Construction Joints location, placing and preparation procedure
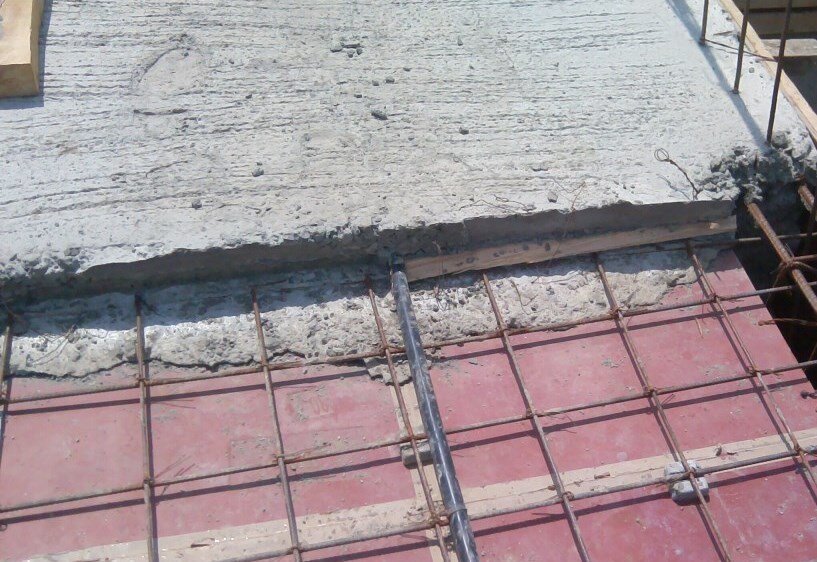
Location and Placing
a) Construction joints occur wherever concreting is stopped or delayed and hardened. Fresh concrete is subsequently placed against hardened concrete.
b) Usually, locations of construction joints are predetermined and shown on plans. In case it becomes necessary, due to stoppage of work at site, to install a joint elsewhere, consult the design engineer or senior engineer and plan the formation of the joint after careful consideration.
c) Horizontal construction joints occur at levels between lifts. (e.g.) in walls, columns..
d) Vertical joints occur where the structure is of such length that it is not feasible to place the entire length in one continuous pour (e.g.) slabs.
e) Construction joints in beams should be in the center or within the middle third of the span (where the shear is least). If this is not possible , provide the joint at the center of the support . The face of the joint should be vertical.
f) If the joint in a slab is made normal to the main reinforcement it should be placed at the center of the span. If the joint is made parallel to the main steel, it may be placed anywhere but the distance of the joint from the edge of a parallel tee-beam should be atleast eight times the thickness of the slab.
g) Construction joints in pavements should be located at planned expansion or contraction joints.
h) Reinforcement steel should be continuous across a construction joint, otherwise, dowels should be provided.
i) Provide stoppers for stopping the concrete or trim the edge surface so as to form the construction joint in a straight line.
j) Keys may be provided at the joints to ensure proper bond. A vee or a beveled rectangular strip can be used as a grade strip to form a groove at the construction joints. Take care to remove the strip used for providing key before the concrete hardens.
k) Water stops should be installed at the joints if leakage of water through the joint must be prevented.
l) Water gain, or bleeding, is objectionable , especially on a horizontal construction joint where a strong and tight bond is needed. Usually, a workable mix with a reduced quantity of coarse aggregate will be used for the first few batches to assure the absence of honeycomb at the bottom of the form. Reduce the mixing water to workable minimum to avoid water gain. If water accumulates even then, reduce the mixing water further.
Preparation of the joint and concreting:
Purpose
Removal of “ Laitance” from the old concrete surface is the main objective of the preparation of the construction joint , which in turn helps in achieving excellent surface bonding with newly placed fresh concrete . Construction joints can be prepared in the following ways
1. Hacking the old joints for removal of laitance .
2. Usage of surface retarder prior to placing fresh concrete and subsequent washing with water after hardening of concrete on form removal.
3. Application of Bonding agents.
Hacking of joints
a) The first step in preparing a joint is to remove any laitance, scum, or porous concrete by hacking. If care had been taken to remove these deposits before the concrete has fully hardened , then hacking needs to be done just to remove the few portions that may have been passed over. Otherwise, hacking should be continued until the old face is entirely removed. Then, scrub the exposed concrete with a wire brush to remove all loose mortar and stone.
b) For vertical construction joints, after hacking has been done , clean and wet the surface thoroughly and apply rich cement slurry on the surface before it is dry. Fresh concrete should be placed over this surface and should be worked and consolidated properly to ensure a good bond.
c) For horizontal joints, clean and wet the surface thoroughly after hacking. The shuttering should be tight enough to prevent leakage between the face of the timber and the old concrete. Cover the joint surface with a freshly mixed mortar (10 to 15 mm thick) composed of cement and sand in the same ratio as in the concrete mix but not leaner than 1:2. Place a layer of fresh concrete not exceeding 150 mm thickness on this surface and vibrate it well before placing the next layer.
