Ceramic and Vitrified Tile Manufacturing Process
What is Ceramic tiles or vitrified tiles
It’s basically a product of clay same like brick but made carefully with high precision to ensure the all tiles have the same dimensional as well as strength and aesthetic properties in it.
What make it different from clay bricks and how.
Clay bricks are made without removing the impurities in it and ensuring same grain sizes in it. Also they are fired in very uncontrolled way which makes some bricks over-burnt and some bricks under-burnt and have no equipment to ensure the perfectness of each brick.
So how the Tiles are manufactured in control environment
The clay use in manufacturing of tiles is checked for its clay properties and other chemical requirements. Mostly here in India clay use for manufacturing of tile comes from Gujarat and Rajastan. It’s in very raw form just like excavated earth is loaded in wagons and transported to factory.
Clay is also imported from other Countries to achieve more strength and plasticity during manufacturing and it is blended with the other clays.
In the process of manufacturing of tile first the raw clay is loaded into the hoppers and blended with minerals in batch mixer homogeneously.
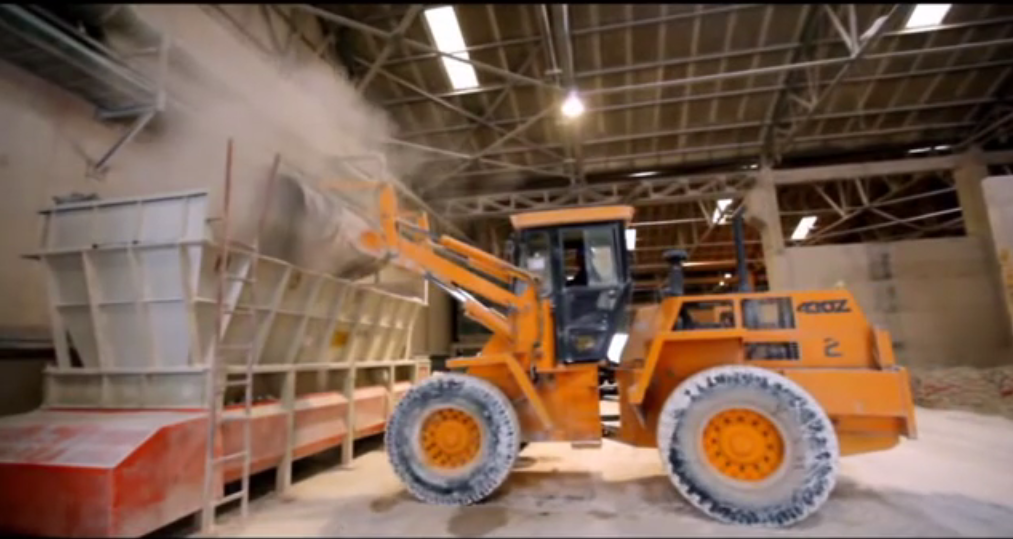
Those clay and minerals are sent via conveyor to a batch mixer to mix in proportion as specified by manufacturer to achieve the desired properties.
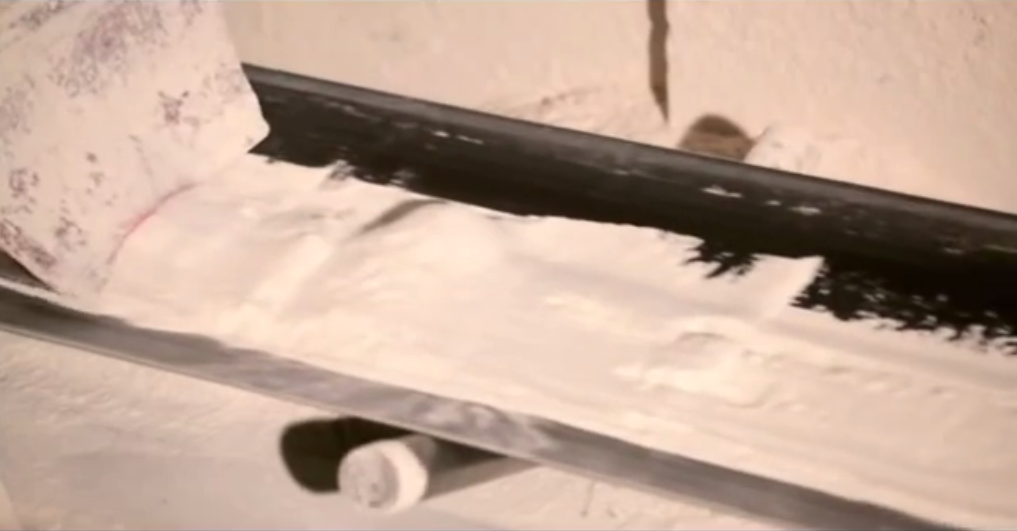
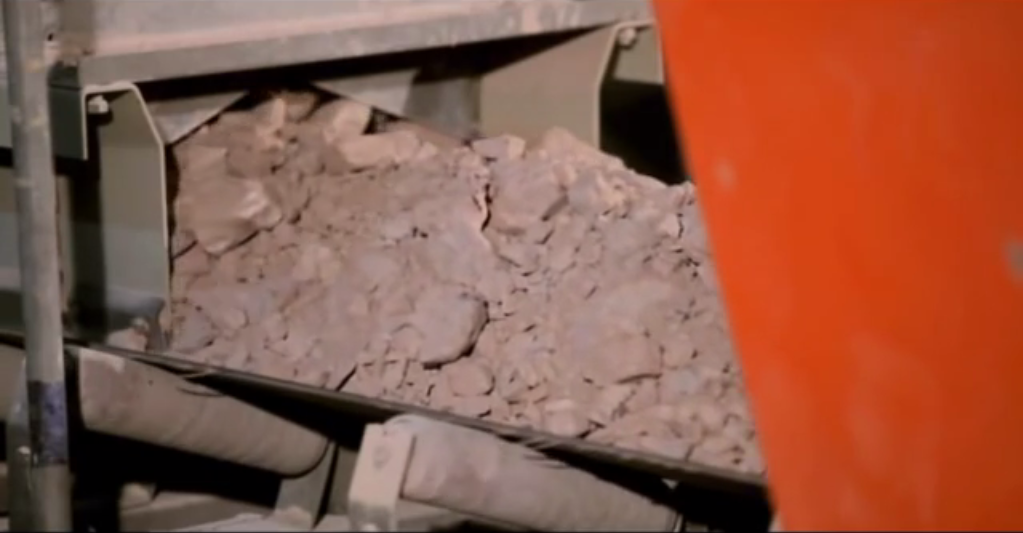
Then the blended mixture is sent to a ball mill and around 33% water by weight is added into it.
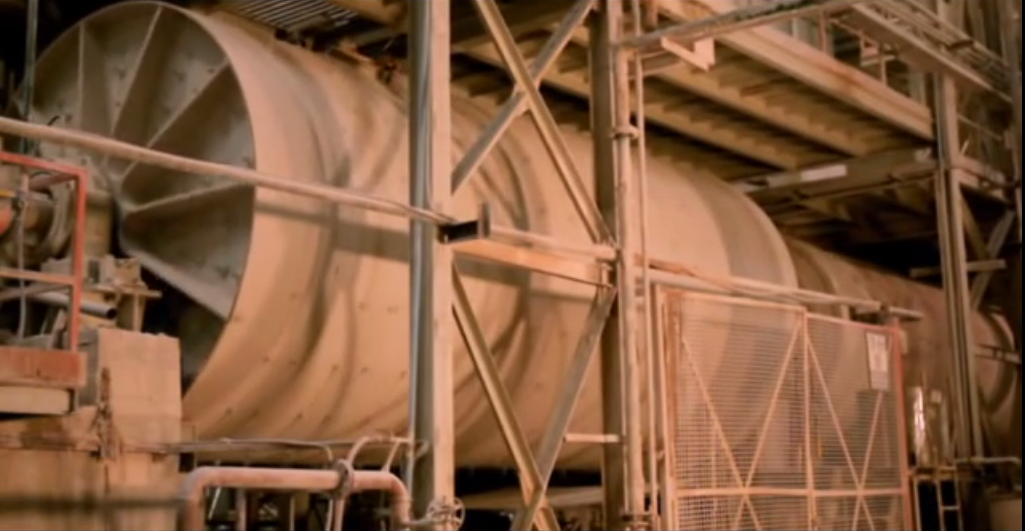
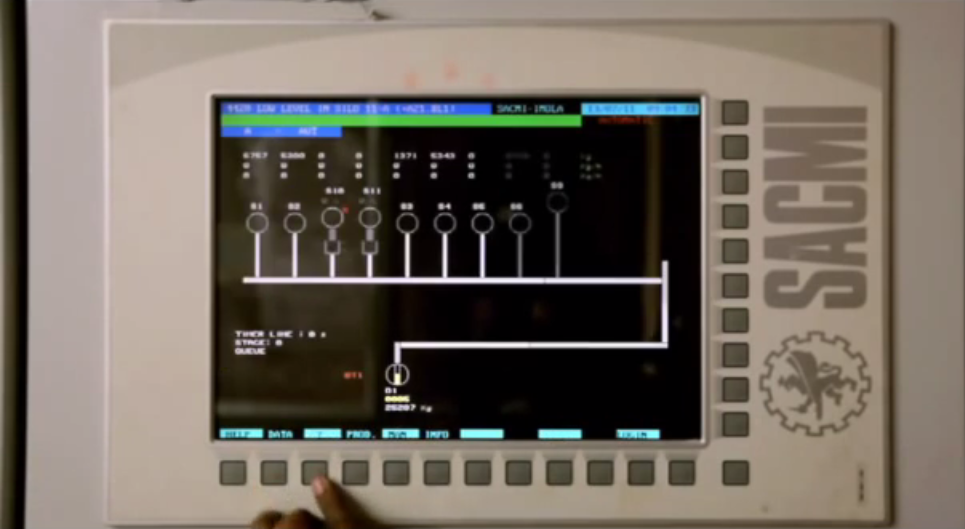
Ball mills content giant alumina balls which crush the clay into a finest slurry through a rotating action of ball mill and gravity force acting on alumina balls. Below is animated photo of milling action.
