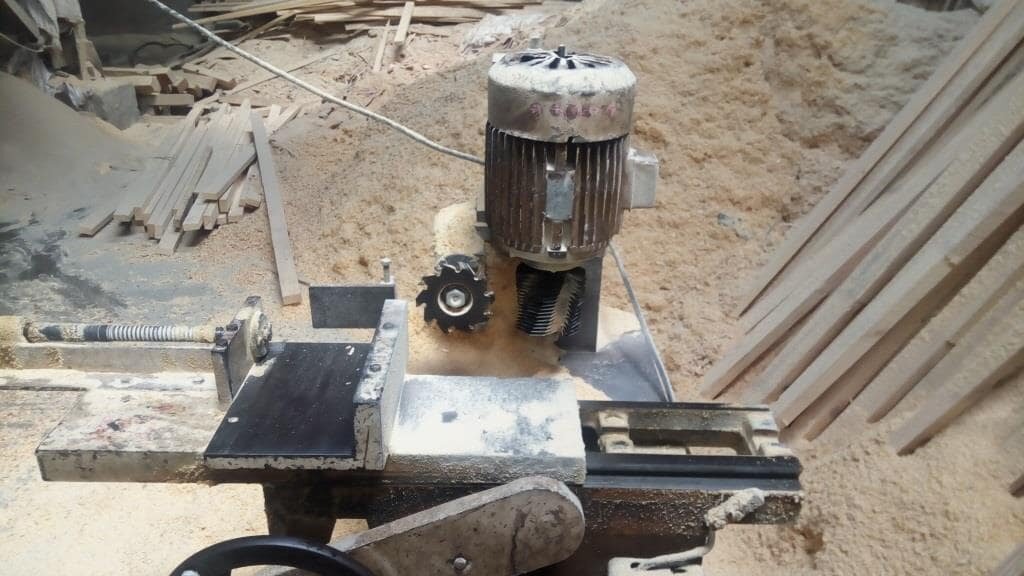
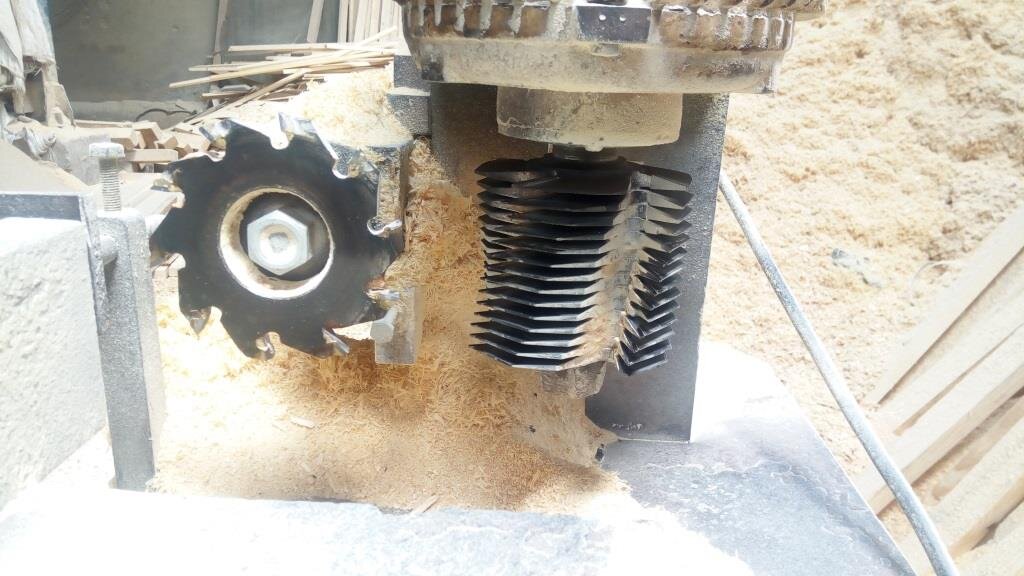
A wood just passed through the machine showing carving of finger joint on it
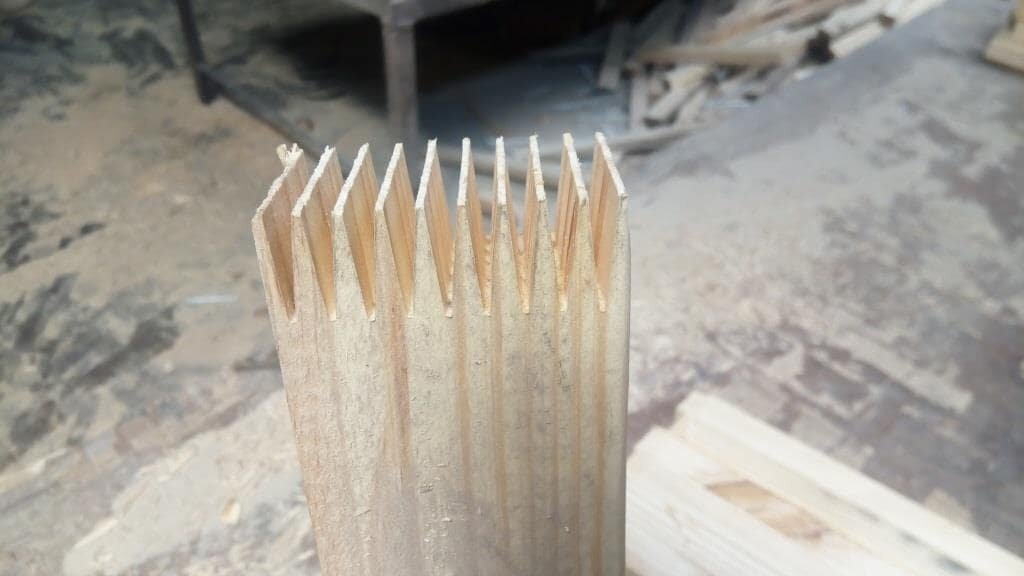
Those pieces of wood then joint together with high strength glue adhesive to make a long stile and rail on a steel frame structure where straightness of wood is ensured
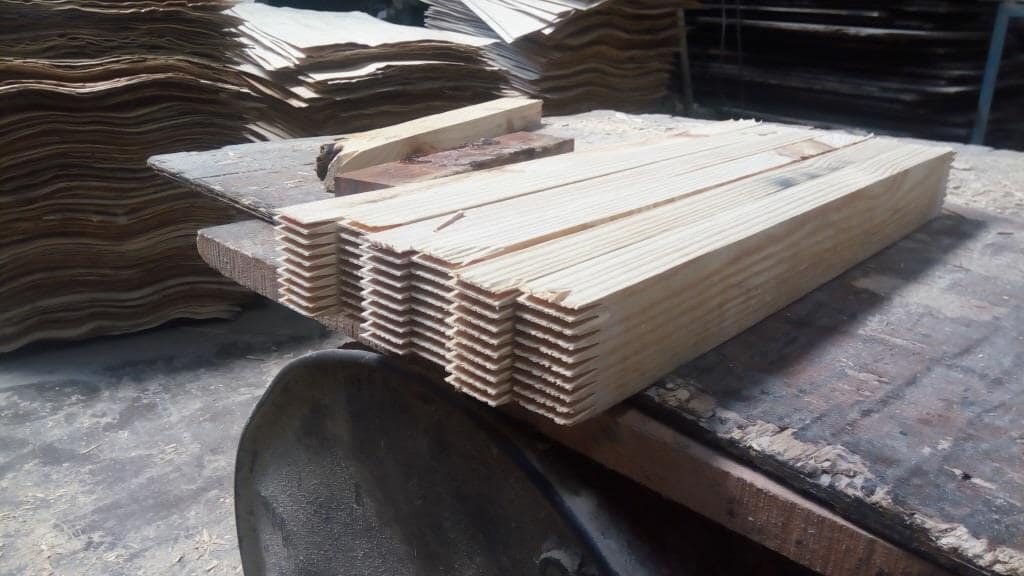
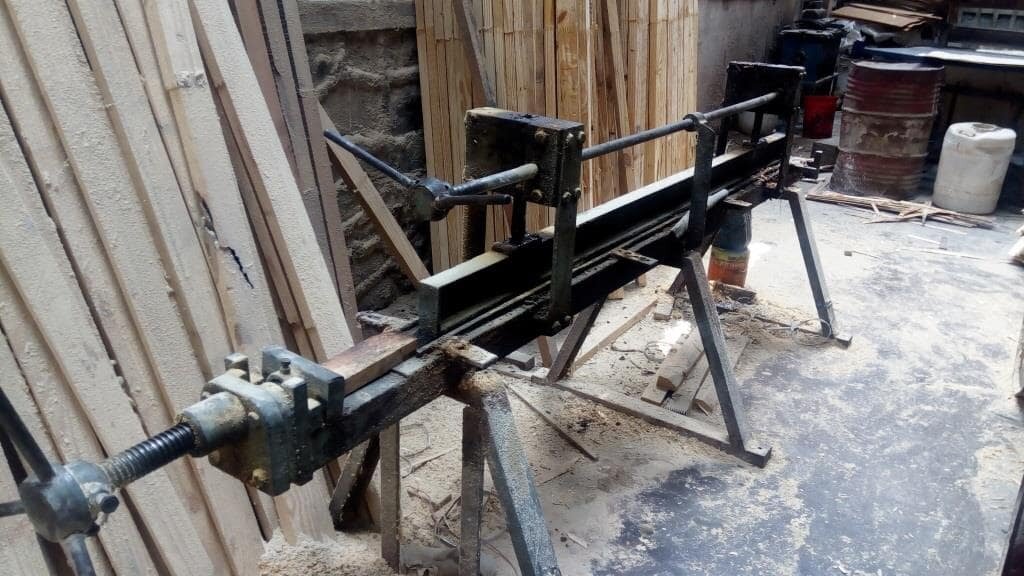
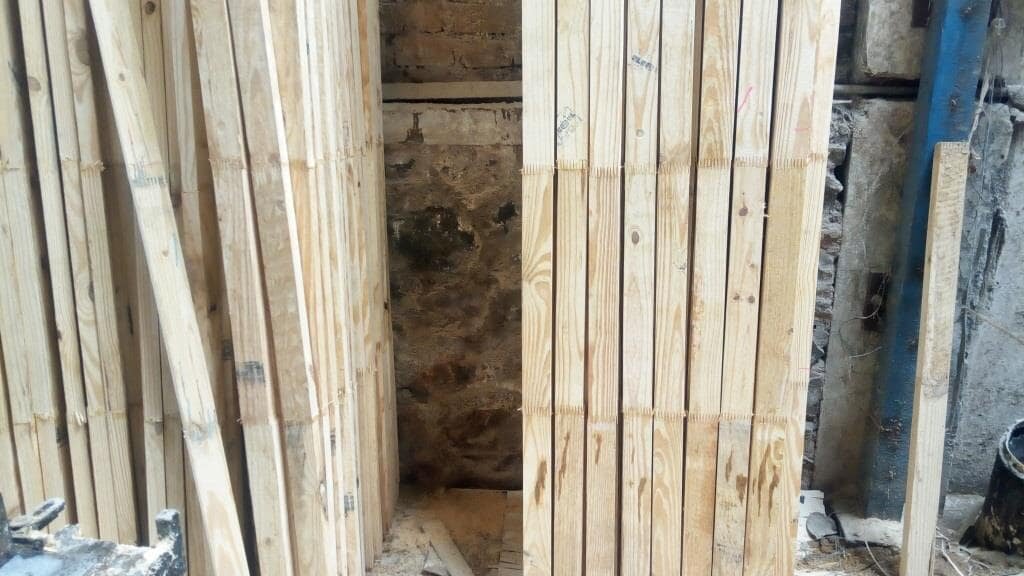