Application of Surface retarder
Usage
Surface retarder produces exposed aggregate surface concrete finish in face up and face down and creates effective bonding to newly placed concrete with old concrete.
Surface retarders can be applied to all types of form work materials like steel, timber and glass fiber. It mainly retards the hydration of cement at the surface matrix of the concrete and exposes the aggregate surface to a depth of 4 to 10 mm depends on application after removal of top mortar build-up.
Application procedure
1. Moulds and formworks to be cleaned and dry before application.
2. A coats of surface retarders to be applied on to the formwork and for absorbing formwork 2 coats to be given for effective performance.
3. It should be applied using a spray, or brush or roller to get even and effective coverage as specified by the manufactures.
4. Before concrete is placed in the moulds , the surface retarder should be dry. It takes 15 to 60 minutes for effective drying depending on the ambient temperature.
5. On stripping the formwork the retarded surface of the concrete can be exposed either by brushing or by water washing.
6. If water washed it should be carried out using high pressure water jet of 5 to 10 N/sq.mm., also use a wire brush to remove all the loose particle.
After exposure and before placing the subsequent concrete a layer of cement sand mortar not leaner then 1: 2 may be applied to 10 to 15 mm thickness and concreting operations continued.
Bonding agents
Even though bonding agents are specified for treatment of construction joints by many clients for bonding old concrete to new concrete, it is not advisable to use the same for construction joint treatment. The reasons are
1. The pot life after mixing is very limited .In general 3 to 4 hours.
2. Forms to be placed within the pot life, and concreting to be commenced with in the expiry of pot life.
3. Since due to less handling time and faster setting time, the applied bonding agents instead of bonding fresh concrete to old concrete sets and from a thin separation (lamination) between layers.
4. Bonding agents are useful for repair works where the rectification’s can be taken up immediately after application, So, bonding agents are not recommended for constriction joint treatment due to less handling time.
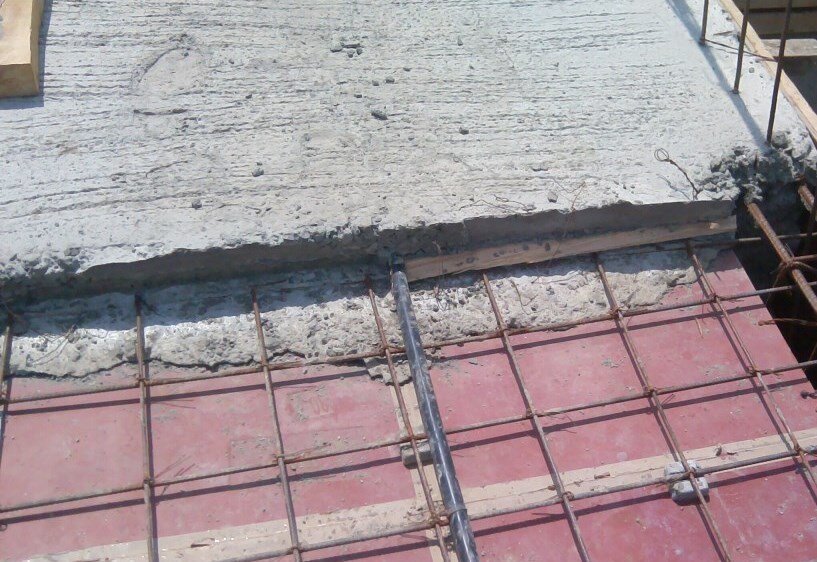
Location and Placing
a) Construction joints occur wherever concreting is stopped or delayed and hardened. Fresh concrete is subsequently placed against hardened concrete.
b) Usually, locations of construction joints are predetermined and shown on plans. In case it becomes necessary, due to stoppage of work at site, to install a joint elsewhere, consult the design engineer or senior engineer and plan the formation of the joint after careful consideration.
c) Horizontal construction joints occur at levels between lifts. (e.g.) in walls, columns..
d) Vertical joints occur where the structure is of such length that it is not feasible to place the entire length in one continuous pour (e.g.) slabs.
e) Construction joints in beams should be in the center or within the middle third of the span (where the shear is least). If this is not possible , provide the joint at the center of the support . The face of the joint should be vertical.