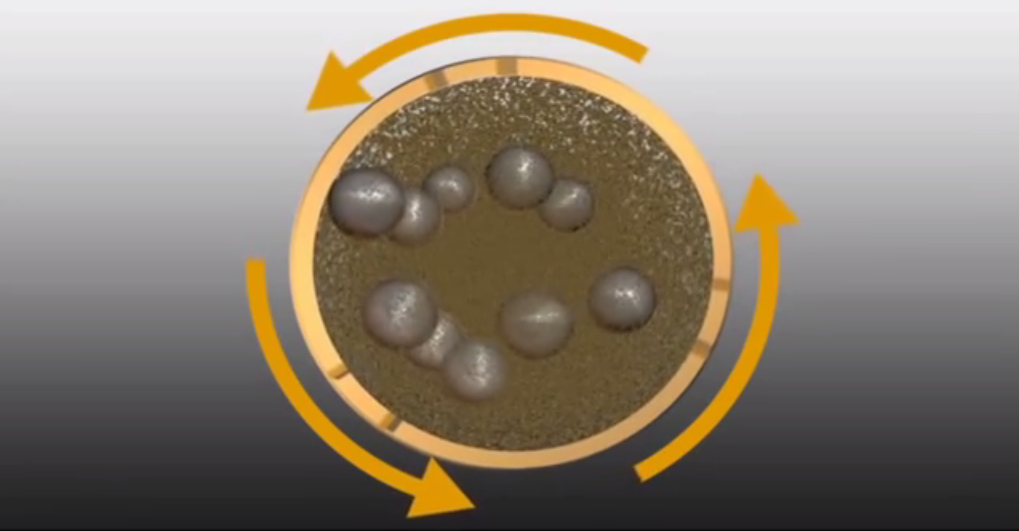
The milling action creates a homogeneous slurry which is taken out from ball mill and screened to remove the uncrushed clay or stones.
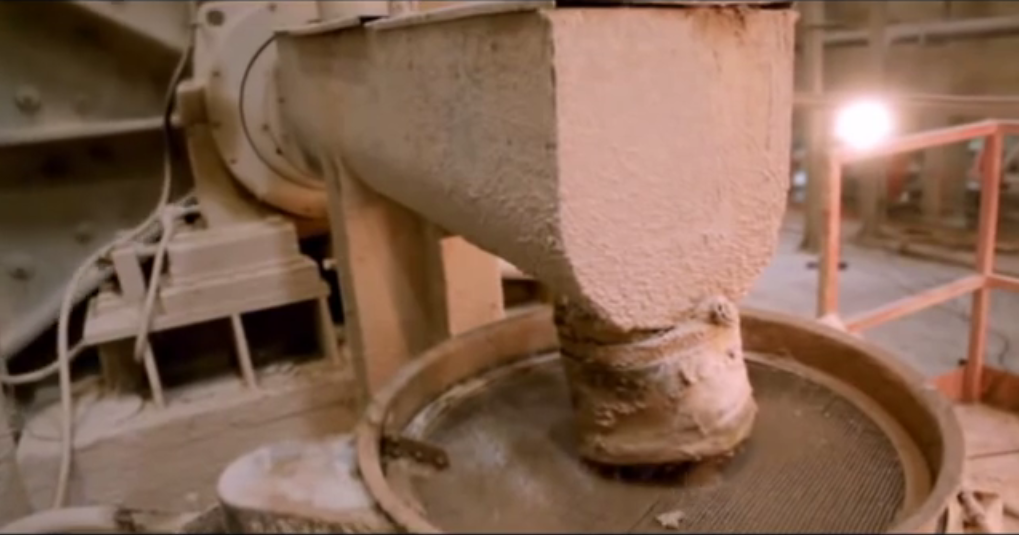
After passing through this hopper the slurry is further moved to a vibrating screens which have the mesh size of 75 microns. The vibrating actions ease out the process of making a fine slurry to pass through it and the oversized material to go out.
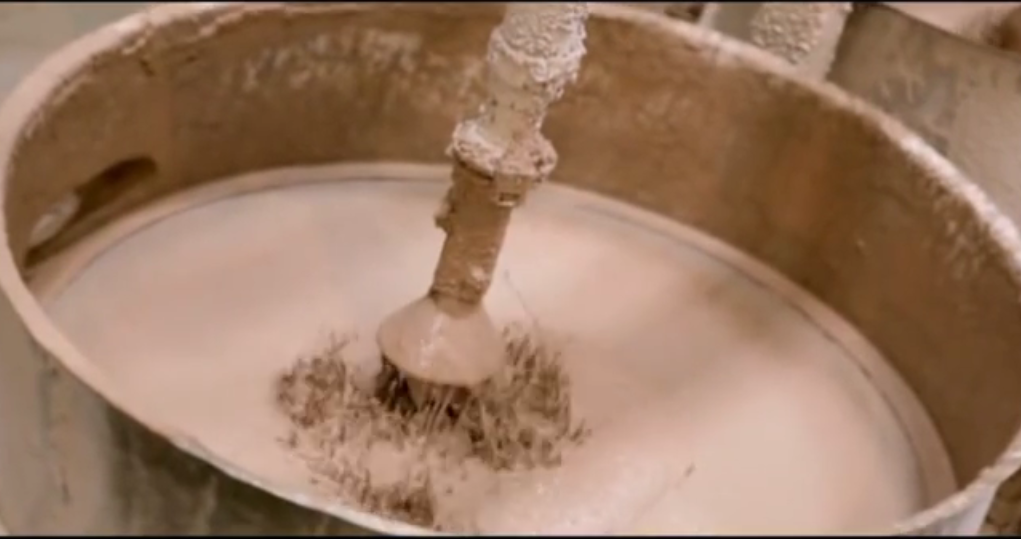
The passed material then go through the channel where magnetic purification of slurry is done.
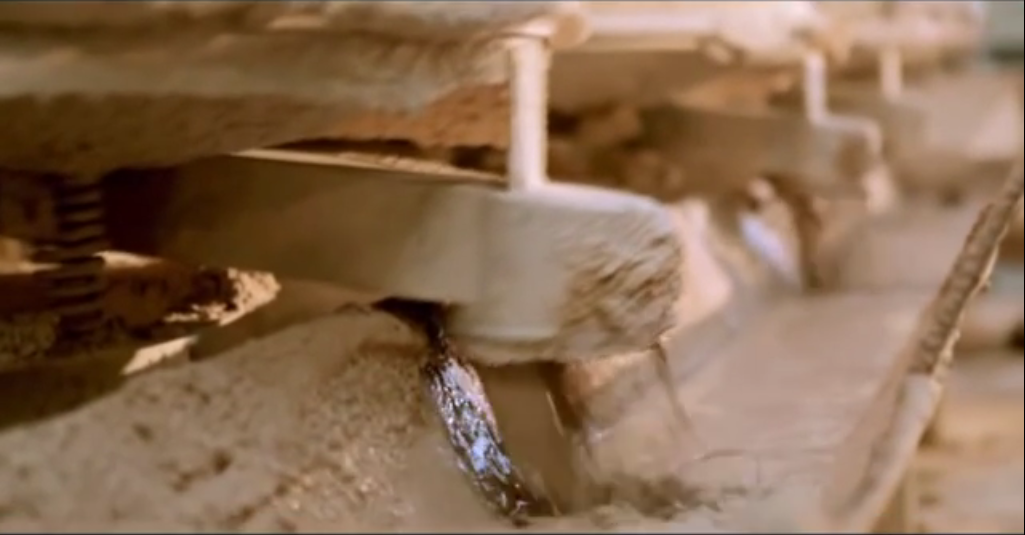
All the material which does not pass through, is again sent back to a ball mill and re grinded to finer size (not a single stone is wasted at tile manufacturing unit, even a waste from backed tile which is cut and grinded for correctness is also re-used for manufacturing)
After passing the screen and magnetic purification, slurry is then pumped with high pressure pump to a silo through a nozzle which have small holes in it.
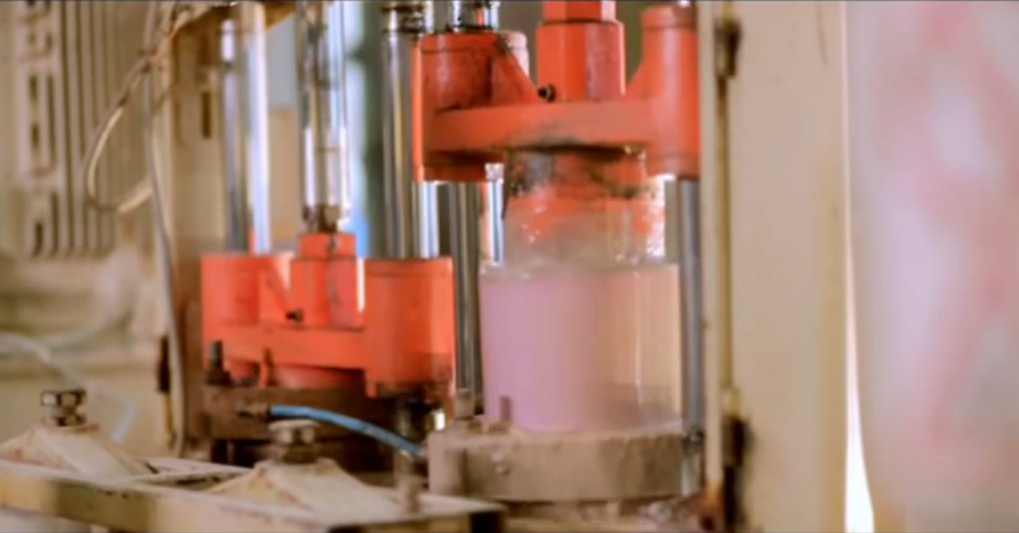
The spraying of slurry into a silo is done along with passing hot air into it. Spraying action and hot air pass makes the slurry to reduce its moisture from 33 to around 5 to 6 % which forms a finest granules of clay which are slightly moist. After formation of granules they are further moved to pressing machine which shape the tile body. The hot air pass and spraying of clay is done in control way to ensure the correct sizes of grains.