After construction of stiles and rails, a frame structure is made out of it of desired length and width. The right angles and dimensions of frame are checked at the time of making of it
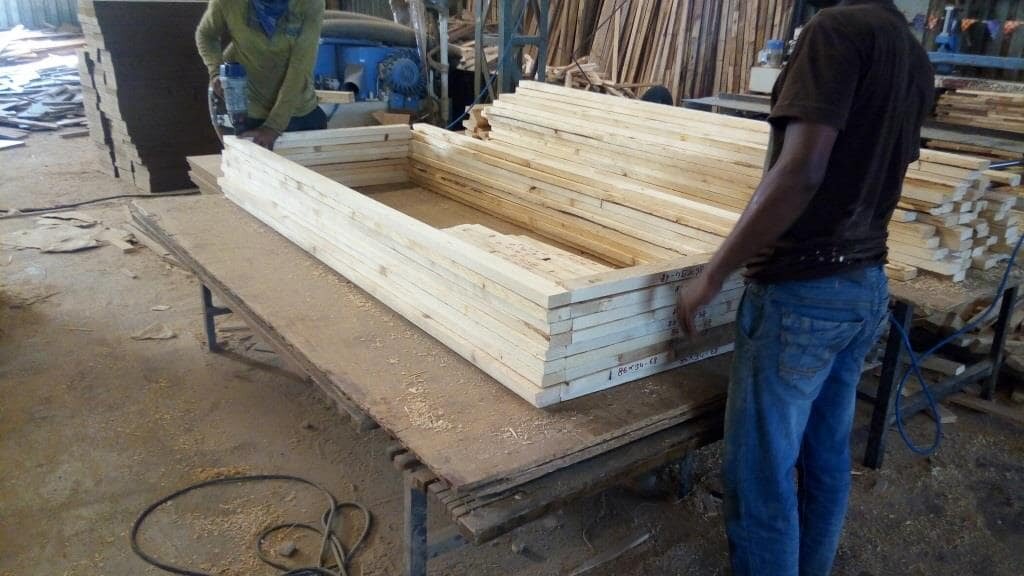
The jointing of the frame is done by using a stapler pins around 3 to 4 mm, at each joint 2 pins were installed using pneumatic stapler machine which works on the air pressure. Stapler pin only works on soft wood, in case of hard wood cotter pins need to be installed at each joint. Cotter pin lead to breakages in soft wood as it wont take much pressure or due to its softness.
