Cement
It is made up of limestone by crushing it into powder and modifying its some properties.
Strength of the cement mainly depends on the quality of lime stone quarry. Blackish limestones have better properties than whitish limestone. It does not mean a faint color cement lack in strength properties but darker color always performs well on strength properties.
Clay or shale so called, are generally “Bentonite” and “Laterite” mix with Limestone to form a clinkers.
There % in mix is around 3 to 4% and rest is lime, % varies base on the quality of material and desired property.
Here it goes though the high temperatures of 1400 to 1600 degree centigrade’s and then it’s cool down below 100 degree till the end of kiln and at cooling unit
Temperature plays important role in forming the compound of cements, Clay helps to liquidation of limestone’s and forming clinker of size 1mm to 25mm through rolling effect of kiln.
IS Codes permitting the Performance improver additive up to 5 %, in the production of Ordinary Portland Cement.
Performance improver additives are;
FlyAsh
Granulated slag
Silica fume
Limestone
Rice husk ash
Metakaolin
So while doing mix designing consider this and stick to one brand of cement or do trials with brands you intended to use in your project.
In production of cement the gypsum is added either solid or liquid with clinker in ball mill. % of gypsum added depends on the properties of cement which are required.
After grinding it to the required fineness then cement is stored in the silo. This cement then sent to us either in bags or through cement bulkers.
The clinkers, which lake into the desired properties are use to produce a 33 Grade cement.
Production of the 43 and 53 grade cement is same; the difference is the fineness of the grinded powder.
The Total Production system is controlled automatically, for the quality of the product at each stage and adjusts the proportions base on the desired properties.
Quality of the product from clinkers to cement is tested automatically at fixed intervals using robotics automation, conveyors, capsules for collecting samples etc.
In case when, a transport conveyor from the control room do not place sample in testing machine or have some problem with x ray machine automation, we can collect the sample and test it on machine manually
The cement we receive is tested for all its properties from starting to end of the processes.
QC X rays make life easier, no need to wait for a day, 3 days, 7 days or 28 days. Within fraction of seconds we get the all details of the material which are tested.
This is my photo with cube of clinker produced, tested for its strength parameter and I am standing at the quarry from where the limestone’s goes inside of it
Hope you like my article and understood the cement manufacturing process.
I am not expert in the field of Cement Manufacturing; I wrote what I understood during my visit to plant.
If you find something written by me is not correct please reply here, so that I can correct it and this article will help others to understand what cement is and how it’s made.
Images are compress to small size so that it can load faster and everyone able to understand it, If you want images for putting into your presentation, I can provide it.
Some photos of FLSmidth equipments are taken from web, give credit to them for those images (They are the leader in making automation).
You can appreciate me either by liking this post or replying to this thread.
It is made up of limestone by crushing it into powder and modifying its some properties.
Strength of the cement mainly depends on the quality of lime stone quarry. Blackish limestones have better properties than whitish limestone. It does not mean a faint color cement lack in strength properties but darker color always performs well on strength properties.
Clay or shale so called, are generally “Bentonite” and “Laterite” mix with Limestone to form a clinkers.
There % in mix is around 3 to 4% and rest is lime, % varies base on the quality of material and desired property.
Lime stone crusher situated in quarry to make a small size aggregates and then transported to stacking location by conveyor.
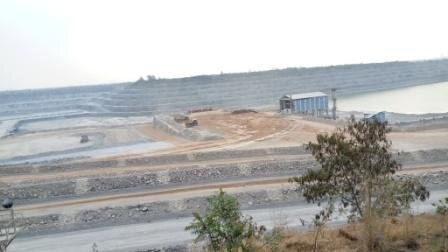
Lime stone stacked in piles
Clays are too stacked you can see on further side of conveyor
Stack reclaimer which does gradation and send lime stones to crusher.
Material then feed to silo by screening.
Screen for removing unwanted materials
Crushing Area
After adding % ingredient mix and calcinations process it is sent into rotary kiln
Here it goes though the high temperatures of 1400 to 1600 degree centigrade’s and then it’s cool down below 100 degree till the end of kiln and at cooling unit
Temperature plays important role in forming the compound of cements, Clay helps to liquidation of limestone’s and forming clinker of size 1mm to 25mm through rolling effect of kiln.
Temperature control unit
After formation of clinkers they are store in silo or directly sent to the production unit by conveyor
At production unit there is a ball mill which grinds all ingredients into finer material
Flyash: being poured into silo for production
IS Codes permitting the Performance improver additive up to 5 %, in the production of Ordinary Portland Cement.
Performance improver additives are;
FlyAsh
Granulated slag
Silica fume
Limestone
Rice husk ash
Metakaolin
So while doing mix designing consider this and stick to one brand of cement or do trials with brands you intended to use in your project.
In production of cement the gypsum is added either solid or liquid with clinker in ball mill. % of gypsum added depends on the properties of cement which are required.
Gypsum feed for production
Clinkers feed for production
After grinding it to the required fineness then cement is stored in the silo. This cement then sent to us either in bags or through cement bulkers.
The clinkers, which lake into the desired properties are use to produce a 33 Grade cement.
Production of the 43 and 53 grade cement is same; the difference is the fineness of the grinded powder.
The Total Production system is controlled automatically, for the quality of the product at each stage and adjusts the proportions base on the desired properties.
The whole process is controlled in the control unit which displays all processes
Quality of the product from clinkers to cement is tested automatically at fixed intervals using robotics automation, conveyors, capsules for collecting samples etc.
Robotics collecting sample received from conveyor
After making the test plate it serves to x ray machine for analyzing the composition of it
In case when, a transport conveyor from the control room do not place sample in testing machine or have some problem with x ray machine automation, we can collect the sample and test it on machine manually
The cement we receive is tested for all its properties from starting to end of the processes.
QC X rays make life easier, no need to wait for a day, 3 days, 7 days or 28 days. Within fraction of seconds we get the all details of the material which are tested.
This is my photo with cube of clinker produced, tested for its strength parameter and I am standing at the quarry from where the limestone’s goes inside of it
Hope you like my article and understood the cement manufacturing process.
I am not expert in the field of Cement Manufacturing; I wrote what I understood during my visit to plant.
If you find something written by me is not correct please reply here, so that I can correct it and this article will help others to understand what cement is and how it’s made.
Images are compress to small size so that it can load faster and everyone able to understand it, If you want images for putting into your presentation, I can provide it.
Some photos of FLSmidth equipments are taken from web, give credit to them for those images (They are the leader in making automation).
You can appreciate me either by liking this post or replying to this thread.