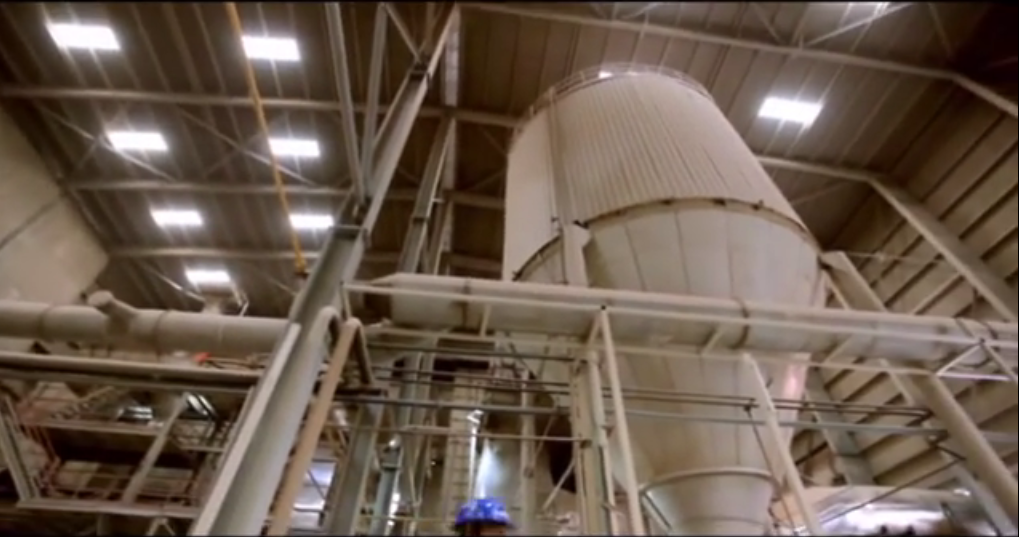
The finest clay powder is then sent to a pressing machine via conveyor.
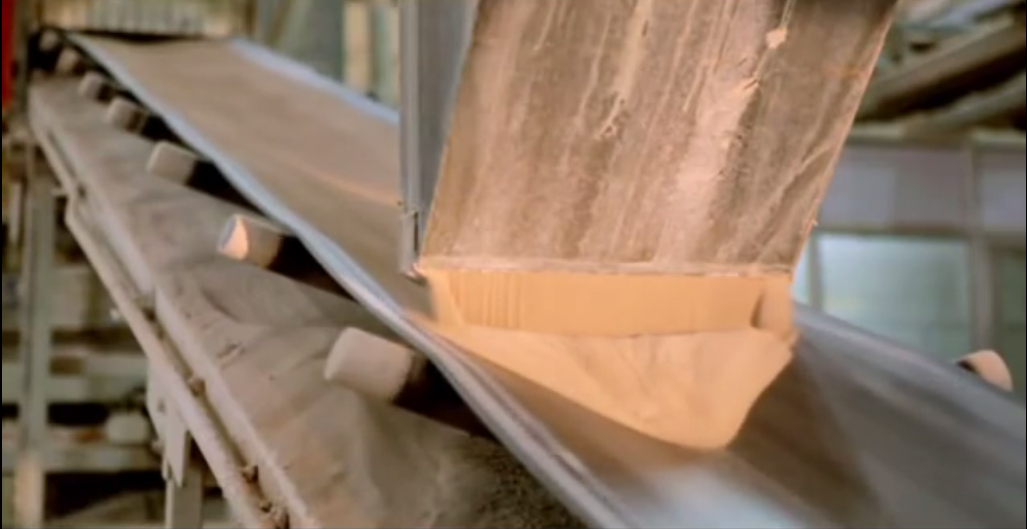
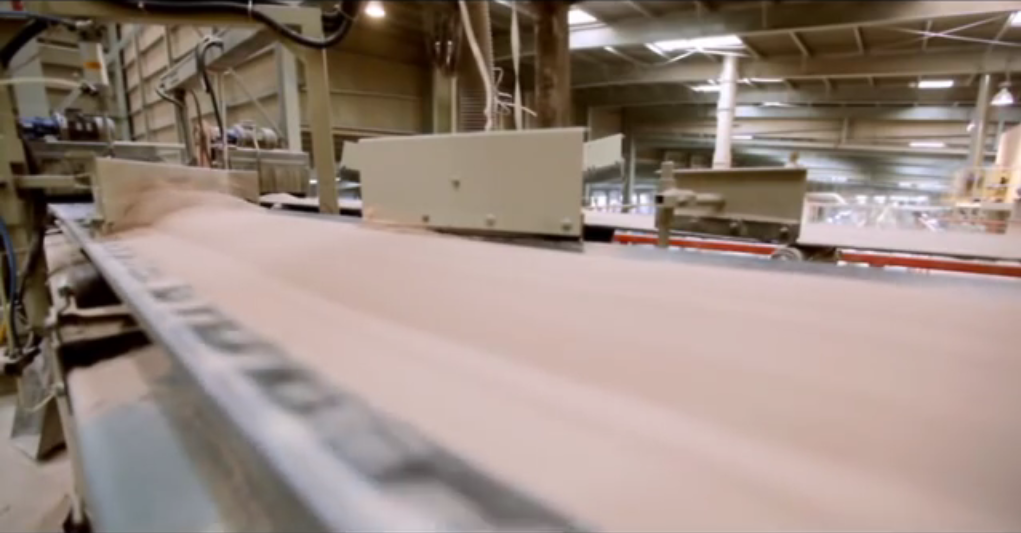
At the pressing machine the properties of tile which to be manufactured are decided, Ceramic tiles are made by pressing powder into the mould at low pressure and vitrified tiles are made by pressing powder into mould at slightly high pressure.
The classification of the any tile is based on its water absorption property which comes from this process. Pressing at high pressure ensure the extra amount of powder to be pressed in same volume of tile creating lesser voids in base tiles which corresponds to low water absorption and vice a versa.
For ceramic tiles the pressing of powder is done at 450 bars of pressure and for vitrified tiles pressing is done at 550 bars of pressure
At pressing machine, we can mould any size tile by providing specification and making arrangements of mould by simply programming it with all data.
Once the command is given, a fully automatic pressing machine fills the mould with moist powder of clay and presses it to required pressure and sends it forward through roller conveyor for further processing machine.
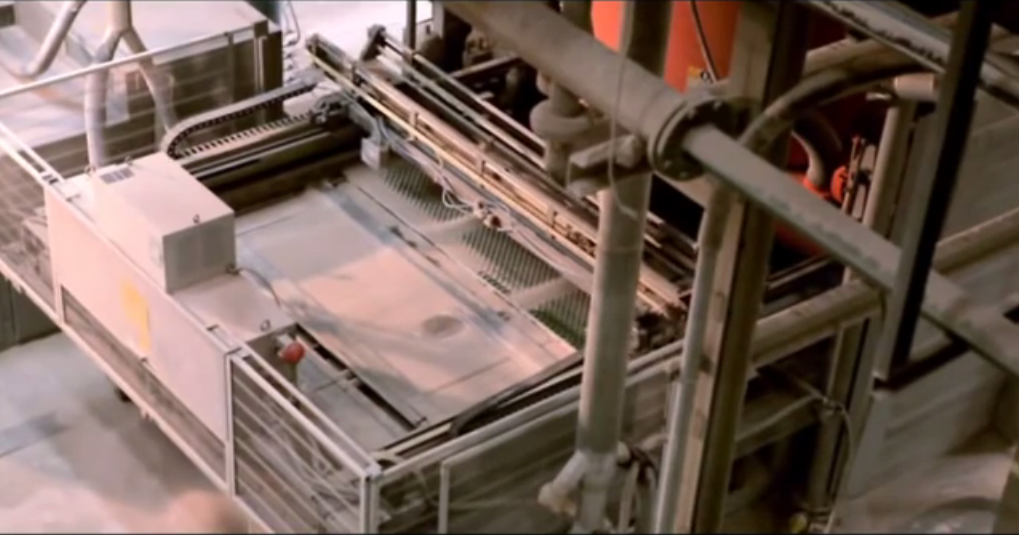
The push tile further here is called as green tile or biscuit.
We can have any shape in the back of tile and can be given in the mould, the top of the tile is plain or have designs on it (rustic tiles) to give the feeling of natural stone.
Rustic finish tiles are slightly costlier as the surface is not plain and the process of its topping do add additional costs but it gives a natural rock filling on top of it.
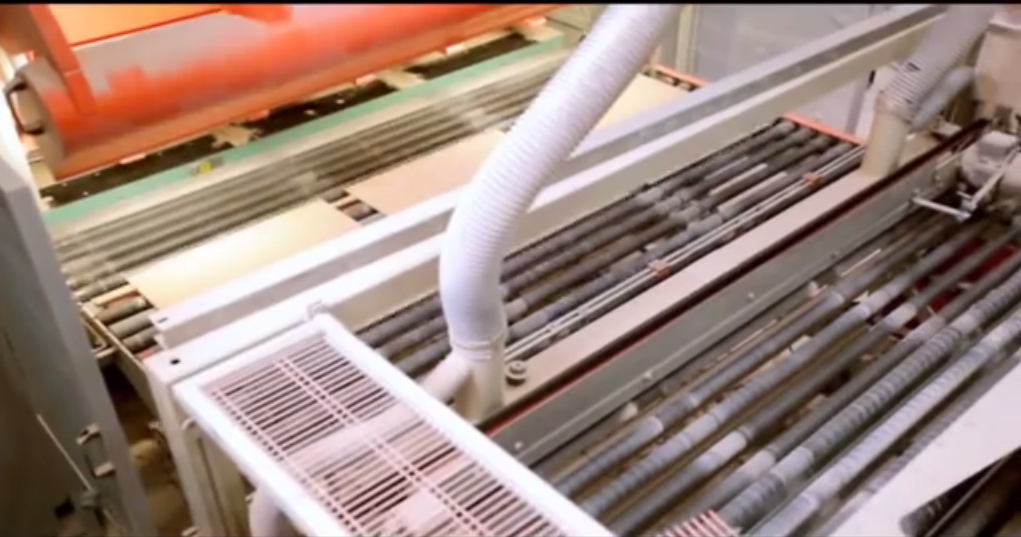
Must know – the size of the moulded tiles is always more than that of required size, generally they are made 15mm + on higher size coz during pressing, there is a chance that tile ends may lift upwards and in further processes may get some defects which can be nullify by cutting it after topping / printing.
The color of biscuit or green tile or the back of tile which is not visible, depends on the properties of the clay and mostly they are brownish or whitish.
So next time when you get two batches of tiles and if there back color varies, then either that tiles are not manufacture at same factory or there is change in source of clay.
The green tiles then further goes from a drier which removes it moisture content completely.

Once the tiles are reached on other end of drier, they are completely dry and does not have any moisture in it and ready for further processing.
The green tiles are tested for its flexure strength to ensure the quality of batch.
Dried tiles then coated with engobe, glaze and sent forward for printing. It can be either printed with rotary drum or digital printing machine.