Below is the phot of stapler pin
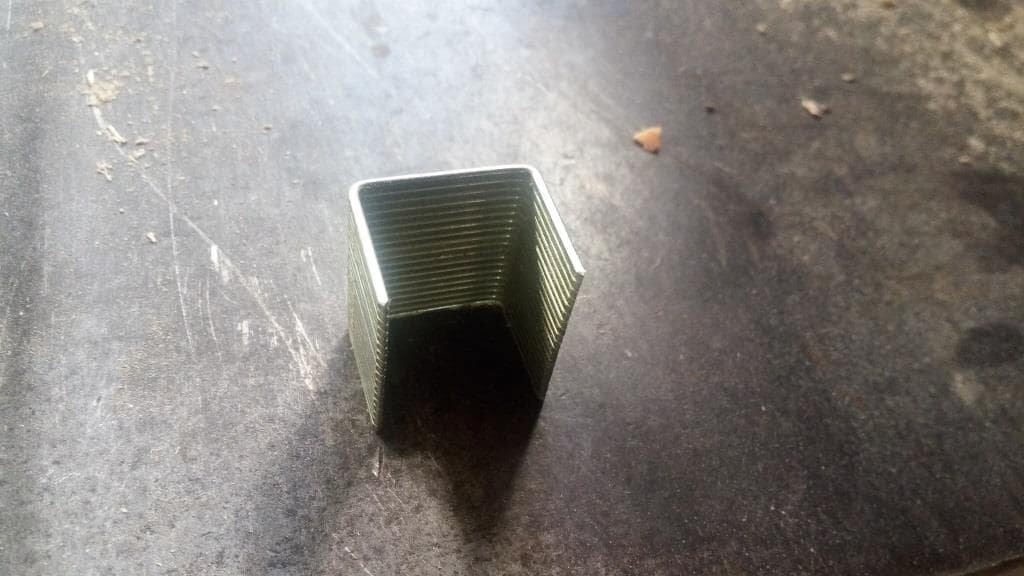
Below is the photo of pneumatic stapler
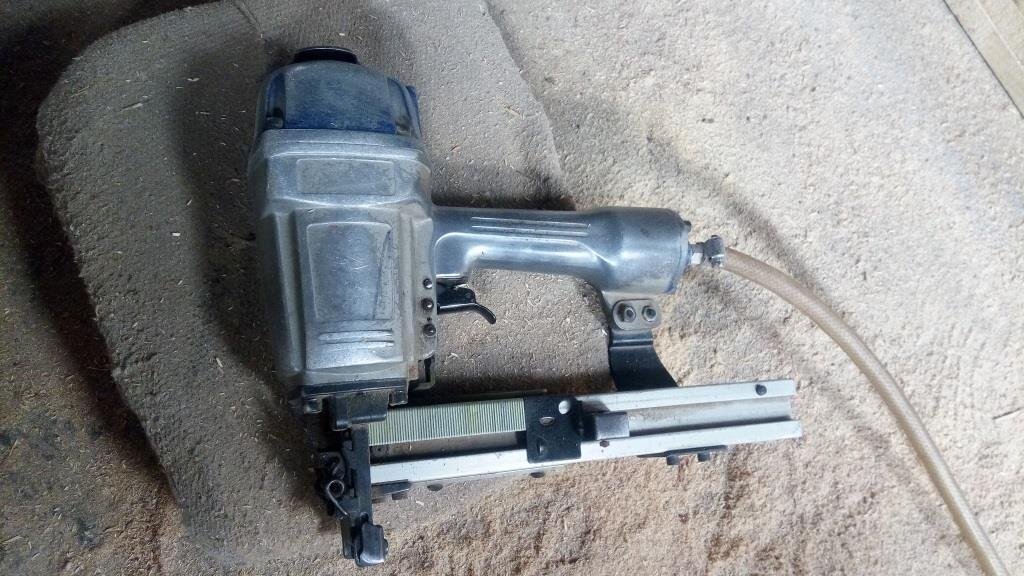
After making of frame, it is then placed on a levelled surface of plywood or metal sheet and as per the design, either blockboard or combination of blockboard and MDF board or complete MDF board is made inside of it base on the requirement given.
Below is the photo where blockboard is made inside the frame, blockboard is made using pine strips of not more than 30 cm in width. The workmen fits the stips inside the frame by ensuring joints of strips get staggered in installed pieces. After filling of blocks in it, the small pieces of wood inserted at 2 to 3 places to make the fill tighter in it.
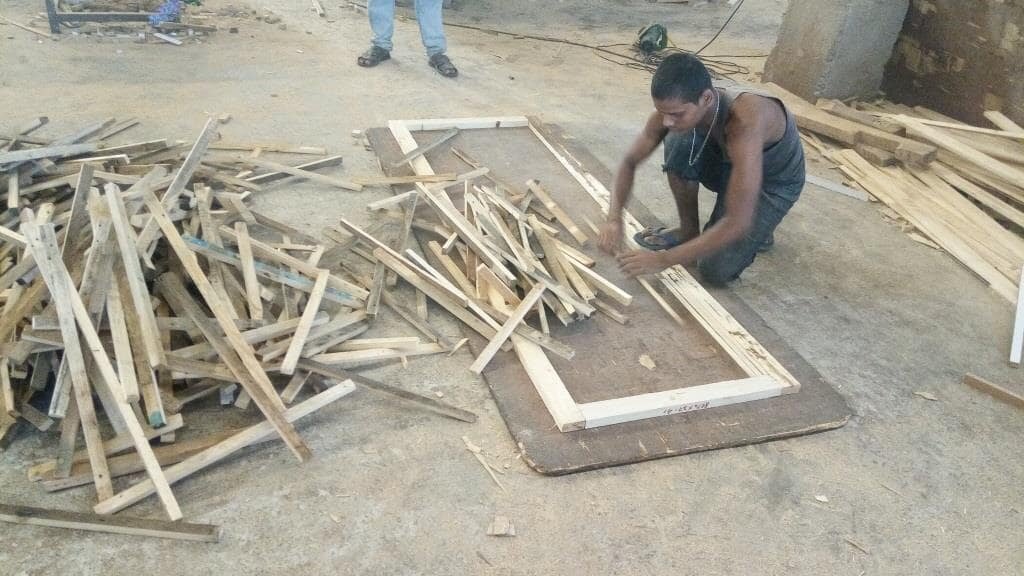
Photo showing completed blockboard filling inside of frame
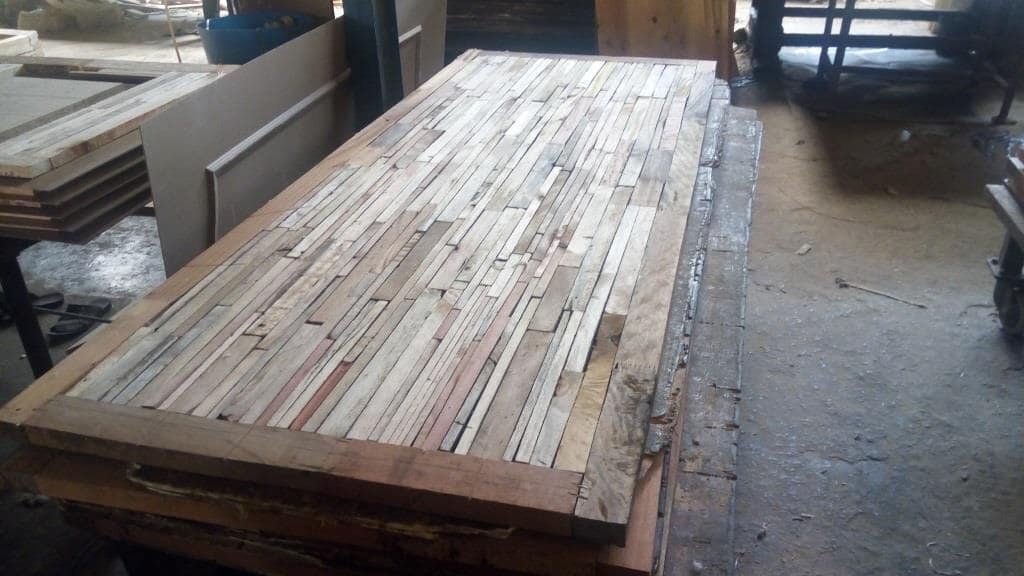
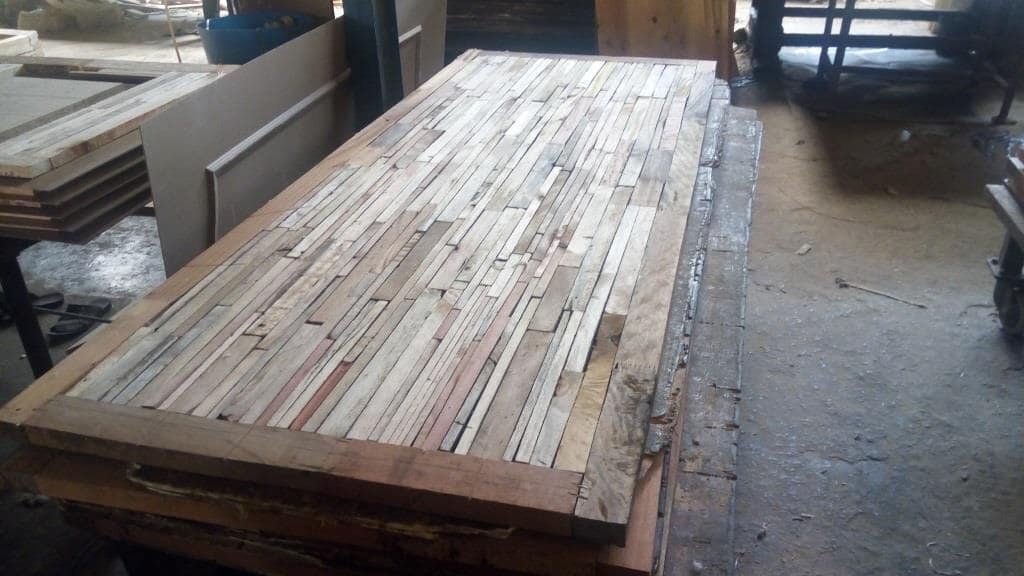
Before proceeding to how flush door shutters are made inside the factory, first take a look at the specifications given in IS 2202 Part 1 for making of it.