f) If the joint in a slab is made normal to the main reinforcement it should be placed at the center of the span. If the joint is made parallel to the main steel, it may be placed anywhere but the distance of the joint from the edge of a parallel tee-beam should be atleast eight times the thickness of the slab.
g) Construction joints in pavements should be located at planned expansion or contraction joints.
h) Reinforcement steel should be continuous across a construction joint, otherwise, dowels should be provided.
i) Provide stoppers for stopping the concrete or trim the edge surface so as to form the construction joint in a straight line.
j) Keys may be provided at the joints to ensure proper bond. A vee or a beveled rectangular strip can be used as a grade strip to form a groove at the construction joints. Take care to remove the strip used for providing key before the concrete hardens.
k) Water stops should be installed at the joints if leakage of water through the joint must be prevented.
l) Water gain, or bleeding, is objectionable , especially on a horizontal construction joint where a strong and tight bond is needed. Usually, a workable mix with a reduced quantity of coarse aggregate will be used for the first few batches to assure the absence of honeycomb at the bottom of the form. Reduce the mixing water to workable minimum to avoid water gain. If water accumulates even then, reduce the mixing water further.
Preparation of the joint and concreting:
Purpose
Removal of “ Laitance” from the old concrete surface is the main objective of the preparation of the construction joint , which in turn helps in achieving excellent surface bonding with newly placed fresh concrete . Construction joints can be prepared in the following ways
1. Hacking the old joints for removal of laitance .
2. Usage of surface retarder prior to placing fresh concrete and subsequent washing with water after hardening of concrete on form removal.
3. Application of Bonding agents.
Hacking of joints
a) The first step in preparing a joint is to remove any laitance, scum, or porous concrete by hacking. If care had been taken to remove these deposits before the concrete has fully hardened , then hacking needs to be done just to remove the few portions that may have been passed over. Otherwise, hacking should be continued until the old face is entirely removed. Then, scrub the exposed concrete with a wire brush to remove all loose mortar and stone.
b) For vertical construction joints, after hacking has been done , clean and wet the surface thoroughly and apply rich cement slurry on the surface before it is dry. Fresh concrete should be placed over this surface and should be worked and consolidated properly to ensure a good bond.
c) For horizontal joints, clean and wet the surface thoroughly after hacking. The shuttering should be tight enough to prevent leakage between the face of the timber and the old concrete. Cover the joint surface with a freshly mixed mortar (10 to 15 mm thick) composed of cement and sand in the same ratio as in the concrete mix but not leaner than 1:2. Place a layer of fresh concrete not exceeding 150 mm thickness on this surface and vibrate it well before placing the next layer.
Application of Surface retarder
Usage
Surface retarder produces exposed aggregate surface concrete finish in face up and face down and creates effective bonding to newly placed concrete with old concrete.
Surface retarders can be applied to all types of form work materials like steel, timber and glass fiber. It mainly retards the hydration of cement at the surface matrix of the concrete and exposes the aggregate surface to a depth of 4 to 10 mm depends on application after removal of top mortar build-up.
Application procedure
1. Moulds and formworks to be cleaned and dry before application.
2. A coats of surface retarders to be applied on to the formwork and for absorbing formwork 2 coats to be given for effective performance.
3. It should be applied using a spray, or brush or roller to get even and effective coverage as specified by the manufactures.
4. Before concrete is placed in the moulds , the surface retarder should be dry. It takes 15 to 60 minutes for effective drying depending on the ambient temperature.
5. On stripping the formwork the retarded surface of the concrete can be exposed either by brushing or by water washing.
6. If water washed it should be carried out using high pressure water jet of 5 to 10 N/sq.mm., also use a wire brush to remove all the loose particle.
After exposure and before placing the subsequent concrete a layer of cement sand mortar not leaner then 1: 2 may be applied to 10 to 15 mm thickness and concreting operations continued.
Bonding agents
Even though bonding agents are specified for treatment of construction joints by many clients for bonding old concrete to new concrete, it is not advisable to use the same for construction joint treatment. The reasons are
1. The pot life after mixing is very limited .In general 3 to 4 hours.
2. Forms to be placed within the pot life, and concreting to be commenced with in the expiry of pot life.
3. Since due to less handling time and faster setting time, the applied bonding agents instead of bonding fresh concrete to old concrete sets and from a thin separation (lamination) between layers.
4. Bonding agents are useful for repair works where the rectification’s can be taken up immediately after application, So, bonding agents are not recommended for constriction joint treatment due to less handling time.