Here onwards for each step of coating tile is first coated with adhesive and then air dried and each coating is done.
The green tile is then goes through a conveyor where adhesive is sprayed on it and air dried with fan.
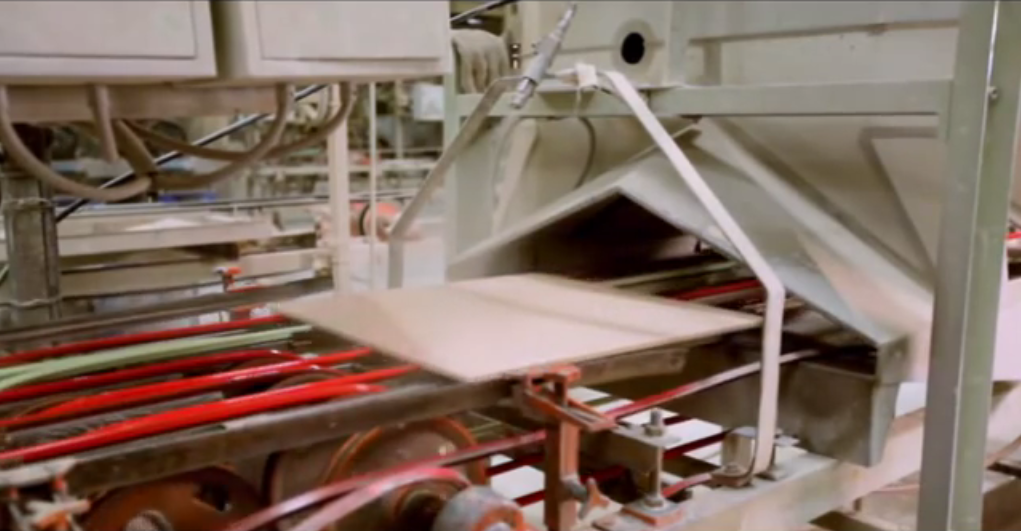
After this the engobe and glaze is applied on the tile surface.
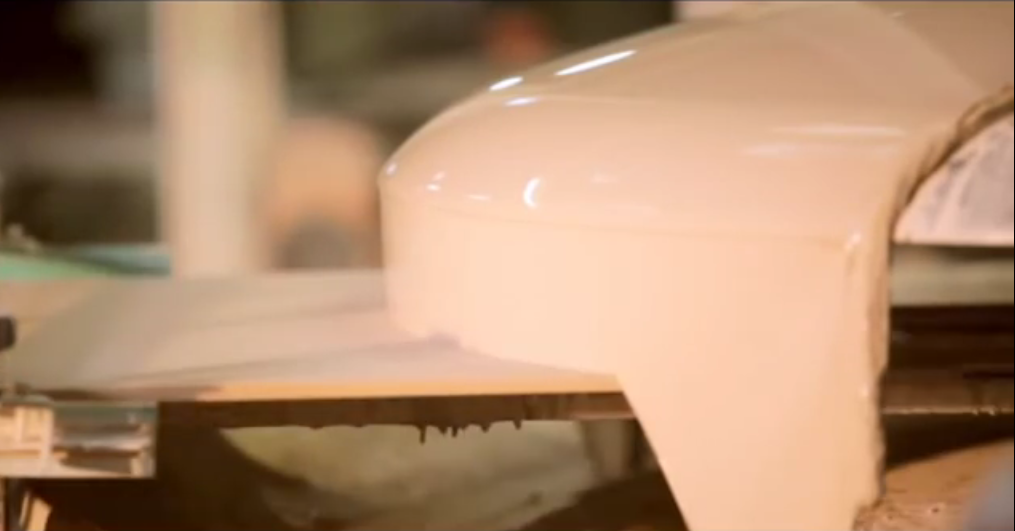
Engobe is the main layer on the tile surface which ensure no leakages from top to back of tile or from back of tile to the top surface (it’s just like a waterproofing coat). When you see a wet patches on tile surface then it’s clear indication of improper engobe application on it.
After engobe and glaze application tile is further moved to a printing assembly, it might be a roto type drum printer which gives color in 4 or more layer with adhesive application and drying before printing each layer.
In roto drum printer a color minerals are flowing through drums and when tile passes from the below of drum surface a layer of minerals is printed on it (just like how we apply paint on wall surface with roller brush)
Below photo shows assembly of 4 roto drum printer.
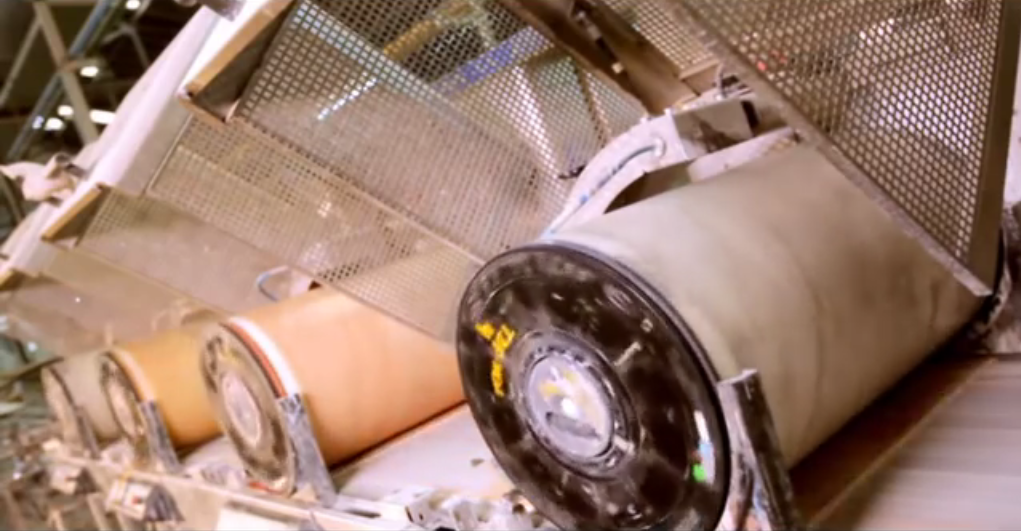
There are two technologies to print the design on tile surface
Roto Drum printer – As it’s a rotating drum which impress the color on tile surface, we can’t make a same design print on each tile surface and all tiles have different combination of surface texture (more likely they looks same), with this technology we cannot have fancy or more designs printed on it. This is use to give finish on the flat or rustic surface tiles.
Digital printing – In digital printing we can mimic almost any style, color combination and any type of surface finish look (we can make it as to look like wood, aluminium etc). After application of englobe the tiles are sent through a giant digital printer where the program automatically prints the design on each tile surface as per the design, with this technology we can print anything on tile surface, we can make a your photo printed on tile or printed in parts on tile which makes combination of 12 tiles to show what is the photo.
After completion of printing on tile surface, the automatic laser guided robots stack them and move to a kiln where heating of tiles is done.
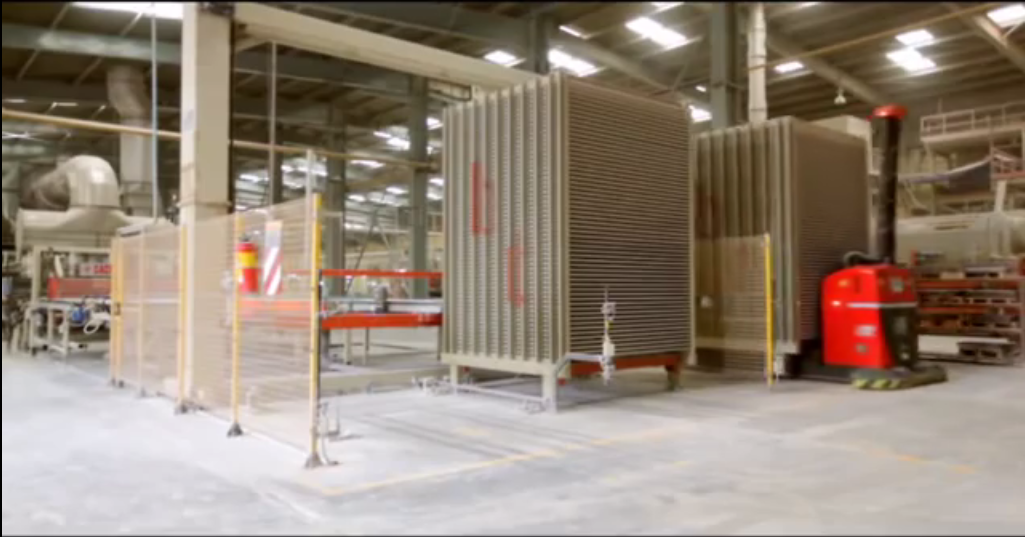
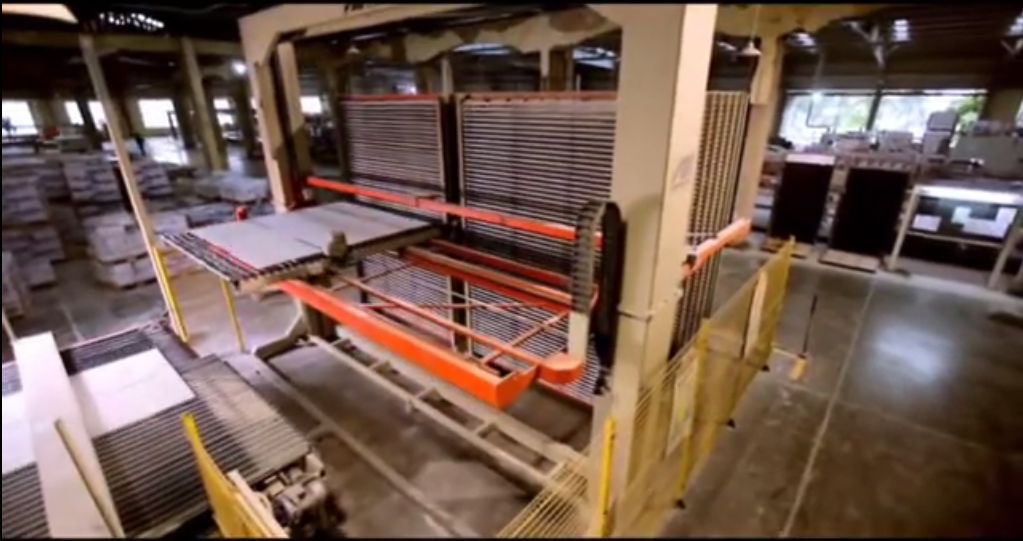
What is Ceramic tiles or vitrified tiles
It’s basically a product of clay same like brick but made carefully with high precision to ensure the all tiles have the same dimensional as well as strength and aesthetic properties in it.