Stiles and rails should be of minimum 45 mm and shall not exceed by 75mm in width. Both should be of hard wood given in group 2A and group 2B.
The suitability of timber for stiles, rails and lipping normally based on screw holding properties of timber.
Blockboard – Wooden strip filled to make core of shutter shall be of single species and should not be more than 30mm in width. These strips may consist of pieces of small lengths placed end to end with the end joints staggered.
Moisture content in wood used for manufacturing door shutter shall not be more than 12%
In case of Particle board or medium density fiber (MDF) board core with blockboard, the width of blockboard constructed shall not be less than 150 mm from inner edge of the stile on either sides.
The Rails shall be made without any joint.
The Stile shall be made with maximum one finger or scarf type joint as per following details;
- Joint shall be located between 300 to 500mm from centerline of the door.
- The joints to both stiles should be located diagonally opposite to each other.
IS Code also state for Lock arrangement in shutters, it says;
Shutter shall be shop prepared for taking mortice locks or latches as may be agreed to. Shop preparing the door with mortice holes for lock fixing shall be done only when desire, suitable block of wood may be provided for fixing the hardware, in absence of specific requirement, the size of block shall be preferably corresponding to maximum size of lock covered in IS 2209.
All above are the basic requirements.
In India, Now days all solid core type flush door shutters are made up of scrap pine wood completely.
Pine is not a hard wood but still it is used for complete construction of shutter due to its cost effectiveness.
The pine scrap wood is dumped at factory via trucks, the pine wood received is generally 2 to 4 feet long.
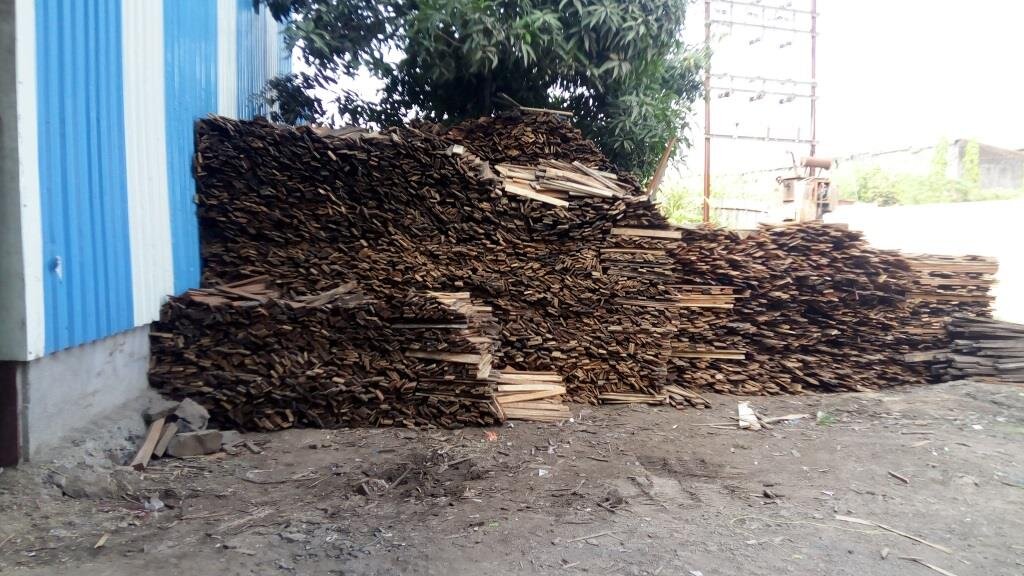
After receiving the wood, it is processed under the seasoning chamber to reduce its moisture content and make it below 12%. Generally, wood is made to complete dry condition in the seasoning chamber.
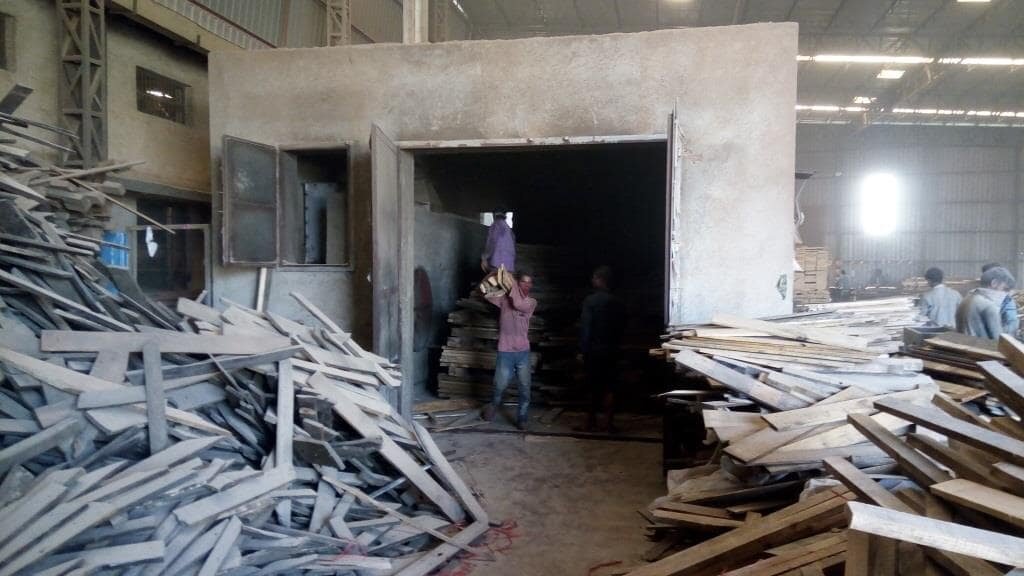
After removing the moisture to desired level, the pieces of pine wood then stacked outside to make it in sizes required. Wood tend to deformed in shape when the moisture level in wood changes and also it does get cracked after drying.