What make it different from clay bricks and how.
Clay bricks are made without removing the impurities in it and ensuring same grain sizes in it. Also they are fired in very uncontrolled way which makes some bricks over-burnt and some bricks under-burnt and have no equipment to ensure the perfectness of each brick.
So how the Tiles are manufactured in control environment
The clay use in manufacturing of tiles is checked for its clay properties and other chemical requirements. Mostly here in India clay use for manufacturing of tile comes from Gujarat and Rajastan. It’s in very raw form just like excavated earth is loaded in wagons and transported to factory.
Clay is also imported from other Countries to achieve more strength and plasticity during manufacturing and it is blended with the other clays.
In the process of manufacturing of tile first the raw clay is loaded into the hoppers and blended with minerals in batch mixer homogeneously.
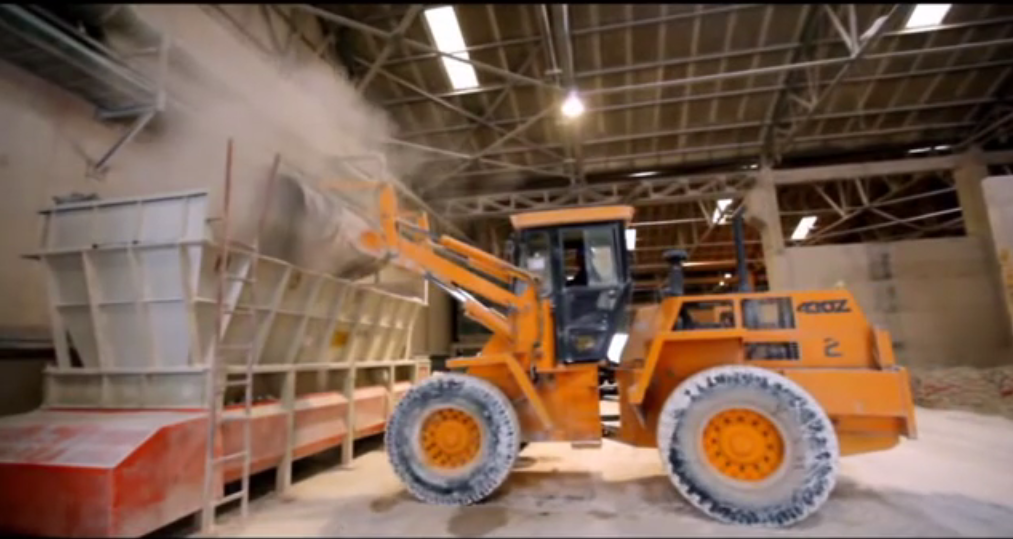
Those clay and minerals are sent via conveyor to a batch mixer to mix in proportion as specified by manufacturer to achieve the desired properties.
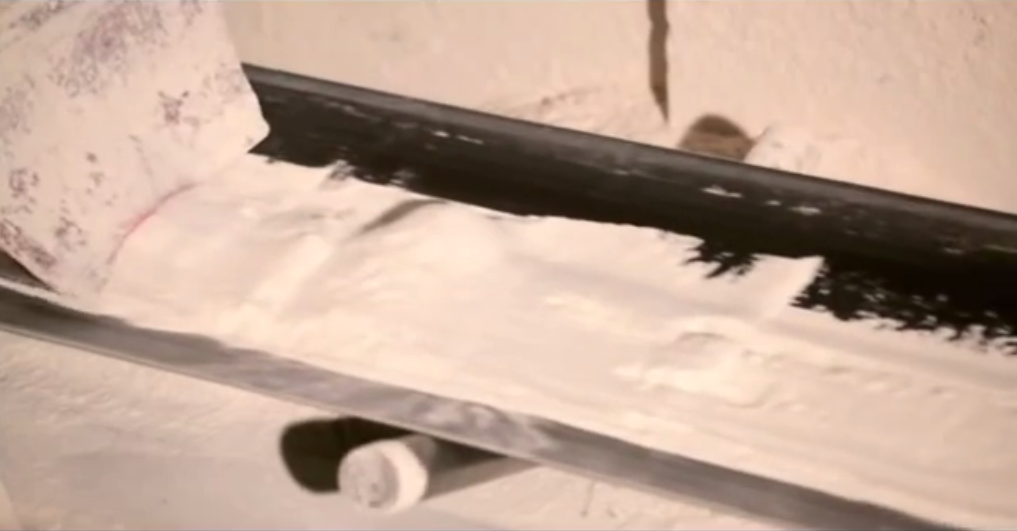
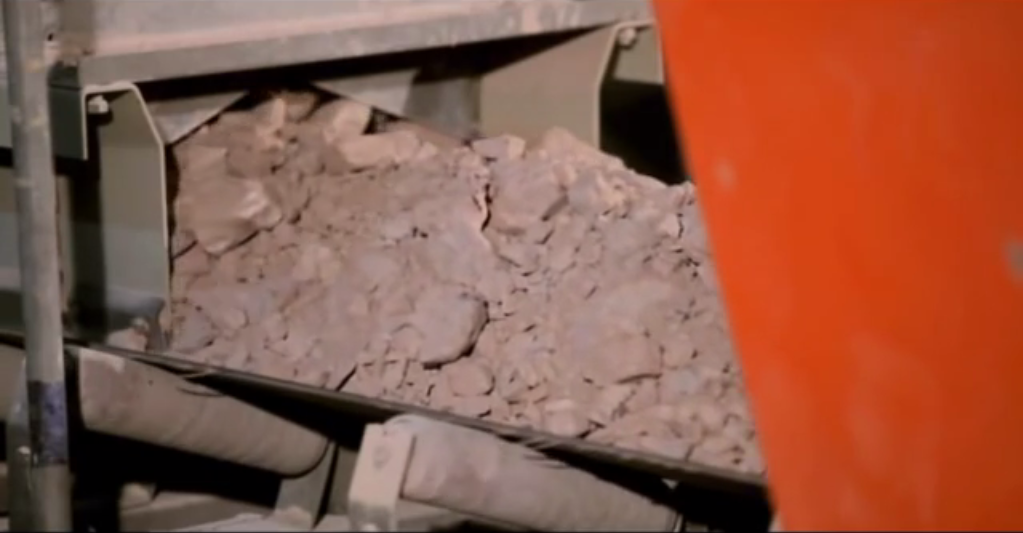
Then the blended mixture is sent to a ball mill and around 33% water by weight is added into it.
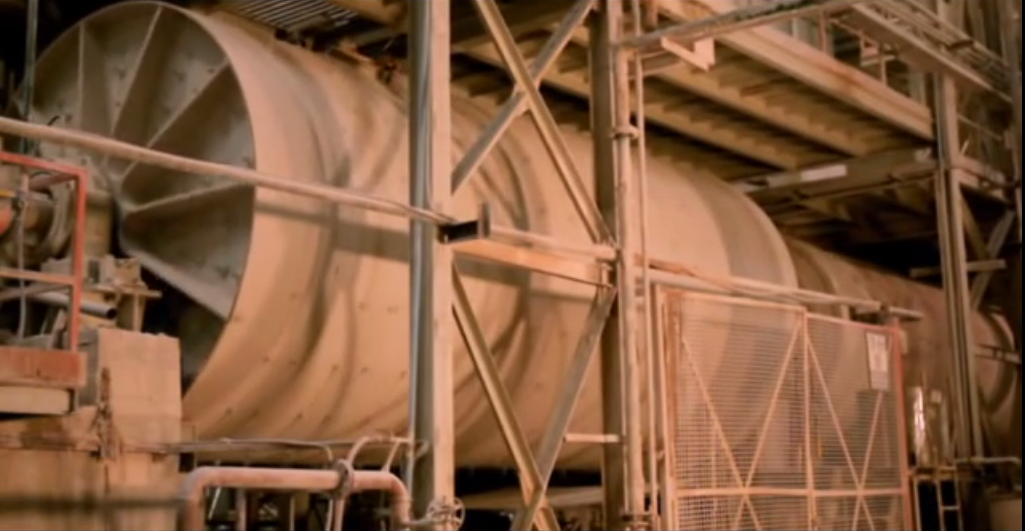
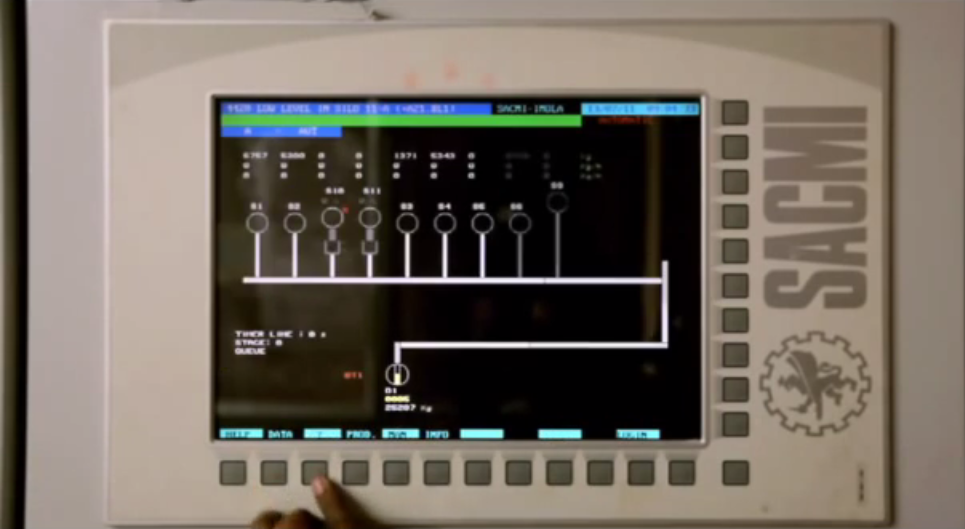
Ball mills content giant alumina balls which crush the clay into a finest slurry through a rotating action of ball mill and gravity force acting on alumina balls. Below is animated photo of milling action.