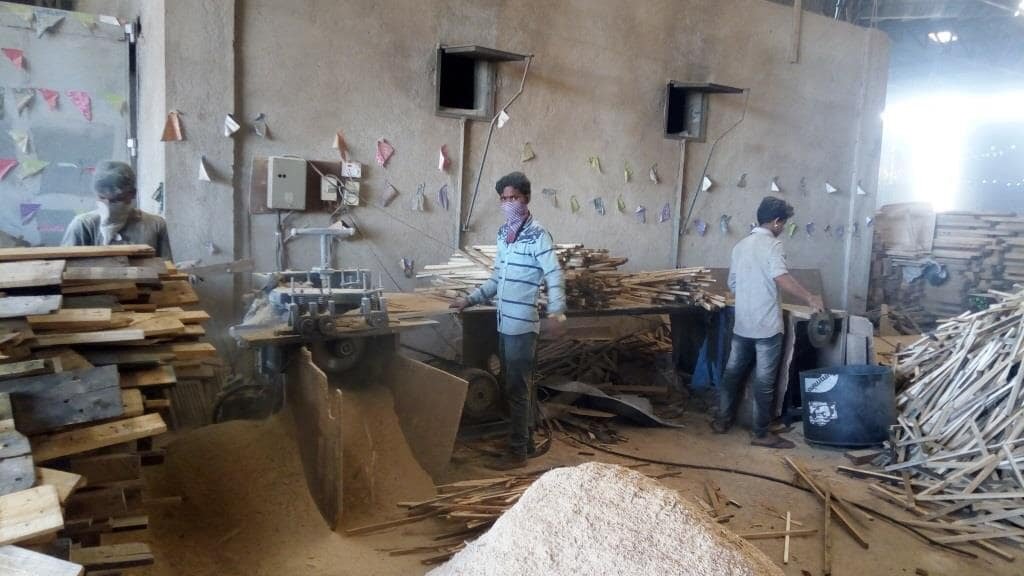
After sizing it to required level, it is stacked near machine and this is used for making blockboard and framing of door shutter.
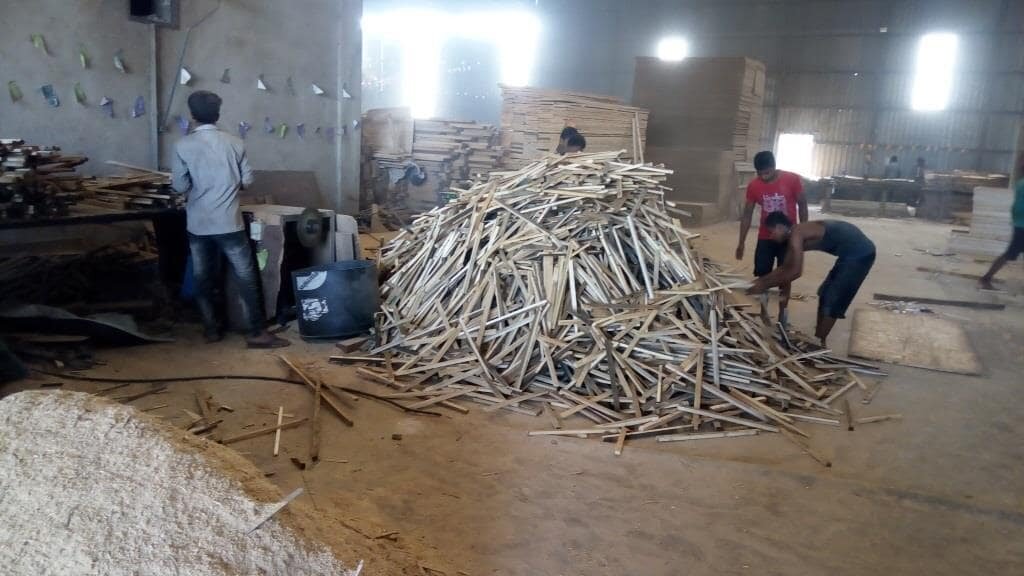
As the wood is scrape, it will be in size from 2 to 4 feet and height of the shutter is normally around 7 to 8 feet. Those pieces of wood then joined together by making finger joints.
Before making the stile and rails, the wood goes through the planner and finger joint making machine.
Below is the photo of planner which makes the wood in uniform thickness.
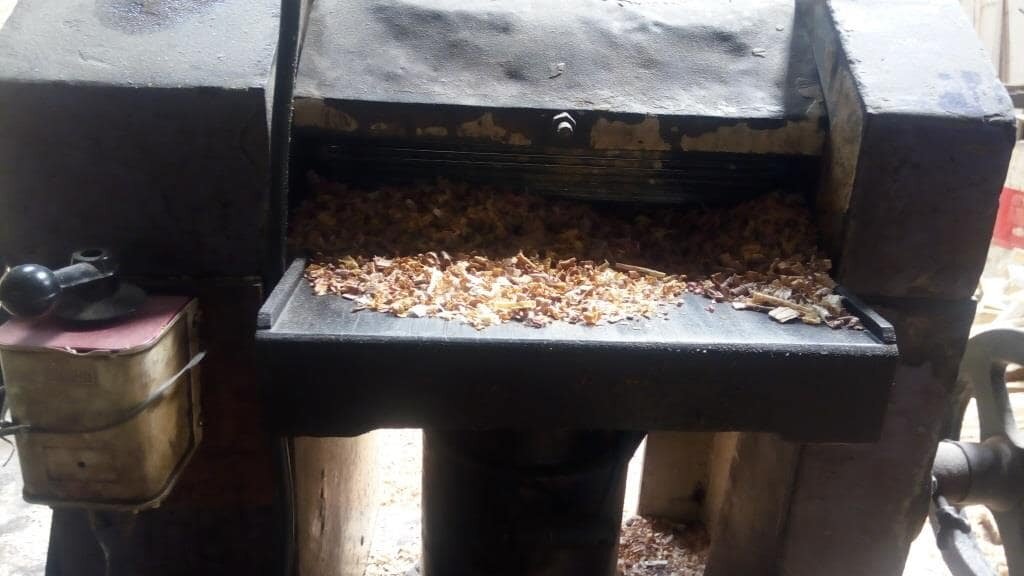