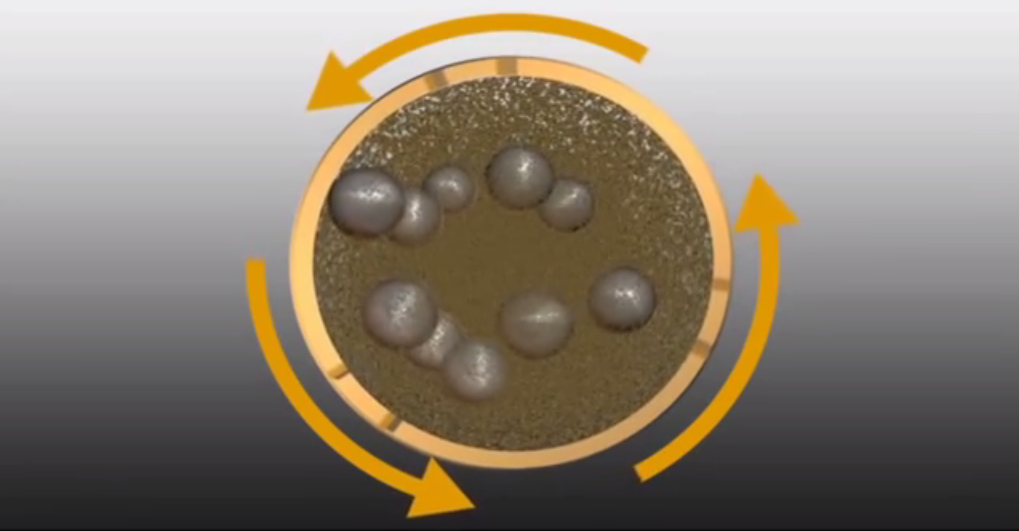
The milling action creates a homogeneous slurry which is taken out from ball mill and screened to remove the uncrushed clay or stones.
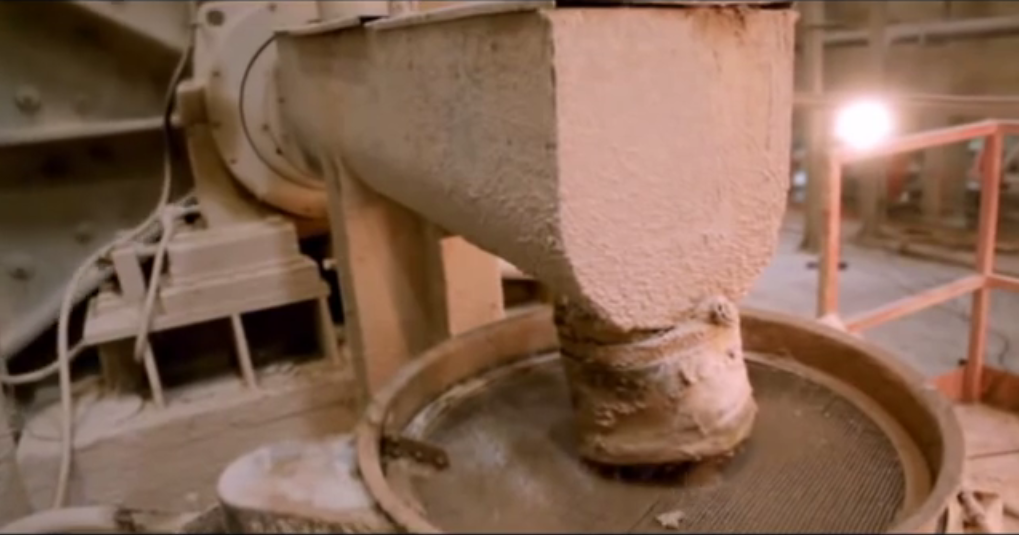
After passing through this hopper the slurry is further moved to a vibrating screens which have the mesh size of 75 microns. The vibrating actions ease out the process of making a fine slurry to pass through it and the oversized material to go out.
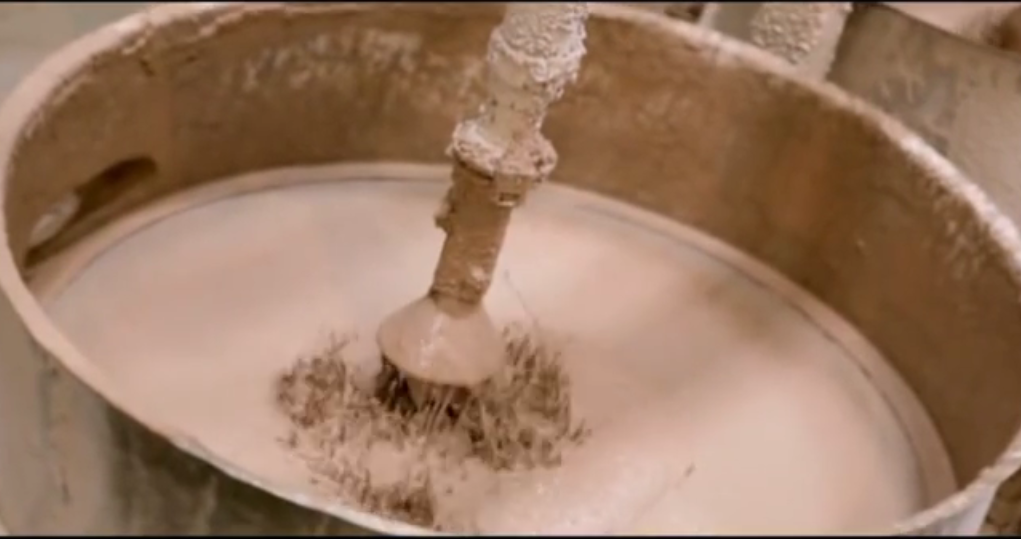
The passed material then go through the channel where magnetic purification of slurry is done.
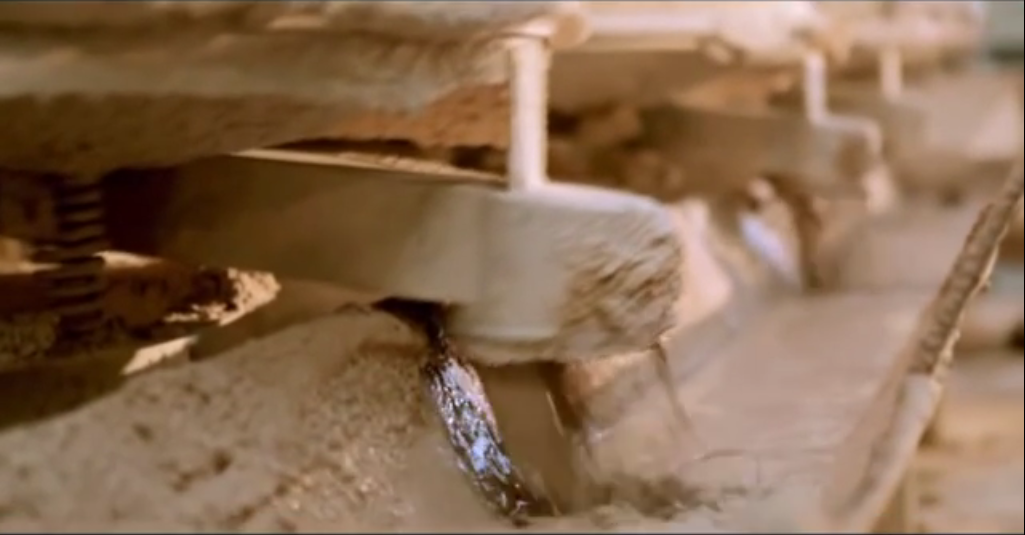
All the material which does not pass through, is again sent back to a ball mill and re grinded to finer size (not a single stone is wasted at tile manufacturing unit, even a waste from backed tile which is cut and grinded for correctness is also re-used for manufacturing)
After passing the screen and magnetic purification, slurry is then pumped with high pressure pump to a silo through a nozzle which have small holes in it.
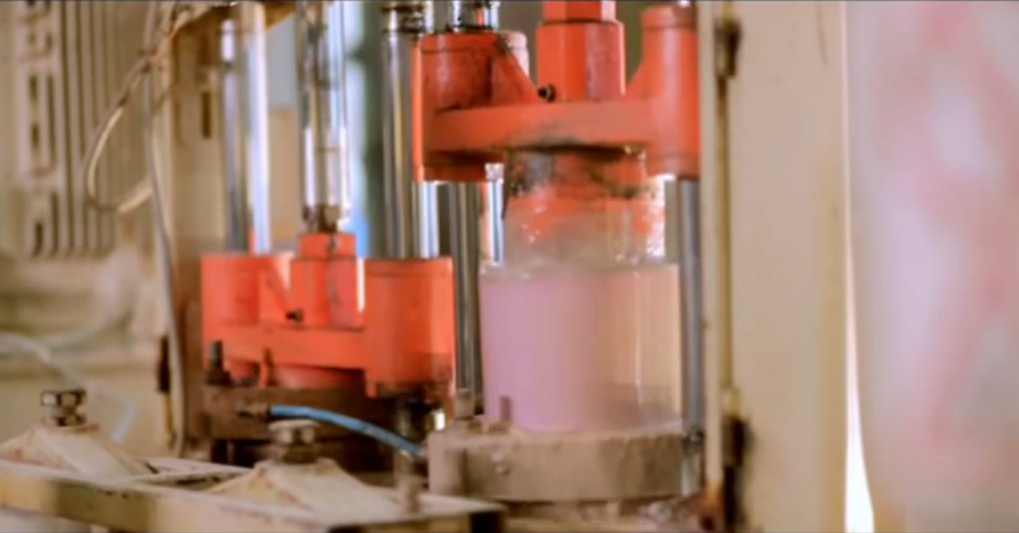
The spraying of slurry into a silo is done along with passing hot air into it. Spraying action and hot air pass makes the slurry to reduce its moisture from 33 to around 5 to 6 % which forms a finest granules of clay which are slightly moist. After formation of granules they are further moved to pressing machine which shape the tile body. The hot air pass and spraying of clay is done in control way to ensure the correct sizes of grains.