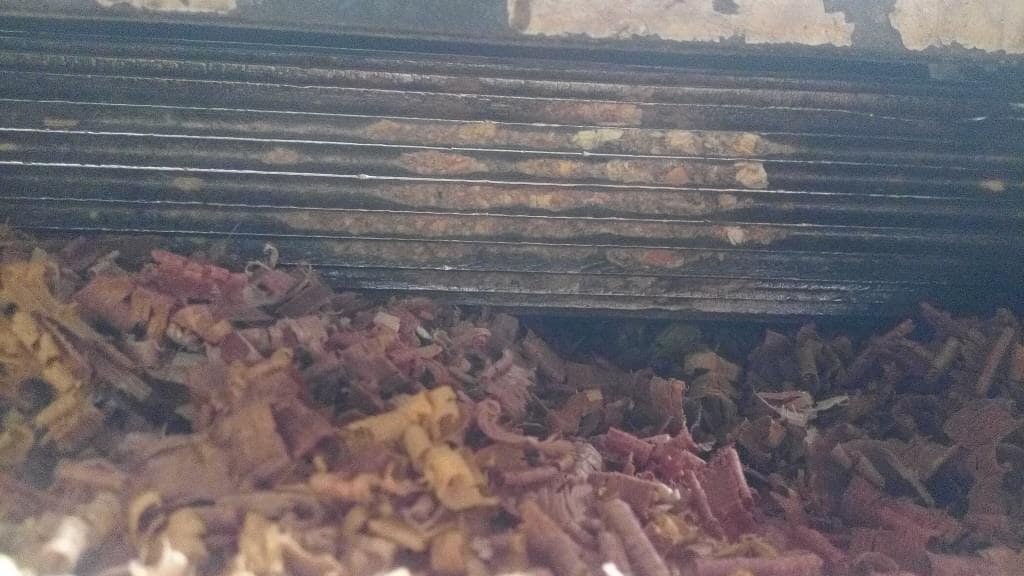
After this, finger joints are made on each piece of wood
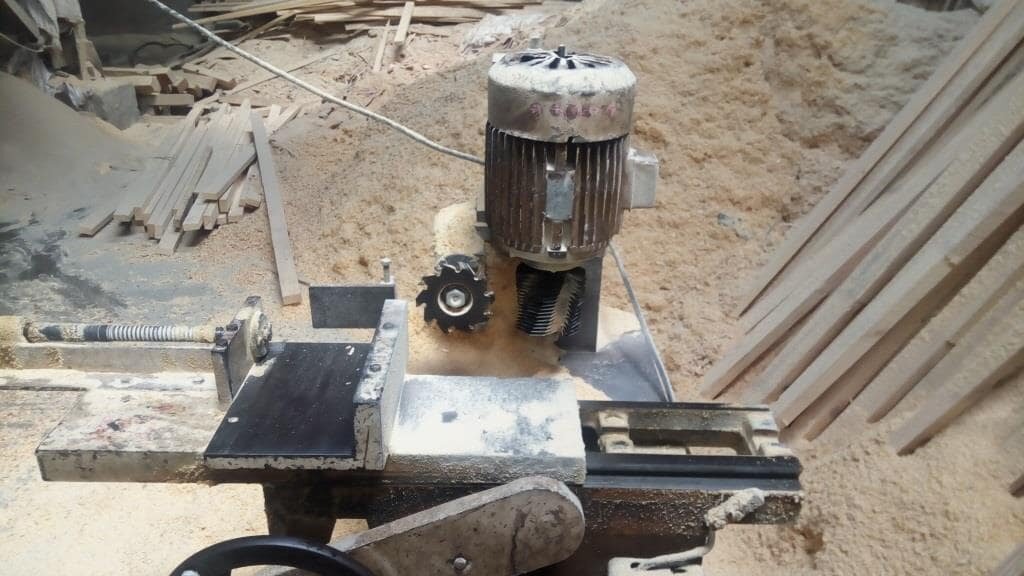
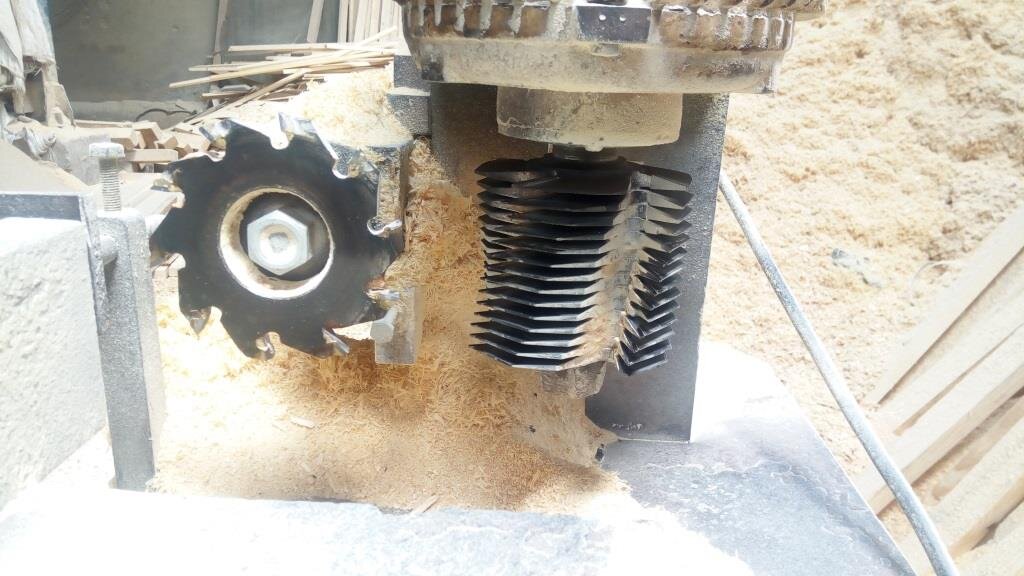
A wood just passed through the machine showing carving of finger joint on it
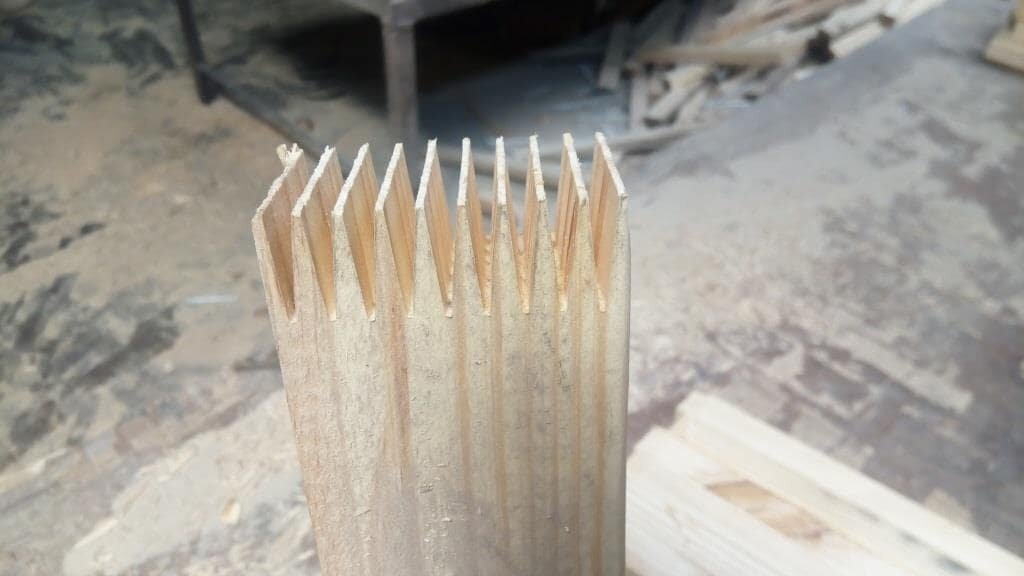
Those pieces of wood then joint together with high strength glue adhesive to make a long stile and rail on a steel frame structure where straightness of wood is ensured
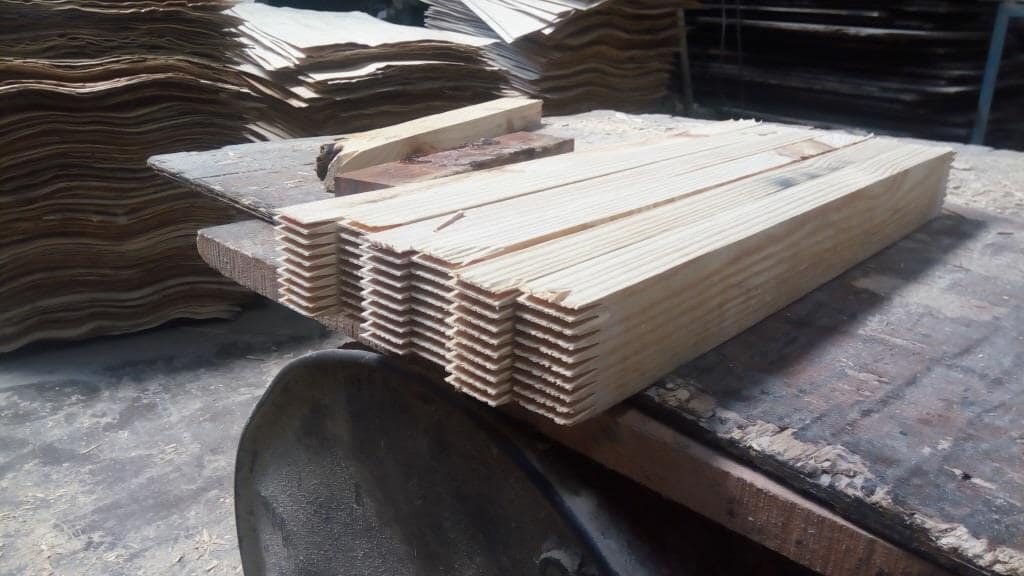
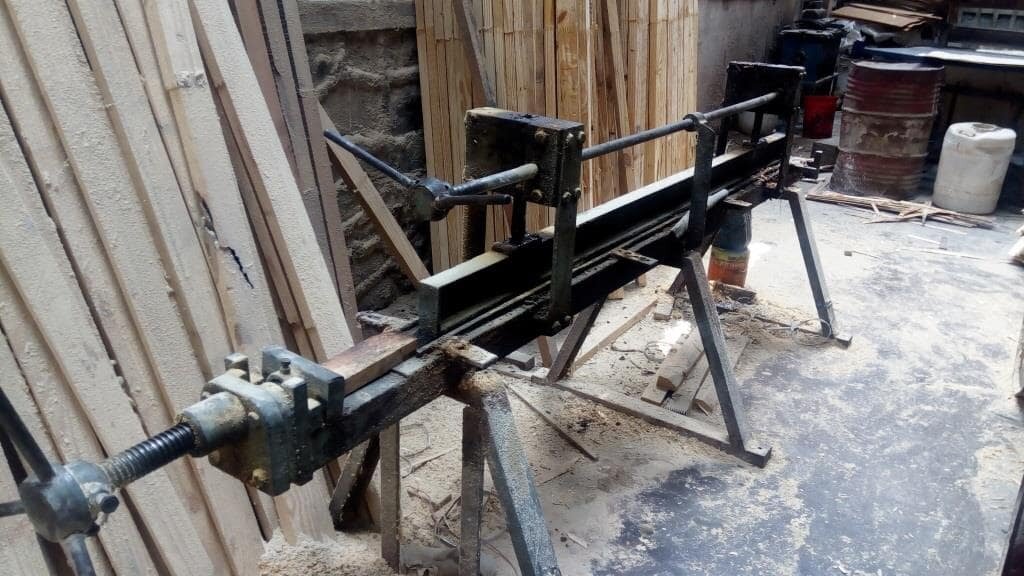
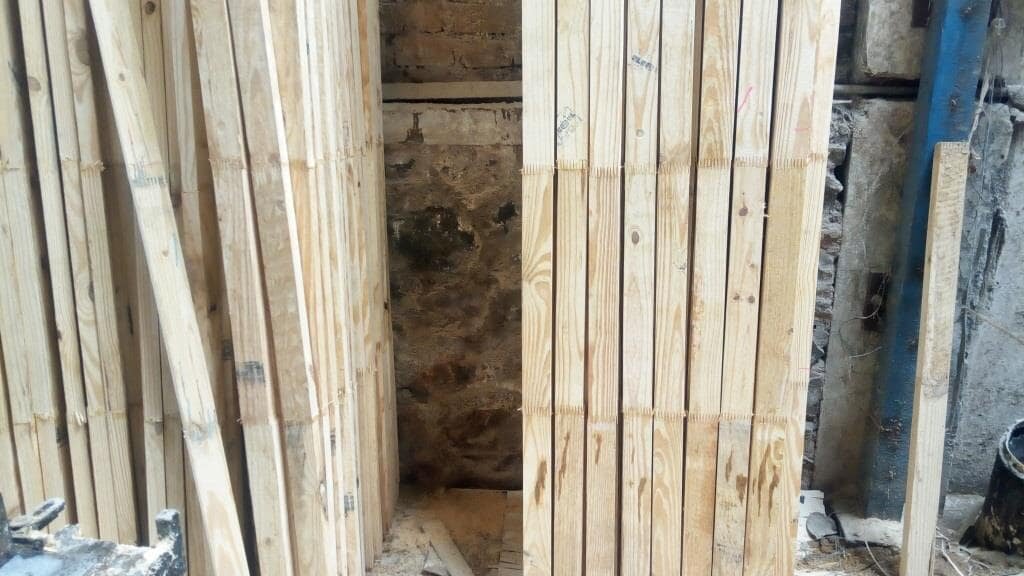
After construction of stiles and rails, a frame structure is made out of it of desired length and width. The right angles and dimensions of frame are checked at the time of making of it
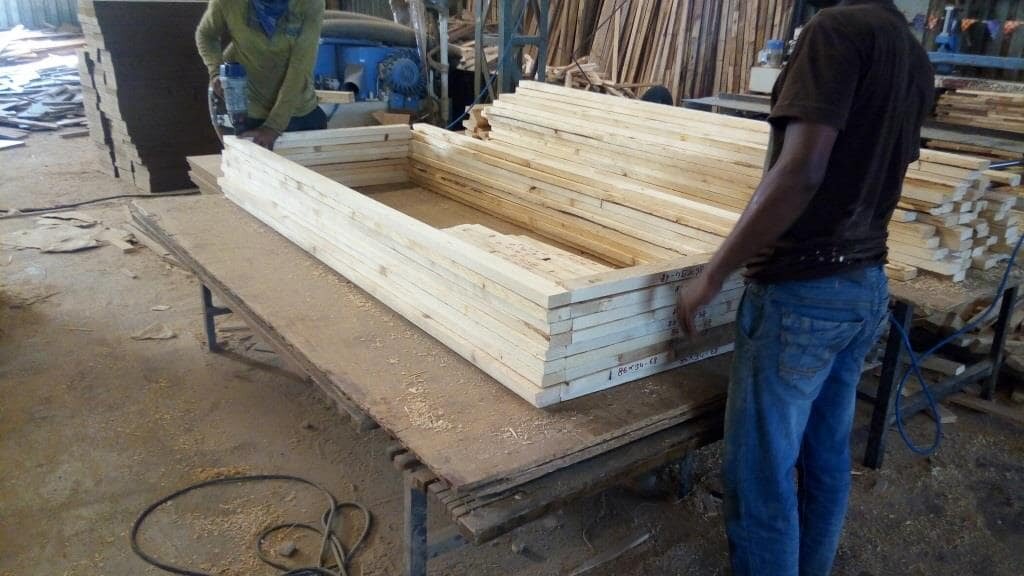
The jointing of the frame is done by using a stapler pins around 3 to 4 mm, at each joint 2 pins were installed using pneumatic stapler machine which works on the air pressure. Stapler pin only works on soft wood, in case of hard wood cotter pins need to be installed at each joint. Cotter pin lead to breakages in soft wood as it wont take much pressure or due to its softness.