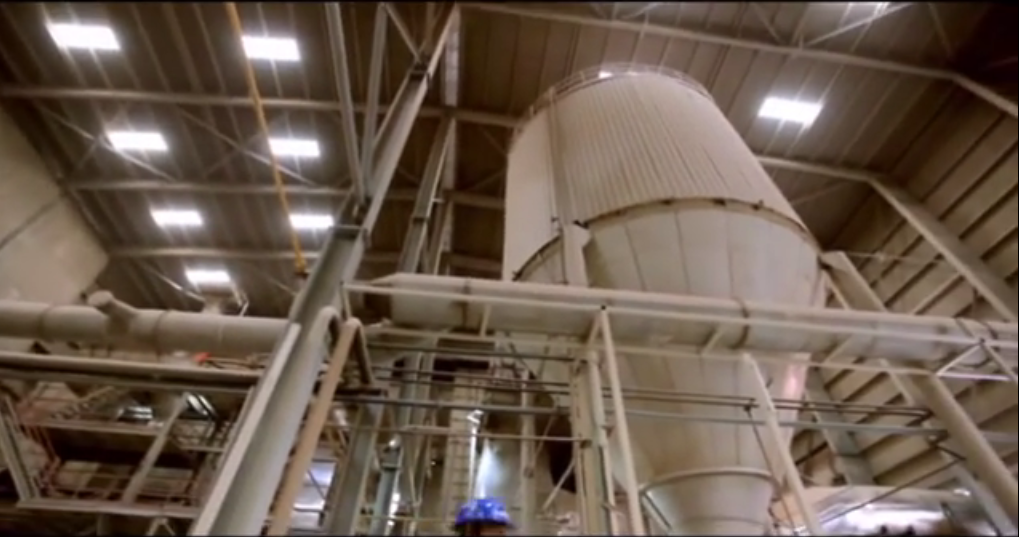
The finest clay powder is then sent to a pressing machine via conveyor.
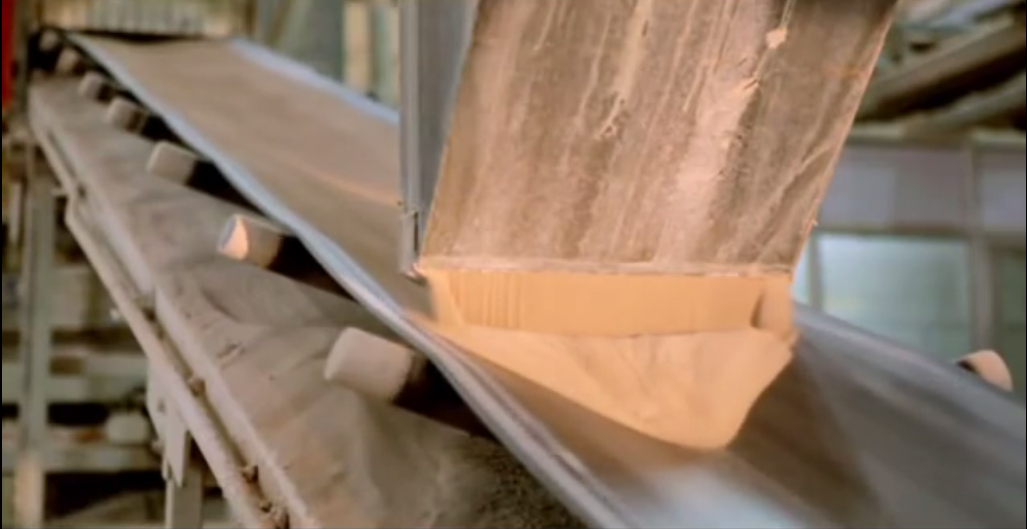
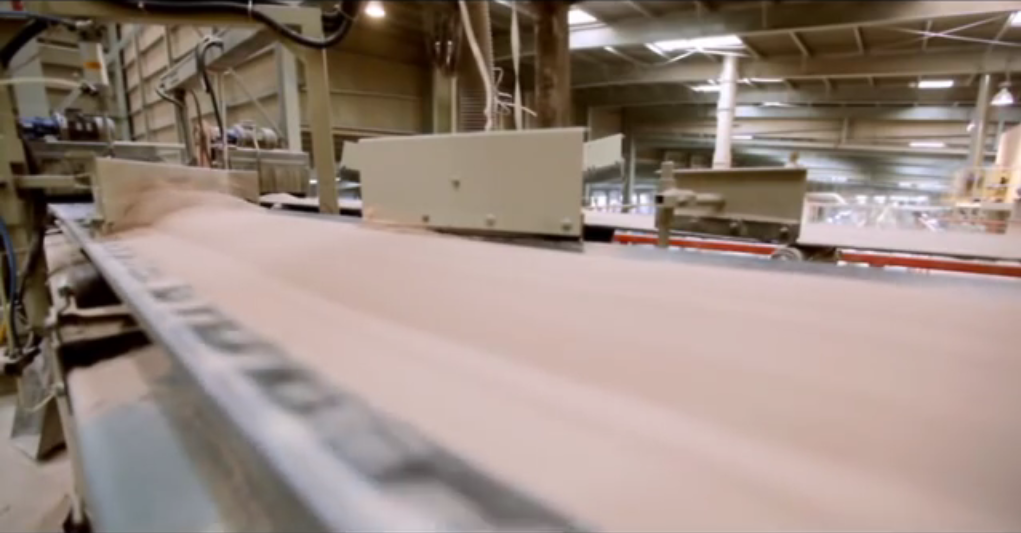
At the pressing machine the properties of tile which to be manufactured are decided, Ceramic tiles are made by pressing powder into the mould at low pressure and vitrified tiles are made by pressing powder into mould at slightly high pressure.
The classification of the any tile is based on its water absorption property which comes from this process. Pressing at high pressure ensure the extra amount of powder to be pressed in same volume of tile creating lesser voids in base tiles which corresponds to low water absorption and vice a versa.
For ceramic tiles the pressing of powder is done at 450 bars of pressure and for vitrified tiles pressing is done at 550 bars of pressure
At pressing machine, we can mould any size tile by providing specification and making arrangements of mould by simply programming it with all data.
Once the command is given, a fully automatic pressing machine fills the mould with moist powder of clay and presses it to required pressure and sends it forward through roller conveyor for further processing machine.
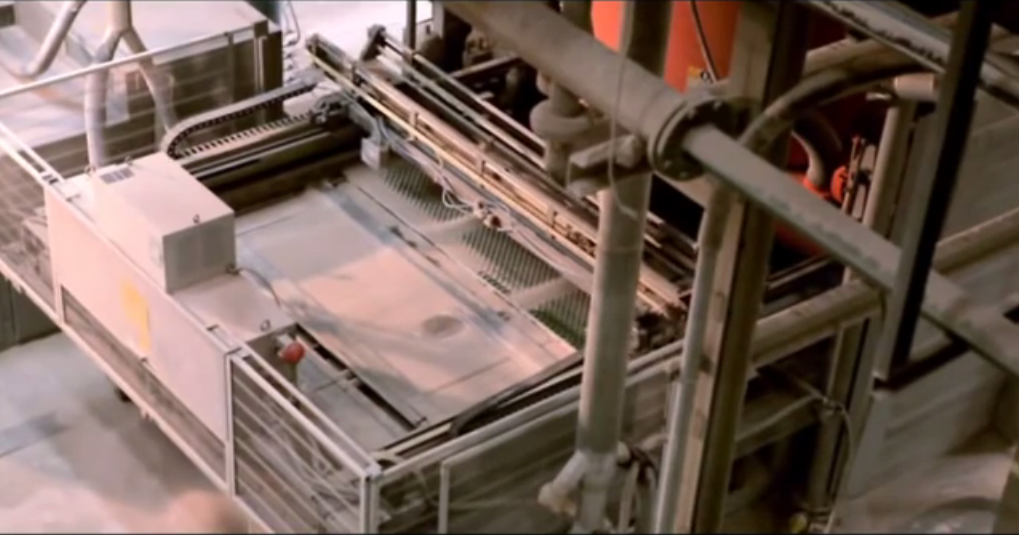
The push tile further here is called as green tile or biscuit.
We can have any shape in the back of tile and can be given in the mould, the top of the tile is plain or have designs on it (rustic tiles) to give the feeling of natural stone.
Rustic finish tiles are slightly costlier as the surface is not plain and the process of its topping do add additional costs but it gives a natural rock filling on top of it.
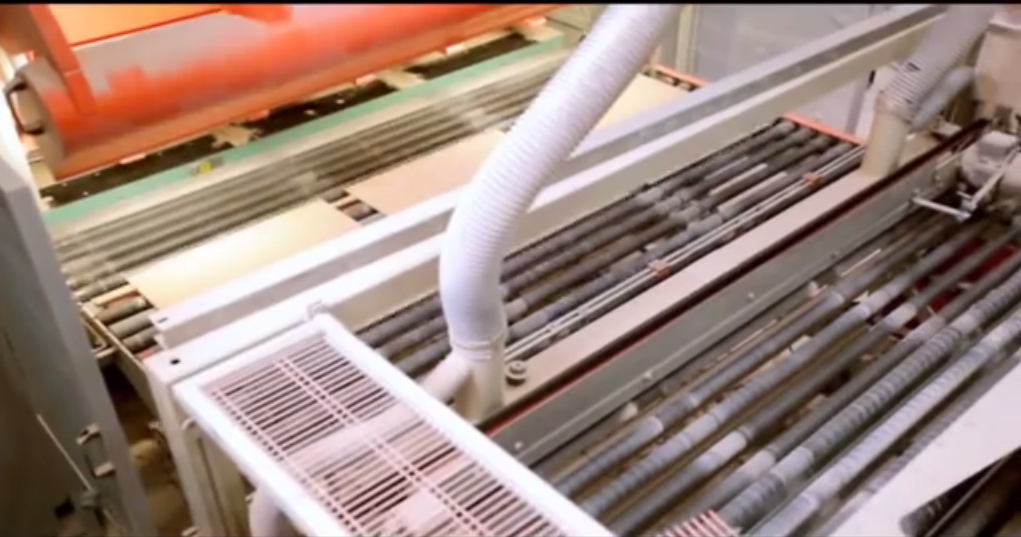
Must know – the size of the moulded tiles is always more than that of required size, generally they are made 15mm + on higher size coz during pressing, there is a chance that tile ends may lift upwards and in further processes may get some defects which can be nullify by cutting it after topping / printing.
The color of biscuit or green tile or the back of tile which is not visible, depends on the properties of the clay and mostly they are brownish or whitish.
So next time when you get two batches of tiles and if there back color varies, then either that tiles are not manufacture at same factory or there is change in source of clay.
The green tiles then further goes from a drier which removes it moisture content completely.

Once the tiles are reached on other end of drier, they are completely dry and does not have any moisture in it and ready for further processing.
The green tiles are tested for its flexure strength to ensure the quality of batch.
Dried tiles then coated with engobe, glaze and sent forward for printing. It can be either printed with rotary drum or digital printing machine.
Here onwards for each step of coating tile is first coated with adhesive and then air dried and each coating is done.