Below is the phot of stapler pin
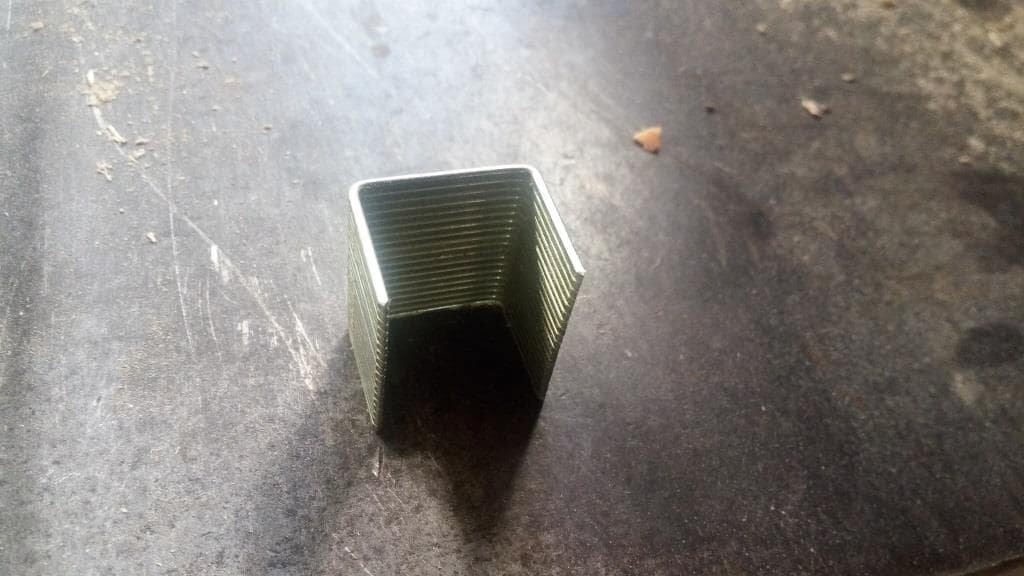
Below is the photo of pneumatic stapler
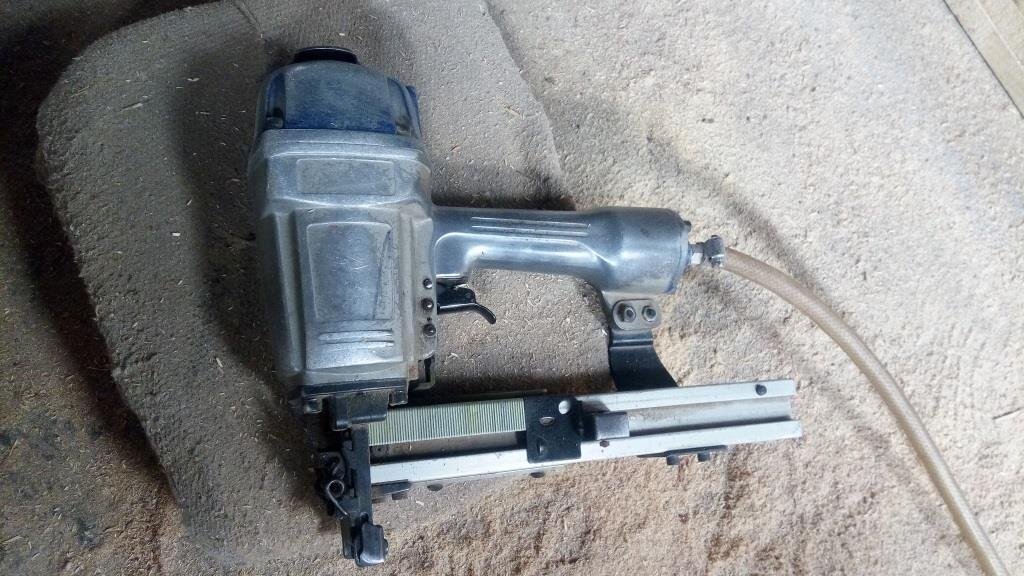
After making of frame, it is then placed on a levelled surface of plywood or metal sheet and as per the design, either blockboard or combination of blockboard and MDF board or complete MDF board is made inside of it base on the requirement given.
Below is the photo where blockboard is made inside the frame, blockboard is made using pine strips of not more than 30 cm in width. The workmen fits the stips inside the frame by ensuring joints of strips get staggered in installed pieces. After filling of blocks in it, the small pieces of wood inserted at 2 to 3 places to make the fill tighter in it.
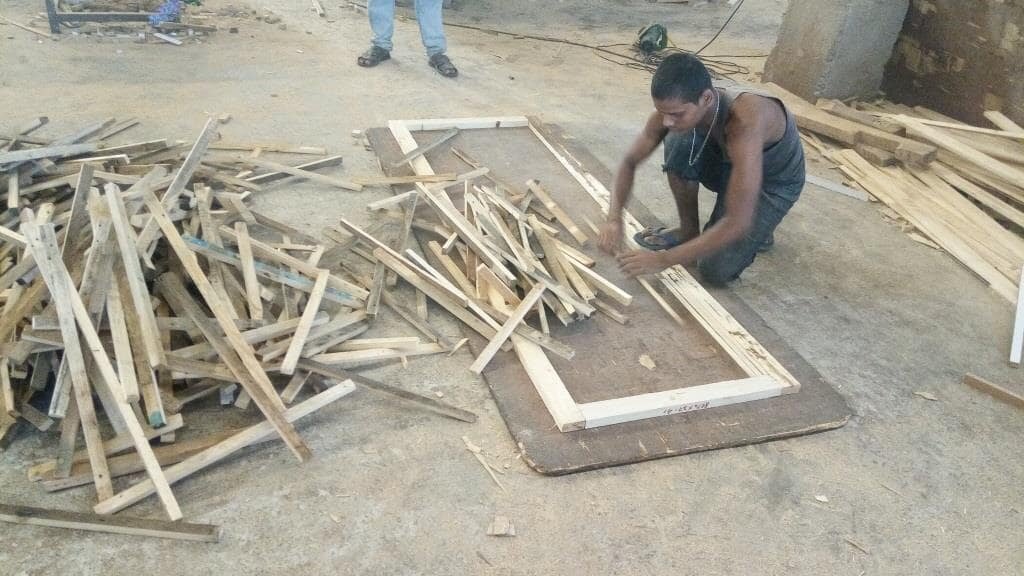
Photo showing completed blockboard filling inside of frame
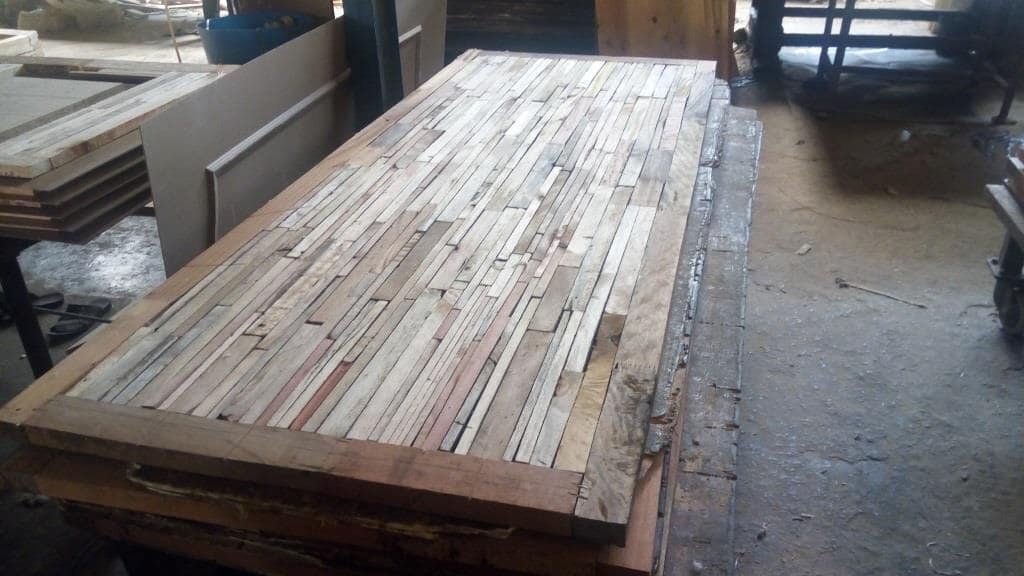