The green tile is then goes through a conveyor where adhesive is sprayed on it and air dried with fan.
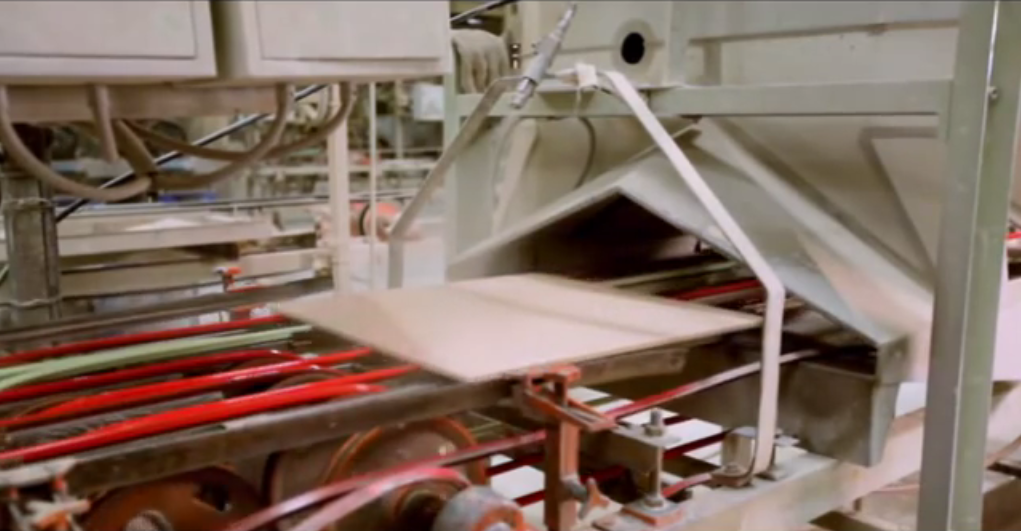
After this the engobe and glaze is applied on the tile surface.
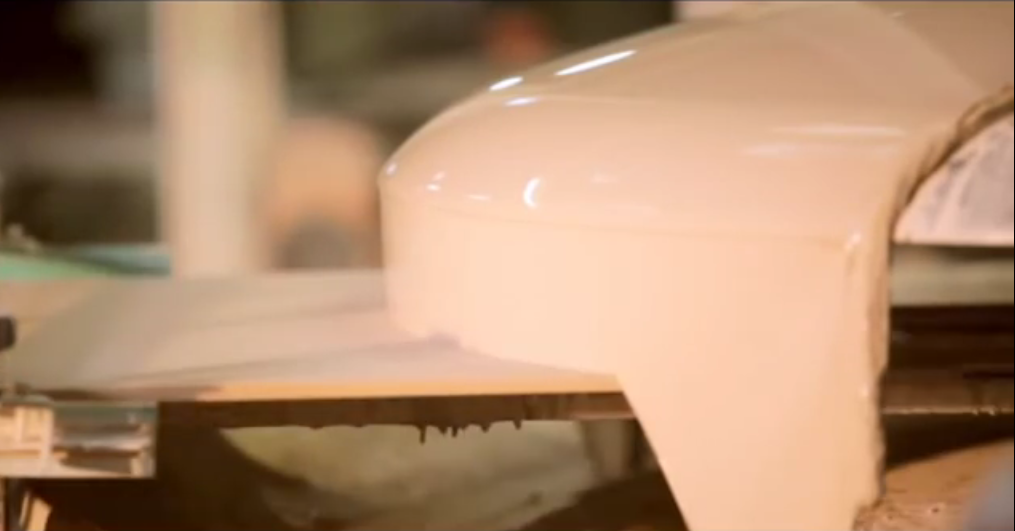
Engobe is the main layer on the tile surface which ensure no leakages from top to back of tile or from back of tile to the top surface (it’s just like a waterproofing coat). When you see a wet patches on tile surface then it’s clear indication of improper engobe application on it.
After engobe and glaze application tile is further moved to a printing assembly, it might be a roto type drum printer which gives color in 4 or more layer with adhesive application and drying before printing each layer.
In roto drum printer a color minerals are flowing through drums and when tile passes from the below of drum surface a layer of minerals is printed on it (just like how we apply paint on wall surface with roller brush)
Below photo shows assembly of 4 roto drum printer.
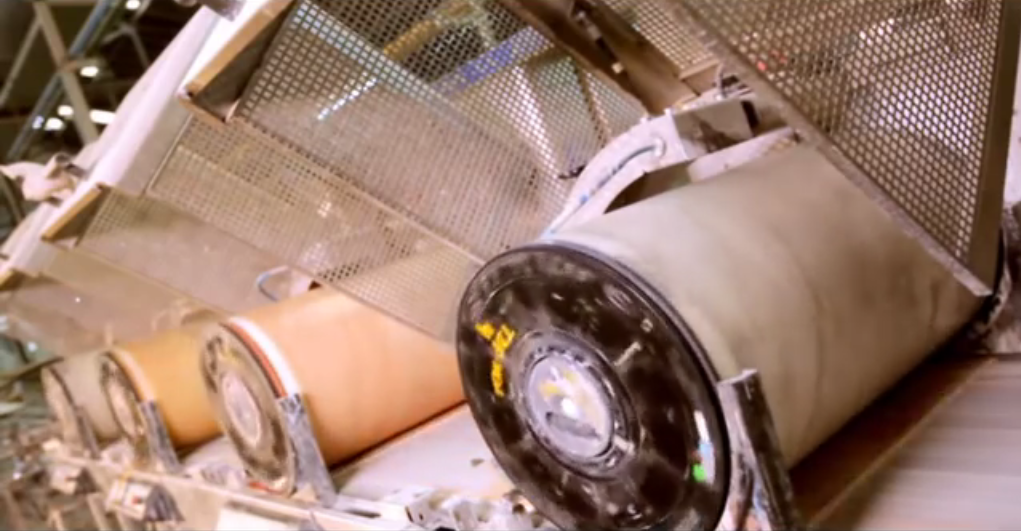
There are two technologies to print the design on tile surface
Roto Drum printer – As it’s a rotating drum which impress the color on tile surface, we can’t make a same design print on each tile surface and all tiles have different combination of surface texture (more likely they looks same), with this technology we cannot have fancy or more designs printed on it. This is use to give finish on the flat or rustic surface tiles.
Digital printing – In digital printing we can mimic almost any style, color combination and any type of surface finish look (we can make it as to look like wood, aluminium etc). After application of englobe the tiles are sent through a giant digital printer where the program automatically prints the design on each tile surface as per the design, with this technology we can print anything on tile surface, we can make a your photo printed on tile or printed in parts on tile which makes combination of 12 tiles to show what is the photo.
After completion of printing on tile surface, the automatic laser guided robots stack them and move to a kiln where heating of tiles is done.
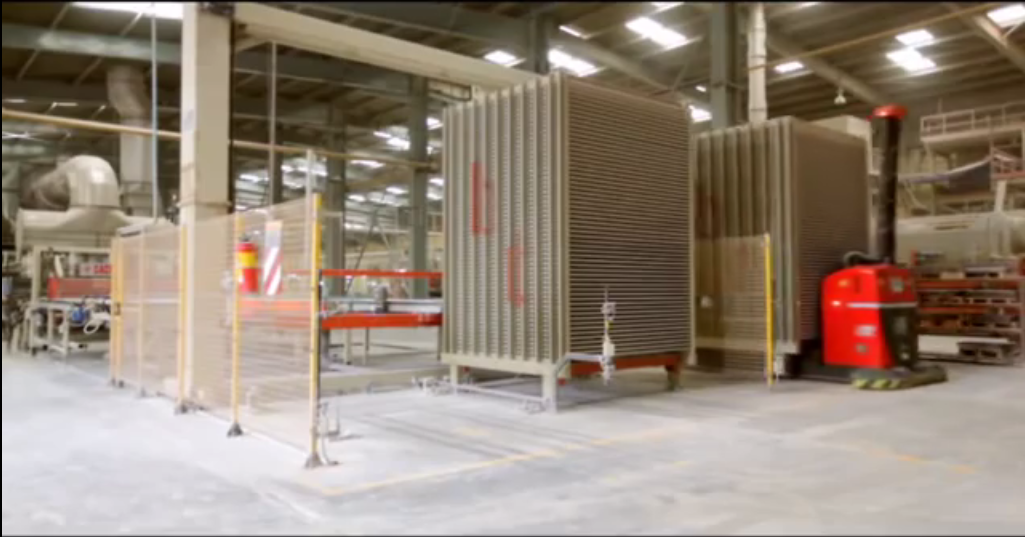
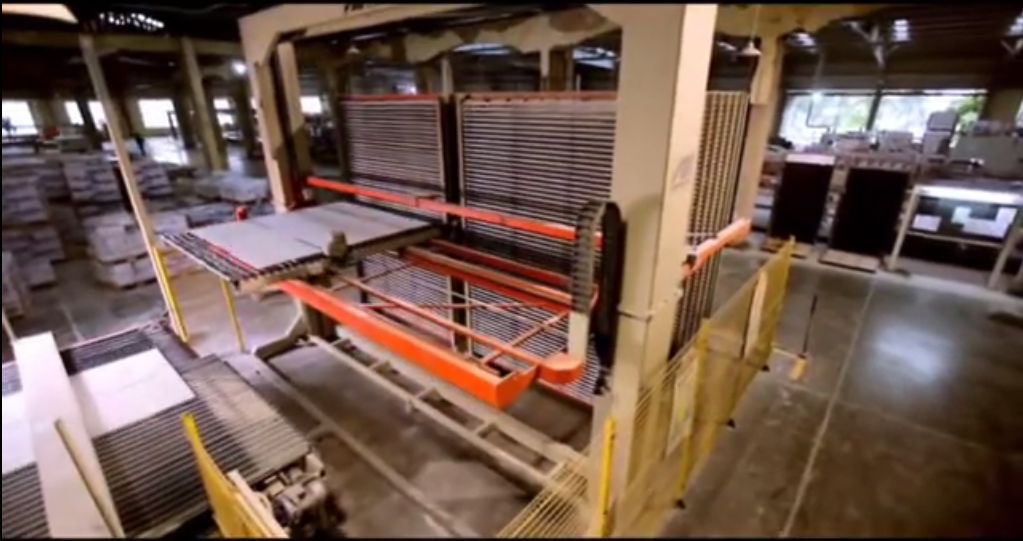